Optimized inventory management in the process industry
Inventory is often considered “a necessary evil” in business which costs considerable time and money. Whether you have too little or too much of it, either way it negatively impacts your company’s bottom line. However, a company still cannot operate without it.
In the process industry, with its diverse product portfolio, inventory can be a particularly complex matter. In this article, we focus on the challenges of inventory management faced by companies in the process industry and explain how they can be solved with advanced analytics procedures.
Why is optimal inventory so important in the process industry?
Specific features of the process industry
The process industry mainly processes raw materials and ingredients which are then used to create a finished product. Production is based on formulas instead of parts, and recipes are used instead of a bill of materials. Most of the goods to be processed are in bulk resources or in liquid form. At the end of the product cycle, the products cannot be broken down into their individual ingredients, unlike a car, for example, which is made up of various parts.
Such materials and ingredients are frequently used in companies that produce bulk quantities of goods such as food, beverages, refined oil, gasoline, pharmaceuticals, chemicals and plastics.
Particular storage challenges
Many of these ingredients and materials have a short shelf-life and can be toxic or hazardous so storing, managing and keeping track of them is particularly important. Above all, certain factors must be observed during storage and handling:
Ingredients must be stored at the right temperature (e.g. cold storage for specific medicaments). Different types of ingredients or materials cannot be stored together, distances between certain products must be observed, some products cannot be stored too close to production facilities or other company buildings for safety reasons. It is therefore crucial that companies have an overview of what is in storage and how much of it, what has to be stored where, how long they have been there and how long they can remain until they need to be processed.
Failure to manage inventory efficiently can lead to a myriad of problems: higher costs, more waste, bottlenecks, delays in delivery, increased safety risks, as well as fines if safety regulations are not observed. Yet, many companies still struggle to manage inventory properly, and this leads to problems in other areas such as procurement, production and logistics.
Getting the balance right
When planning inventory levels, the golden rule is not too much, but not too little. However, getting the balance right. can be challenging. Companies in the process industry need to keep a constant level of stock in their warehouses in order to prevent delays in delivery of vital goods and components. On the other hand, storage costs should be kept as low as possible. Overstocking and understocking are common inventory problems.
Overstocking
Overstocking mainly occurs when companies misjudge customer demand or procure on a just-in-case basis.
Let us take the events of the last few years as a classic example of overstocking. Where companies had previously implemented the just-in-time concept, the huge demand for products manufactured in the process industry induced many companies to move away from the approach and maintain buffer stock during the pandemic and resulting supply chain disruptions. However, the hoarding eased off and the energy crisis, political upheavals and rising inflation since then have led to a decrease in consumer spending and a slump in demand, leaving companies with goods and materials that they cannot shift.
Surplus inventory ties up capital as more storage space is needed. In the process industry, for example, much of the inventory must be held in tanks and drums for liquids, silos and warehouses for solids, cylinders for gases, the procurement and maintenance of which is very costly.
Furthermore, much of the inventory may also be subject to quality tests at set intervals. This is a waste of time and resources if there is too much sitting on the shelves.
Too much stock in warehouses also increases risks such as leaks, explosions, health hazards, etc. Other items can expire quickly and have to be sold at a loss. At worst, they can no longer be used in production and have to be disposed of. This entails further costs, especially if they are hazardous to health and the environment and call for special disposal. This, in turn, does nothing to reduce a company’s carbon footprint, making it even more difficult to meet prescribed environmental guidelines.
Understocking
The less you have lying around in your warehouse, the better. However, there still has to be enough of what is needed. Understocking is just as bad for business as overstocking.
Understocking is also a consequence of poor inventory management procedures. However, supply chain disruptions, as we have witnessed in the last few years, can also lead to empty warehouses, just as much as the failure to accurately predict the demand for raw materials, for instance. While the just-in-time concept had been a popular one in the business world for decades, large-scale disruptions such as the COVID-19 pandemic or climate crises have proven that it is not foolproof.
The consequences of having an inventory shortage are production bottlenecks which waste personnel resources, run up higher costs, cause delivery delays and ultimately lead to dissatisfied customers. Depending on the severity of the delays, customer loyalty takes a hit, making a company lose its competitive edge in a market which is already challenging enough. This is even more so in the process industry because so many of the goods they produce are essentials – e.g. food, medicine, oil and gas.
Just-in-time vs. Just-in-case
Companies which adopt the just-in-time strategy are focused on avoiding excess inventory and lean production processes. The just-in-case strategy is used to prevent a company running out of stock when there is a sudden increase in demand, for instance. While both strategies have their advantages, there also drawbacks.
Just-in-time prevents overstocking as well as over production so that resources can be deployed more efficiently in other areas. Just-in-time means less waste and reduced costs as companies only keep stock that is needed for production. On the other hand, they do not have sufficient supplies in the event of a sudden increase in demand, if suppliers cannot meet their obligations on time, or there are unforeseen circumstances such as shipping delays.
Just-in-case enables companies to meet any level of demand which gives them a competitive edge as their supplies are constantly in stock. This also allows them to continue production while they wait for stock to be replenished. Procurement costs are often lower since they can take advantage of bulk discounts or buy raw materials when prices are at their lowest. At the same time, while just-in-case saves costs in other areas, storage costs for more inventory are higher. There is also the risk of goods spoiling or becoming obsolete if they do not sell as expected.
To sum up: Just-in-time only works when the conditions are optimal: in industries where there are few serious demand fluctuations and guaranteed supplier reliability. Just- in-case can promote growth and flexibility but can also lead to problems elsewhere if demand falls and goods cannot sell.
