Managing
bottlenecks
in production
As a student I once had a job during the summer holidays serving guests at a hotel and restaurant. I had to pour a lot of glasses of wine, yet back then I never paid much attention to the neck of the bottle and contemplated its function:
“A bottleneck literally refers to the narrowed portion (neck) of a bottle near its opening, which limits the rate of outflow. The narrower the neck is, the less liquid comes out. Without a bottleneck the rate of outflow would be considerably higher.” – Wikipedia.
In other words, the bottleneck prevents liquid from flowing freely so that, when being poured, it fills the glass slowly instead of spilling all over the table. Thankfully, the bottlenecks of wine, water and all other beverages is very narrow.
A bottleneck in production, on the other hand, is not as desirable. In this case, limiting the flow rate leads to delays in the entire production process.
Production bottlenecks and their impacts
Simply put, a bottleneck is a resource which has the highest utilization in the entire production process over a considered period of time and thus delays the workflow. It limits throughput, increases the lead time and ultimately sets a limit on the capacity of the whole production.
Or, put another way: even if the bottleneck resource runs at its maximum capacity, it cannot always process the material quickly enough in order to transfer it to the following production stage without a delay. Therefore, production bottlenecks frequently become apparent by the inventory before the respective production stage, the lack of processed
materials and idle phases in the downstream production stages.
A bottleneck has a major influence on the production as a whole because more time is required for the manufacturing process which drives up the costs. Apart from the loss of production efficiency, bottlenecks have an impact on your flexibility and adherence to delivery dates. At worst, they can have an adverse effect on the level of your customers’ satisfaction.
How does a bottleneck occur?
A production bottleneck can be attributed to various factors. The production infrastructure, staff and quality problems are just a few examples which can influence production:
Low processing capacity in the production infrastructure
For a production process to be efficient, it is essential to have a production infrastructure – i.e. machines and equipment – which is in unobjectionable condition. A bottleneck can occur, for instance, when the processing capacity of a machine or production facility is too low. There are several reasons for this: capacity has been too tight from the very beginning, equipment breaks down, must undergo maintenance or is too old to be put to use in production.
Lack of employees with the right skills
Employees who do not know how to use the production system or machines properly are unable to complete processes effectively. If a worker does not have the right qualifications or skills then he/she will likely need more time to do a job. A work station on which an unqualified employee is working can all too quickly become a bottleneck.
Quality problems
Many bottlenecks occur due to problems with the quality. Work which has not been done properly has to be done all over again. This slows down the processes and results in waiting periods and idle phases in the downstream production stages.
Eliminating the bottleneck
Once you have identified the causes of your production bottleneck, the next step is to restructure your production process to ensure a smooth workflow. This can involve improving processes as well as bringing in added capacity, introducing quality controls or sub-contracting.
Maximum capacity
Only if you have optimal throughput at the narrowest point can you also adapt all the other processes. Avoid standstills and keep the waiting and set-up times of your bottleneck resources at a minimum. Furthermore, the availability of the production stage can be improved with optimized maintenance and servicing cycles and measures.
Increasing capacity
If the maximum utilization of a bottleneck is insufficient, then it has to be increased. Faster throughput can be reached by creating more capacity. You may need additional machines (to create redundancy in case of a breakdown, for example), more or better qualified employees or more automation in production. Another option is to outsource part of your production.
Adjusting processes
The bottleneck determines the pace of your production: This can also mean that you will have to shut down preceding or subsequent process stages and lower the input here. This functions like the section of a very busy highway: By lowering the speed limit, the traffic continues to flow instead of to stall. This means that more vehicles can pass through the bottleneck.
Introducing quality controls
The bottlenecks caused by quality problems can be avoided by implementing quality controls. Even though this takes up more time in the short-term, controls do save time and ease the workflow in the long run.
All of these measures can result in the bottleneck shifting and that another resource in production now becomes the bottleneck. Planning and eliminating bottlenecks is a continuous process of improvement in any company – and this is where mathematical optimization can help.
Mathematical optimization for efficient measures
Once the causes of the production bottleneck have been identified, the right measures have to be taken in order to
eliminate it. Here, companies often have to consider what the best procedure is with a view to their business objectives.
