Strom sparen in
der Produktion
Vielleicht kennen Sie das Phänomen auch? Räume, die meine Kinder während der dunklen Jahreszeit betreten haben, erkennt man daran, dass das Licht brennt – unabhängig davon, ob sich der geneigte Nachwuchs noch im Raum aufhält oder nicht. Dies erfordert ein wachsames Auge und viel Mikromanagement meinerseits. Es gilt der Grundsatz: „Strom sparen ist Sisyphusarbeit“! Und dieser gilt umso mehr, wenn es nicht nur um ein unnötig beleuchtetes Eigenheim geht, sondern um einen energieintensiven Produktionsbetrieb. In diesem Artikel wollen wir uns einmal anschauen, wie produzierenden Unternehmen Energie einsparen können.
Stromkosten sind nach wie vor hoch
Die gute Nachricht vorweg: Dank des Wegfalls der EEG-Umlage im Juli 2022 und der Reduktion der Stromsteuer liegen die Strompreise aktuell etwa auf dem Niveau von 2020. Doch bei genauerer Betrachtung haben sich die direkten Kosten seit diesem Jahr nahezu verdoppelt. Es ist also anzunehmen, dass das Preisniveau künftig eher steigen als sinken wird. Produzierende Unternehmen sollten diese Atempause nutzen, um Konzepte umzusetzen, mit denen sich nachhaltig Energie einsparen lässt. Hierfür wollen wir einige Möglichkeiten aufzeigen.
Stromsparkonzepte
In den letzten Jahren wurden immer mehr Methoden entwickelt, mit denen Unternehmen Energie einsparen können. Viele davon sind jedoch mit hohen Investitionen verbunden. Wir wollen daher mit einer vergleichsweise einfach zu implementierenden Methode beginnen: dem Peak Load Management.
Peak Load Management
Über diese Methode haben wir bereits in einem eigenen Blogartikel berichtet (hier klicken). Trotzdem möchten wir hier noch einmal auf das Prinzip eingehen: Der Strompreis für Unternehmen setzt sich aus einem Grund- und einem Leistungspreis zusammen. Die Berechnung erfolgt durch fortlaufende Messung und Dokumentation des Stromverbrauchs in kurzen Intervallen à 15 Minuten während eines Jahres. Basierend auf dem höchsten erreichten Mittelwert wird der Leistungspreis ermittelt. In der Praxis bedeutet dies, dass bereits eine einzelne Lastspitze im Messzeitraum ausreicht, um den Leistungspreis im Abrechnungsjahr zu erhöhen. Das Prinzip des Peak Load Managements wurde eingeführt, um das Stromnetz möglichst konstant auszulasten und plötzliche Verbrauchsanstiege zu vermeiden.
Lastspitzen können auftreten, wenn mehrere Verbraucher gleichzeitig eingeschaltet werden – beispielsweise beim parallelen Hochfahren von Produktionsmaschinen. Um diese zu vermeiden, ist es notwendig, den Stromverbrauch aller Geräte im Unternehmen systematisch zu erfassen. Dies gilt auch für nicht direkt an der Produktion beteiligte Verbraucher, die viel Energie benötigen, wie Klimaanlagen. Das Prinzip des Peak Load Managements sieht vor, durch eine geschickte Verteilung der Verbräuche (z.B. durch zeitversetztes Hochfahren von Maschinen) Lastspitzen zu vermeiden – sofern dadurch die Produktionsprozesse nicht beeinträchtigt werden. Eine weitere Möglichkeit ist der sogenannte „Lastabwurf“, also das Abschalten nicht benötigter Verbraucher.
Wenn im Unternehmen Stromspeichermöglichkeiten vorhanden sind, erhöht sich die Flexibilität im Lastspitzenmanagement, da sich Verbrauchsspitzen im Stromverbrauch über zuvor gespeicherte Energie abfangen lassen.
Ein solches Stromsparkonzept hat jedoch auch seinen Preis. Die Komplexität bei der Planung der Produktionsprozesse steigt merklich, wenn neben der Maschinenauslastung und dem Durchsatz auch den Füllstand der Stromspeicher oder das Ein- und Ausschalten der Maschinen berücksichtigt werden müssen. Zudem können durch letzteres wiederum neue Lastspitzen entstehen. Manuelle Planungsmethoden mithilfe von Tabellenkalkulationsprogrammen stoßen hier schnell an ihre Grenzen.
