Reducing waste
in manufacturing
Who doesn’t have one in their kitchen at home – the waste separation bins for compost, paper, plastics and glass so that we can recycle as much waste as possible? In order to keep waste at a minimum, many of us try to buy products with little to no packaging. We also try to avoid excessive and (often) needless use of our electricity, gas and water. This is not just because we strive to be more environmentally conscious but also to save money in the long run, especially in the light of the energy crisis and the high electricity and gas bills.
For private households, reducing waste is a fairly manageable, small-scale process. Yet spare a thought for large companies, particularly in processing and manufacturing industries, where keeping waste at a minimum is no easy feat. In this article we take a look at the root causes of waste in manufacturing industries and how businesses can manage and ultimately keep waste at the lowest level possible – and save costs in the long run…
What exactly can be termed as waste?
Every business wants to achieve a high ROI. To this end they initiate cost-cutting measures such as reducing direct material costs, performing audits of operating costs, restructuring, cutting shipping costs, etc.
However, businesses often fail to see that savings can be made in many areas simply by making more efficient use of their resources. This is not necessarily material waste. Waste can come in many forms – it is not just what you see in your garbage can at the end of the day but it can be other forms whose causes are not immediately apparent. In manufacturing processes, waste is considered to be anything that provides no customer value and contributes nothing to your bottom line. Below are the main root causes of waste in manufacturing:
The different types of waste in manufacturing
Inefficient inventory management
Too many goods and materials lying idle in your warehouse are going to waste – a classic case of just-in-case production and overstocking. If you have goods or materials in stock that are not required in the short to medium-term, they not only take up too much valuable space but risk becoming unsaleable, particularly if these are perishables. Switching from just-in-case to just-in-time production can help, but this is not as easy as it sounds. Here, effective demand forecasting can help to determine what is required and when. Furthermore, it is necessary to have an optimal tracking system in place to trace any goods which are about to expire, which are close to expiry or are damaged. Failure to take the right measures can mean that these products or materials are deployed in production, which cannot be halted timely, thus leading to delays and therefore more waste.
Over-production
Inefficient inventory management is also a direct result of over-production. When too many goods have been produced and cannot be moved immediately, then they accumulate in the warehouse. However, over-production leads to waste in other areas. Producing goods which are not required in the immediate or short-term future means that personnel resources are being unnecessarily wasted, when they could be deployed elsewhere. Add to the equation the waste of time and energy caused by unnecessary set-up times as well as the wasteful use of machines and the energy sources they consume (electricity, gas, water, etc.). As with inventory management, an efficient process needs to be in place to forecast demand and schedule production processes better.
More interesting articles
Packaging
How often have you, as a consumer, despaired of the extreme amount of unnecessary packaging for a product that has been delivered? While the mindset here has changed over the years, still too much is being spent on packaging materials which are deemed one of the highest waste contributors of all. Although many businesses tend to view their packaging as advertising for their product, with fancy designs printed upon it, savings can be made if packaging is kept minimalistic. The fact that it should also be recyclable goes without saying, of course.
Defects and poor quality
Particularly in processing industries, it is impossible to prevent waste of some sort from occurring. All too often waste can be found in the machines after production: this can be food remains stuck in the machines, sawdust, evaporation, etc. While this may be unavoidable, too much waste may mean that the machinery is not running as efficiently as it should.
If machines are older or the technology is no longer as sophisticated, this can also lead to two other problems: they consume a high amount of energy which inevitably leads to higher overhead costs for electricity, gas or water and, even more problematic, poor machine performance can also lead to defective or poor quality goods. Therefore, additional costs are incurred for rework, corrections and scrap.
With regard to the above aspects, regular (predictive) maintenance of machines and processes is crucial.
Transport/Motion
Basically, anything that is in motion yet fails to add any value to your business or product is a waste of time, money and resources. If you have to transport materials at an excessive rate , for example by forklifter from one warehouse to another in order to make room for other materials and products, or even from one site to another by truck, you also run the risk of damage to the goods and the extra time for transportation costs money. Again, this type of waste can be reduced to a great extent, if not eliminated, with more structured processes, better production planning and inventory management, never mind an organized shop floor.
Wasted human resources
If your resources are poorly utilized they are, in effect, wasted. While this certainly applies to material resources such as machinery, raw materials, etc, it also applies to the area of personnel. If you are deploying workers on jobs who lack the necessary skills and qualifications, you are wasting both time and money. Time because employees need longer to complete the job than a skilled worker would and money because this time has to be compensated. Aside from that, the likelihood of defects or poor quality is higher when an untrained person is doing the job. This is where a production planning schedule needs to be in place which takes the skills and qualifications of its employees into consideration in order to plan processes better.
Mathematical optimization helps to reduce waste to a minimum
Planning software such as OPTANO applies mathematical optimization methods to create the necessary transparency in planning which can help you make informed decisions on the best course of action to take. With the help of sophisticated analytical methods such as Predictive and Prescriptive Analytics, production plans can be created based on a model which maps the entire production process – taking into consideration all objectives, resources, variables and constraints. Special solvers are used to help come up with the optimal solutions to the production problem.