Neither concept alone will be without its flaws. A hybrid method combining both can be feasible. Having Just-in-time for materials and ingredients which are not required on a regular basis; just-in-case for items with a long shelf-life and where demand remains stable and predictable.
Advanced Analytics as a solution to inventory challenges
Finding the right strategy is critical to ensure a company has the right inventory levels. However, taking various measures in other areas can also go a long way towards improving inventory management and planning. More supply chain transparency is an absolute must. Being able to identify problems in all areas – from the supplier to the end customer – can considerably facilitate your inventory planning because you have a far better overview of what will be needed and when.
Optimized inventory management which helps a company improve its stock availability, reduce its inventory levels and costs and thus meet demand changes and supply chain challenges is not possible with manual planning using spreadsheets. By applying optimization software which is based on advanced analytics methods such as Predictive and Prescriptive Analytics, intelligent solutions to complex inventory planning issues in the process industry can be deployed fast, easily and efficiently.
More interesting articles
Take your inventory to the next level with OPTANO
An optimization platform such as OPTANO uses all of a company’s available data to create a mathematical model of your business. This can map not only your inventory management but also your entire supply chain and production, taking all of your objectives, variables and constraints into consideration.
Different alternatives to a problem are analyzed and compared in what-if scenarios to find the best solution. For instance, what would be the result if a company switched from just-in-time or just- in-case, or vice versa? Would a hybrid method, i.e. combining the two, be more beneficial? To what extent would stocks be affected if a supplier cannot meet its commitments? Would there be enough buffer stock and to what extent would production plans need to be readjusted?
Applying the same data in various scenarios also allows you to forecast long and short-term demand. This provides valuable insights into your inventory planning. Not only does this considerably facilitate decision-making processes but it can help you to prepare and respond quickly to unexpected disruptions, for instance by adjusting inventory to account for different lead times and any changes to production schedules. You can identify which steps to take to prevent overstocking and understocking and determine how your inventory can be distributed across multiple warehouse locations for optimal effect. KPIs and reporting round off the optimization package.
If you want to learn more about how advanced analytics can help optimize your inventory management or other areas of your business, you can download our factsheet “Predictive und Prescriptive Analytics”.
Or why not talk to one of our consultants? Our team of optimization experts is just a phone call or e-mail away and is happy to answer any questions you may have on inventory optimization or any other planning issue.
Inventory: really a necessary "evil"?
It goes without saying that inventory management combined with the determination of stock levels is a necessity. However, this does not have to be evil. With the use of advanced analytics techniques and mathematical optimization, your warehouse and inventory can be managed efficiently.
Have you got your copy of our factsheet on this topic yet?
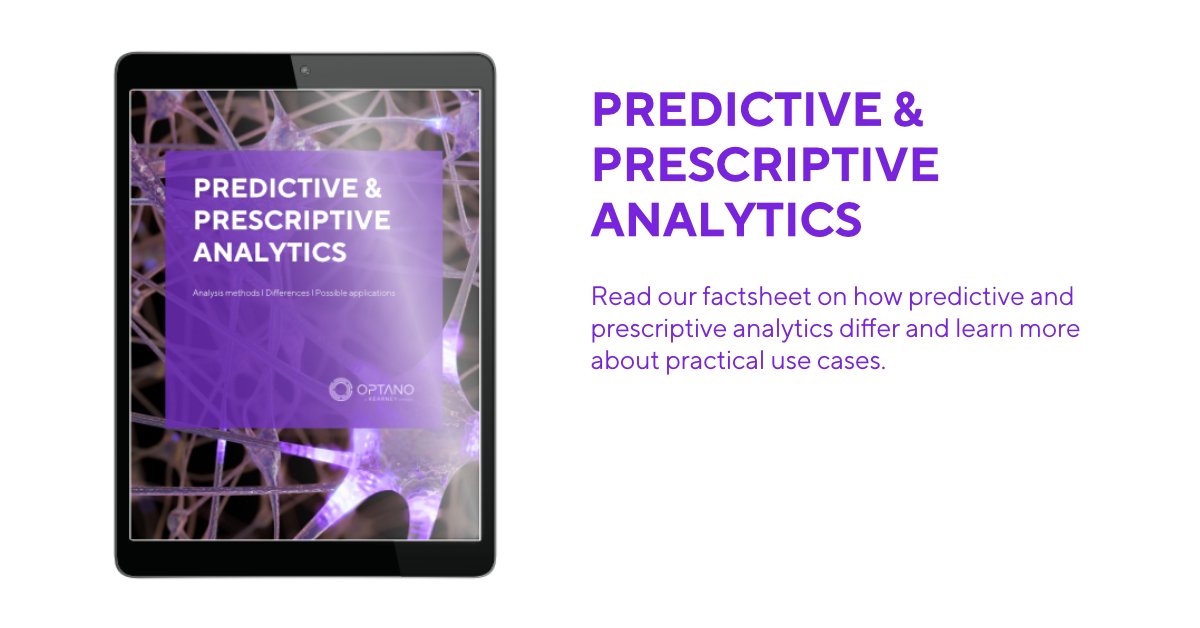
When it comes to optimizing processes, the terms predictive and prescriptive analytics come up again and again. As predictive and pre-planning analyses, both have their use cases.
In our factsheet, we show what exactly lies behind the terms predictive and prescriptive analytics, how they can be distinguished from each other, and what practical use cases there are.
To obtain our factsheet, all you need to do is enter your contact details in the space below. A pop-up window will then open to download the whitepaper. Please note that by providing us with your email address, you agree that we may contact you on this topic. You may revoke this agreement at any time by contacting [email protected].