Flexible Produktion
Seit der Liberalisierung des Strommarktes können Industrieunternehmen ihren Strom frei an Strombörsen beziehen und von Preisschwankungen profitieren. Die Strompreise werden zu einem bestimmten Zeitpunkt des Vortages für die kommenden 24 Stunden festgelegt und unterliegen starken Schwankungen, die sich aus Angebot und Nachfrage ergeben. Die Zeitintervalle variieren dabei von Börse zu Börse und können in Form von frei definierten Blöcken, Stunden- oder auch Viertelstundenintervallen angeboten werden. Interessant ist, dass sich die Strompreise bei einem Überangebot auch negativ entwickeln können, wodurch verbrauchende Unternehmen Geld dafür erhalten, dass sie das Stromnetz entlasten.
Diesen Umstand kann man sich in der Produktionsplanung zunutze machen, indem sehr energieintensive Produktionen kurzfristig in Zeiten verlegt werden, in denen Strom besonders günstig ist. Unternehmen erreichen einen noch höheren Grad an Flexibilität, wenn sie Energiespeicher einsetzen. Diese können mit günstig eingekauftem Strom geladen werden, der dann zu einem späteren Zeitpunkt in der Produktion genutzt wird. Besonders vorteilhaft ist es, wenn das Unternehmen hierbei auf selbstproduzierten Strom zurückgreifen kann. In einer Episode unseres deutschsprachigen Podcasts „OPTCast“ haben wir über ein Forschungsprojekt an der Uni Paderborn gesprochen, bei dem dieses Prinzip zum Einsatz kommt, um einen Induktionsofen für die Produktion von Blechen für die Automobilindustrie zu betreiben (hier klicken).
Ähnlich wie beim Peak Load Management gibt es auch bei dieser Methode Nachteile. Die Planung der Produktionsprozesse wird nicht nur erheblich komplizierter, es gibt zudem organisatorische Grenzen. Lieferfristen für Kundenaufträge können beispielsweise eine Verschiebung der Produktion unmöglich machen. Zudem können Arbeitsschichten nicht beliebig abgesagt oder umgeplant werden. Kurzfristige Umplanungen – insbesondere bei Verwendung manueller Planungsmethoden – können die Planungsqualität und damit die Effizienz beeinträchtigen. Außerdem muss genau berechnet werden, ob und unter welchen Umständen sich die Investition in Stromspeicher oder erneuerbare Energien für das Unternehmen lohnt.
Wärmeintegration
Wird in einem Unternehmen Strom zum Erhitzen oder Abkühlen innerhalb von Prozessen verwendet, kann das Prinzip der Wärmeintegration dazu beitragen, Stromkosten zu senken. Industrielle Wärmeintegration, auch bekannt als Prozessintegration, zielt darauf ab, die Wärme- und Kältenachfrage von Industrieanlagen zu reduzieren. Dies geschieht durch die Verknüpfung von Prozessen, die Wärme erzeugen, mit Prozessen, die Wärme benötigen. Mit dem Einsatz von Wärmetauschern kann die freigesetzte Wärme effizient dort genutzt werden, wo sie benötigt wird. Dies ermöglicht eine Minimierung des extern zugeführten Energiebedarfs. Die aufzuheizenden Prozesse dienen als Wärmeverbraucher, während die abzukühlenden Prozesse als Kälteverbraucher fungieren. Ein System, das verschiedene Wärmetauscher miteinander verbindet, um Wärme- und Kälteverbraucher zu optimieren, wird als Wärmeübertragernetzwerk bezeichnet.
Auch dieses Konzept führt zu einer verkomplizierten Planung, wenn Wärme- und Kälteverbraucher in einem Produktionsplan berücksichtigt werden müssen. Darüber hinaus erfordert die Investition in die entsprechende Technik eine wohlüberlegte Entscheidung.
