Saving electricity
in production
Perhaps you are also familiar with this phenomenon? Rooms that my children have entered during the dark months of the year can be recognized by the fact that the light is burning – regardless of whether the offspring in question is still in the room or not. This requires a watchful eye and a lot of micromanagement on my part. The principle applies: “Saving electricity is a Sisyphean task”! And this applies all the more when it’s not just about an unnecessarily well-lit home, but also about an energy-intensive production operation. In this article, we want to take a look at how manufacturing companies can save energy.
Electricity costs remain high
The good news first: thanks to the abolition of the german EEG surcharge in July 2022 and the reduction in electricity tax, electricity prices are currently at around the same level as in 2020. However, on closer inspection, direct costs have almost doubled since this year. It can therefore be assumed that the price level will rise rather than fall in future. Manufacturing companies should use this breathing space to implement concepts that will enable them to make sustainable energy savings. We would like to highlight a few options for this.
Electricity saving concepts
In recent years, more and more methods have been developed to help companies save energy. However, many of them are associated with high investments. We therefore want to start with a method that is comparatively easy to implement: peak load management.
Peak Load Management
We have already reported on this method in a separate blog article (click here). Nevertheless, we would like to reiterate the principle here: The electricity price for companies in Germany is made up of a basic price and a performance price. It is calculated by continuously measuring and documenting electricity consumption at short intervals of 15 minutes each over the course of a year. The performance price is calculated based on the highest average value achieved. In practice, this means that even a single peak load in the measurement period is sufficient to increase the demand charge in the billing year. The principle of peak load management was introduced in order to utilize the electricity grid as constantly as possible and to avoid sudden increases in consumption.
Peak loads can occur when several consumers are switched on at the same time – for example when production machines are started up in parallel. To avoid this, it is necessary to systematically record the power consumption of all devices in the company. This also applies to consumers that are not directly involved in production and require a lot of energy, such as air conditioning systems. The principle of peak load management is to avoid peak loads by cleverly distributing consumption (e.g. by starting up machines at different times) – as long as this does not impair production processes. Another option is load shedding, i.e. switching off consumers that are not required.
If electricity storage options are available in the company, this increases flexibility in peak load management, as peaks in electricity consumption can be intercepted using previously stored energy.
However, such an electricity saving concept also has its price. The complexity of planning production processes increases significantly if, in addition to machine utilization and throughput, the fill level of the power storage units or the switching on and off of the machines must also be taken into account. The latter can also lead to new load peaks. Manual planning methods using spreadsheet programs quickly reach their limits here.
Flexible production
Since the liberalization of the electricity in Germany market, industrial companies have been able to purchase their electricity freely on electricity exchanges and benefit from price fluctuations. Electricity prices are set at a specific time on the previous day for the next 24 hours and are subject to strong fluctuations resulting from supply and demand. The time intervals vary from exchange to exchange and can be offered in the form of freely defined blocks, hourly or quarter-hourly intervals. It is interesting to note that electricity prices can also develop negatively in the event of an oversupply, whereby consuming companies receive money for relieving the burden on the electricity grid.
This fact can be exploited in production planning by shifting very energy-intensive production to times when electricity is particularly cheap. Companies can achieve an even higher degree of flexibility by using energy storage systems. These can be charged with cheaply purchased electricity, which can then be used in production at a later time. It is particularly advantageous if the company can draw on self-produced electricity. In an episode of our German-language podcast “OPTCast”, we talked about a research project at the University of Paderborn in which this principle is used to operate an induction furnace for the production of sheet metal for the automotive industry.
Similar to peak load management, there are also disadvantages to this method. Not only does the planning of production processes become considerably more complicated, there are also organizational limits. Delivery deadlines for customer orders, for example, can make it impossible to postpone production. In addition, work shifts cannot be canceled or rescheduled at will. Rescheduling at short notice – especially when using manual planning methods – can impair planning quality and therefore efficiency. It is also necessary to precisely calculate whether and under what circumstances it is worthwhile for the company to invest in electricity storage or renewable energies.