Optimal production plans with OPTANO Production
With OPTANO production it is possible to identify the right measures in order to achieve your objectives –after sound analysis of all your available business data. In this way, alternatives can be analyzed and compared with one another in what-if scenarios in order to find the proven best solution. For example, by using the same data in multiple scenarios to analyze you can make long and short-term demand forecasts and prepare and respond quickly to unexpected disruptions by rescheduling in good time, avoiding unnecessary delays and the waste in time, money and resources that occur as a result. By analyzing your inventory management you can identify which steps to take in order to prevent surplus inventory and be confident that a smooth production workflow is in place, that you can, reduce levels of wastage and improve your plant efficiency.
Whether it is tactical or operational planning, with OPTANO production plans can be generated quickly and easily in line with your requirements.
Read our use case below to gain an impression of just how OPTANO can benefit your production:
Case story
A manufacturer that specializes in producing wrapped moldings and profiles for use in items such as furniture deployed a computer-operated sawing unit, which was designed to cut the large wooden panels it received from suppliers into the smaller components required for finished products. The company soon discovered that the software that came with the sawing unit was not advanced enough to cope with its specialist manufacturing processes, which mostly use unusually long and narrow pieces of wood, forcing staff to create manual workarounds. In their efforts to eliminate waste, employees were spending hours manually calculating the best ways to cut the wood to reduce off-cuts.
Once the saw had done its work, employees had to walk long distances to rotate the huge wooden panels or remove them from the cutting table as they worked to generate the components needed for each customer order. This was extremely time-consuming, and threatened to become a bottleneck that would increase production times and jeopardize the company’s ability to deliver products to customers on time.
OPTANO’s software solution automatically collected data on the company’s stock of raw materials, product designs, customer orders waiting to be fulfilled, operational constraints of the saw, and the availability of forklift trucks to transport the items within the manufacturing facilities. By collating and combining these factors, the solution optimized key business processes involved in the manufacture, storage and delivery of products.
The results speak for themselves:
1. A 7% reduction in the amount of wood used by minimizing unusable off-cuts reduces raw materials wastage.
2. A 98% reduction in the time spent calculating cutting patterns, enabling the company to reassign planning staff to more productive roles, although some manual adjustments to the plans are still needed
3. An increase in capacity by optimizing the transport of items within the manufacturing facilities, helping the firm avoid costly investments in extra resources despite higher output.
Waste not, want not...
An old English proverb is “waste not, want not”, meaning that if you do not waste anything, you will always have what you need at hand. This is especially true today more than ever and we should be taking care not to carelessly waste what we have. Industry is one of the most wasteful areas, yet one of the areas with the biggest potential to reduce the level of wastage it creates. It is never to late to “waste not, want not”.
Have you already got your factsheet on this topic?
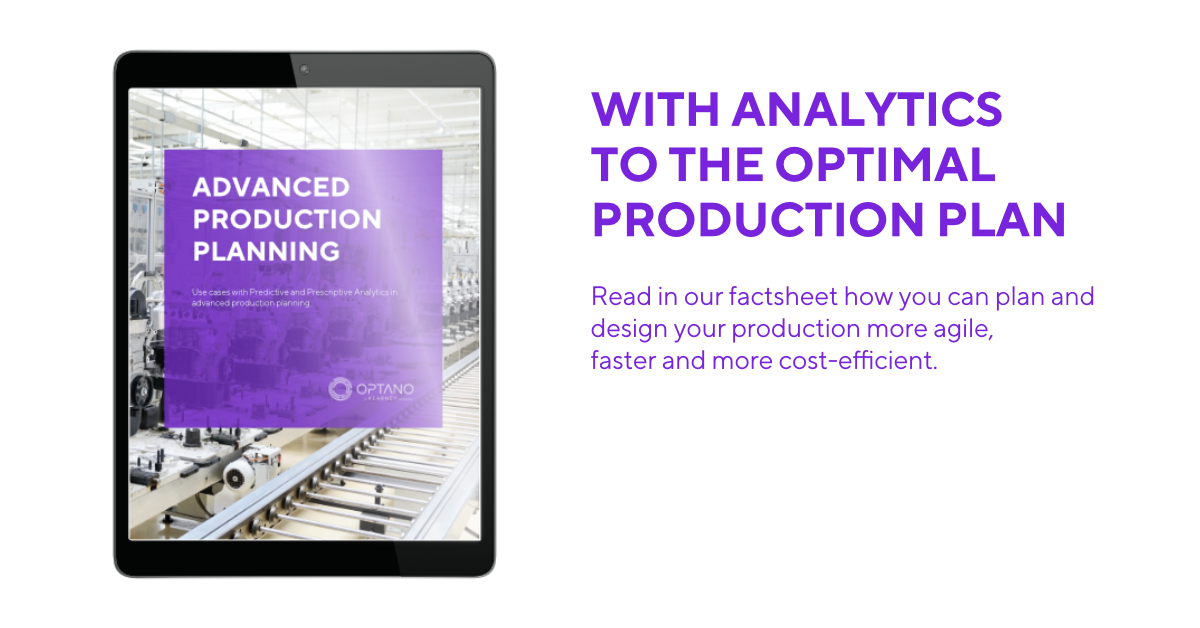
In our factsheet Advanced Production Planning we present some of the use cases of Predictive and Prescriptive Analytics in modern production planning which you can download here.
To obtain our factsheet, all you need to do is enter your contact details in the space below. A pop-up window will then open to download the whitepaper. Please note that by providing us with your email address, you agree that we may contact you on this topic. You may revoke this agreement at any time by contacting [email protected].