Weitere interessante Beiträge
Mit OPTANO Strom bereits in der Planung sparen
Der große Vorteil einer mathematisch gestützten Produktionsplanung liegt in der Fähigkeit, eine Vielzahl von Zielen und Nebenbedingungen im Planungsprozess zu berücksichtigen. So lassen sich Lastspitzen vermeiden oder die Produktion innerhalb bestimmter Grenzen flexibilisieren. Externe Daten wie Day-Ahead-Preise oder Wetterdaten können automatisiert in die Planung einfließen. Auch häufige Umplanungen beeinträchtigen die Planungsqualität nicht. Unternehmen können sicher sein, dass das optimale Gleichgewicht zwischen Energiekosteneinsparung und Produktivität gefunden wird. Dank leistungsstarker Szenarioanalysen lassen sich Investitionen in Stromspeicher, erneuerbare Energien oder Wärmetauscher kalkulieren, bewerten und priorisieren. So ist sichergestellt, dass das System auch schnell anpassbar ist, wenn sich Rahmenbedingungen ändern.
Um Energie in produzierenden Unternehmen einzusparen, stehen verschiedene Konzepte zur Verfügung. Mit der mathematisch gestützten Produktionsplanung lassen sich diese vergleichsweise einfach in die Produktionsabläufe integrieren. Die erforderlichen Investitionen zur Leistungsoptimierung des Systems lassen sich dank Szenarioanalysen berechnen und bewerten. Und ich? Ich werde weiterhin von Raum zu Raum laufen und das Licht wieder ausschalten. Bewegung soll bekanntlich jung halten.
Kennen Sie schon unser Factsheet zum Thema?
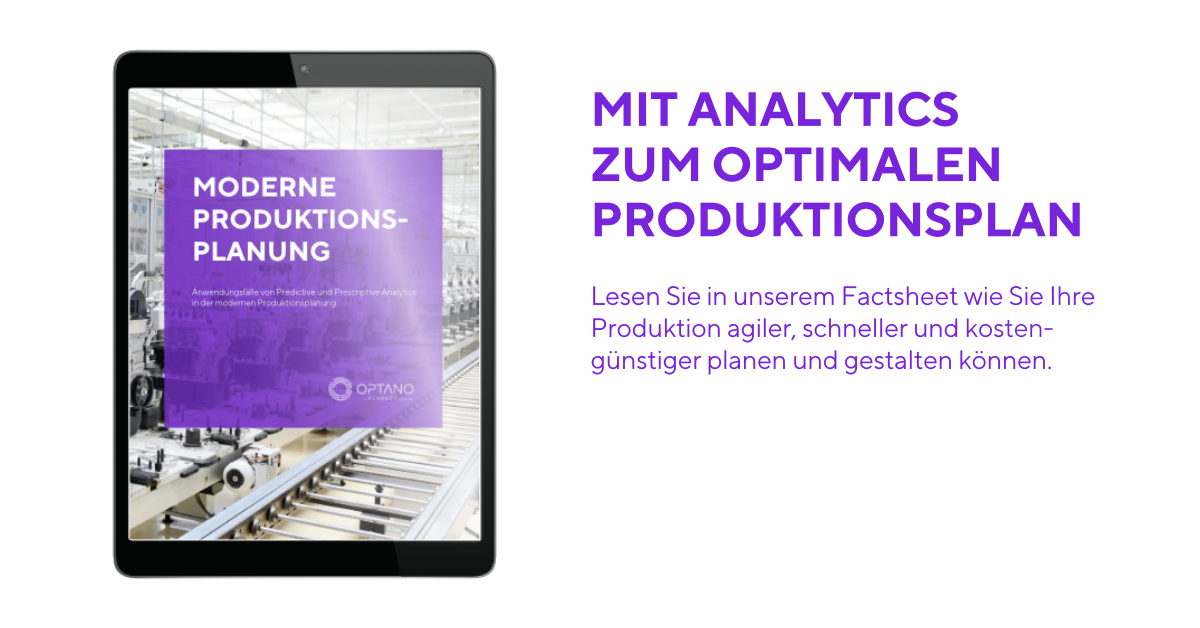
Wir haben Anwendungsfälle von Predictive und Prescriptive Analytics in der modernen Produktionsplanung in einem Factsheet zusammengestellt. Dieses können Sie hier herunterladen.
Um dieses Factsheet zu erhalten, müssen Sie nur Ihre Kontaktdaten in das untenstehende Formular eintragen. Es öffnet sich dann ein Pop-up-Fenster zum Downloaden des Whitepapers. Bitte beachten Sie, dass Sie mit der Angabe Ihrer E-Mail-Adresse zustimmen, dass wir Sie zu diesem Thema kontaktieren dürfen. Sie können diese Zustimmung jederzeit widerrufen, indem Sie sich an [email protected] wenden.