For complex procedures such as production planning, applying analytical methods such as mathematical optimization is advisable. Creating production plans using Predictive and Prescriptive Analytics is based on a model which maps the entire production process – taking into consideration all objectives, resources, variables and constraints. Special solvers are used to help come up with the optimal solutions to the production problem. A close-meshed and repeated analysis of all these influencing factors enable problems to be identified early on and plans can then be readjusted quickly.
More interesting articles
OPTANO helps to identify the right measures
Planning software such as OPTANO creates the necessary transparency, provides alternatives on the best course of action to take and enables you to compare these in order to support you with data-driven decisions.
With OPTANO production it is possible to identify the right measures in order to achieve the desired objectives – soundly analyzed on the basis of all the data to be considered. In this way countless alternatives – from optimizing set-up times, increasing capacity to outsourcing production stages – can be analyzed and compared with one another in order to find the proven best solution. Whether it is tactical or operational planning, with OPTANO production plans can be generated quickly and easily in line with your requirements.
If you would like to learn more about how OPTANO can improve your production planning, simply download our factsheet “Advanced Production Planning”. If you have any further questions, then contact us. Our consultants are available to answer any of your questions on optimal production planning. Or why not e-mail us? We’ll get back to you as soon as possible.
Contemplating over a glass of wine
Who knows, when I enjoy a glass of wine in the future, I may briefly think about the wine’s rate of outflow and the lead times in production. On the other hand, maybe not. There are so many other subjects to philosophize on over a glass of wine…
Have you already got your factsheet on this topic?
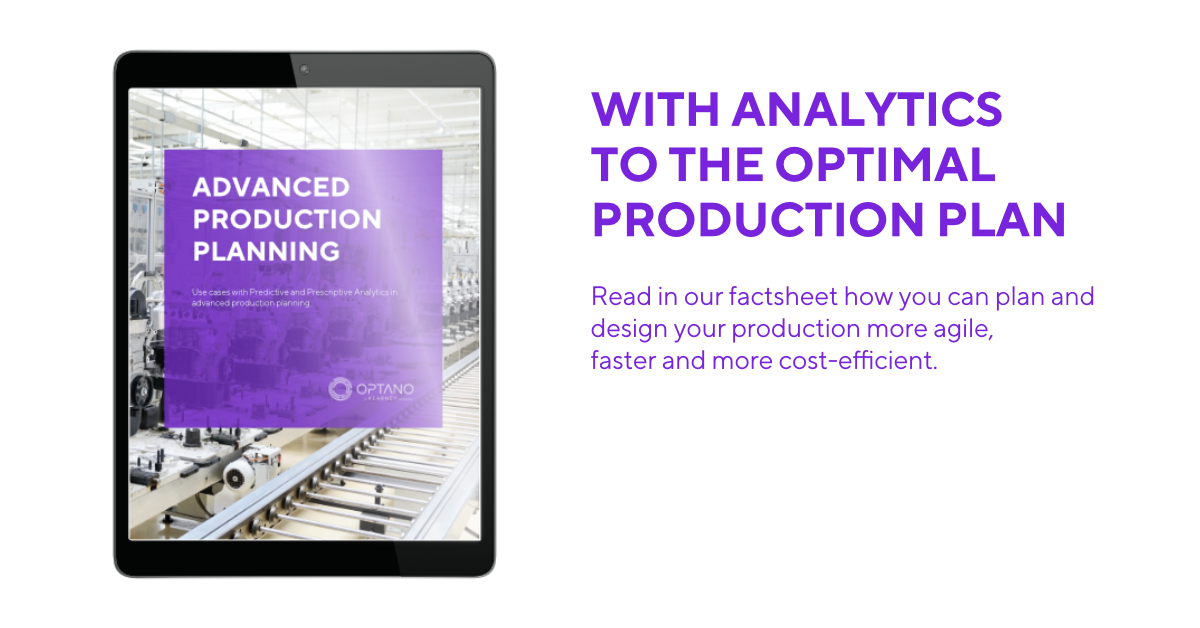
In our factsheet Advanced Production Planning we present some of the use cases of Predictive and Prescriptive Analytics in modern production planning which you can download here.
To obtain our factsheet, all you need to do is enter your contact details in the space below. A pop-up window will then open to download the whitepaper. Please note that by providing us with your email address, you agree that we may contact you on this topic. You may revoke this agreement at any time by contacting [email protected].