Thermal integration
If a company uses electricity for heating or cooling within processes, the principle of heat integration can help to reduce electricity costs. Industrial heat integration, also known as process integration, aims to reduce the demand for heat and cooling from industrial plants. This is achieved by linking processes that generate heat with processes that require heat. With the use of heat exchangers, the released heat can be used efficiently where it is needed. This enables the externally supplied energy requirement to be minimized. The processes to be heated serve as heat consumers, while the processes to be cooled act as cooling consumers. A system that connects different heat exchangers to optimize heat and cold consumers is called a heat exchanger network.
This concept also leads to complicated planning when heat and cold consumers have to be taken into account in a production plan. In addition, investing in the appropriate technology requires a well-considered decision.
More interesting articles
Save electricity right from the planning stage with OPTANO
The great advantage of mathematically supported production planning lies in its ability to take a large number of targets and constraints into account in the planning process. This allows peak loads to be avoided or production to be made more flexible within certain limits. External data such as day-ahead prices or weather data can be automatically incorporated into the planning process. Even frequent rescheduling does not impair planning quality. Companies can be sure that the optimum balance between energy cost savings and productivity is found. Thanks to powerful scenario analyses, investments in electricity storage, renewable energies or heat exchangers can be calculated, evaluated and prioritized. This ensures that the system can also be adapted quickly if framework conditions change.
Various concepts are available to save energy in manufacturing companies. With mathematically supported production planning, these can be integrated comparatively easily into production processes. The investments required to optimize the system’s performance can be calculated and evaluated thanks to scenario analyses. And me? I will continue to walk from room to room and switch the lights off again. It’s well known that exercise keeps you young.
Have you already got your factsheet on this topic?
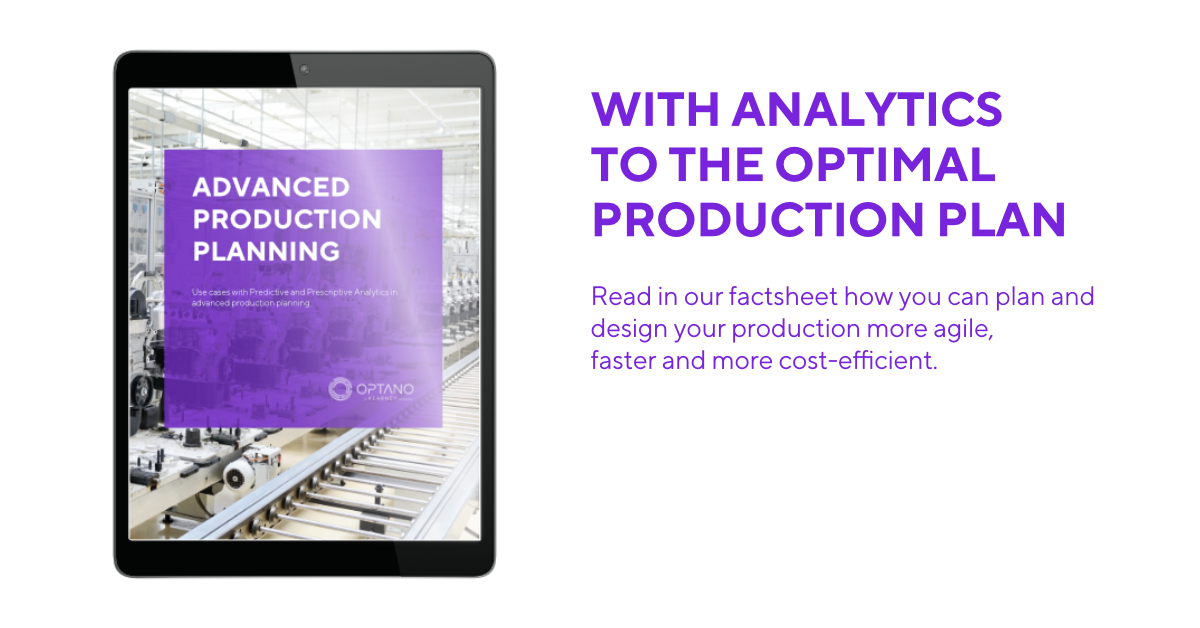
In our factsheet Advanced Production Planning we present some of the use cases of Predictive and Prescriptive Analytics in modern production planning which you can download here.
To obtain our factsheet, all you need to do is enter your contact details in the space below. A pop-up window will then open to download the whitepaper. Please note that by providing us with your email address, you agree that we may contact you on this topic. You may revoke this agreement at any time by contacting [email protected].