Optimizing costs in production networks
Part of running a household involves budgeting costs. Whether you live alone or as family, it is still necessary to know how much money comes in and, above all, how much goes out. For private budgeting the 50-30-20 rule is often recommended: 50% of your disposable income for needs, 30% for wants and 20% for savings/debt repayment. This rule of thumb can work well for families or for a single person. It is easy to maintain an overview and balance out incoming and outgoing expenses since everything is confined to one household.
Production networks with locations in different regions, countries and even continents are an entirely different matter. Just like a household, they have to coordinate the different facilities and business areas, all of which have various cost requirements, to meet their prioritized targets. For example, these can be low cost and risk, maximized profit and optimized KPIs. However, such networks are far more complex than a household and much more is needed than a 50-30-20 rule to optimize the costs within an entire production network. Without the necessary transparency and efficient management, these costs can quickly spiral out of control.
In this article we want to focus on how production networks can balance their costs on a long-term basis and meet their targets.
The catch-22 of production networks
Multiple sites within a production network are connected to each other and to customers by various transport options. Whether it is a global production network or one that is confined to a specific region only, the objective is always to achieve the optimal distribution of customer requirements across the entire network. At the same time lowest costs, short delivery times as well as a high service level, i.e delivery reliability and goods availability, must also be ensured. (Read our blog “Who supplies whom” to learn more about managing complex production networks in detail).
The difficulty here is that many of these are competing targets. For example, if you want to cut costs in one area, you run the risk of them increasing in another. For this reason, it is essential to understand how the different areas of your network interact and how decisions made in one area can impact another, not just within one production facility but among all facilities combined. However, without the right measures in place, this becomes a mammoth task.
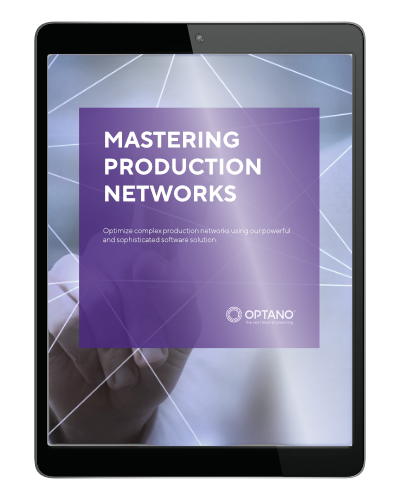
Know your cost drivers!
The four main cost factors within a production network are in procurement, production, inventory and transport. Striking the balance between all four cost factors is of the utmost importance. However, as we already mentioned above, finding the optimal trade-off is difficult. By cutting the costs of one, you are creating more problems in another, the dilemmas of which we would like to explain in more detail below:
- Procurement costs
A purchasing manager has two objectives in sight – to ensure security of supply and to purchase the raw materials and goods required as cost-effectively as possible. Due to fluctuating prices in the markets, it makes sense to stockpile the goods that are available at the optimal price. The consequence of this, however, is that it drives up your storage costs. This means weighing up all the various options. Which materials should be prioritized and bought and stored in bulk, which ones should not? How do we balance storage costs and tied-up capital with the goals of goods availability and low procurement costs?
- Production costs
Basically, the production sites within a production network cannot produce at the same costs. Depending on the country they are in, their size and capacity, costs for procurement, storage, transport, labor, machines, etc. can vary considerably. Since demand should be distributed intelligently across the network, the logical assumption would be to satisfy this demand by availing of the production facility that disposes of the necessary capacity and which can produce as cost-effectively as possible. While this may sound like the optimal solution in theory, it throws another spanner in the works because the chosen facility may not be located close to the customer. The result: your transport costs are higher. In addition, this can also be at the expense of your other goals such as delivery reliability and short delivery times. So here, too, it is essential to find the optimal trade-off between your production costs, delivery times and transport costs.
- Inventory costs
As we mentioned in the section on procurement costs, a company can get more favorable purchasing conditions by buying goods in large quantities and having them in storage. On the other hand, stockpiling ties up valuable capital, which is also skyrocketing thanks to the currently high interest rates. This capital could be invested in other areas to meet the customers’ demands on companies. Here it is important to strike the optimal inventory balance and take into account which goods you can store and deliver over a longer period of time (e.g. on a just-in-case) basis and which ones you should purchase on a just-in-time basis.
- Transport costs
The volume and type of goods, the selected mode of transport as well as the route from the supplier to the recipient all have an influence on your transport costs. A production network must have a highly efficient supply chain in place, which takes into account factors such as optimal routing, modes of transport, load capacities as well as import duties and freight insurance.
Usually, transport costs can be saved by choosing to manufacture and ship products from production facilities which are closer to the customer. Yet, this is not always feasible. While transport routes may be shorter and more cost-effective, the production costs can increase if overhead, labor or machine costs are higher at the chosen production facility. Another question to consider: Does the facility also have the manufacturing and storage capacity? Here it is important to weigh up the transport costs against production and inventory costs.
"Untangle" your network
As demonstrated above, the complexity of production networks makes it extremely difficult to balance the costs in various areas. This complexity can be compared to a tangled ball of thread which needs to be untangled before you can use it. In production networks you have a lot of processes and structures which interact and influence one another. The larger the network, the more intertwined the various processes and structures become. The result is a lack of transparency. Yet if you “untangle” all of the different processes and structures, you start to get a clearer picture of the network. And with intelligent planning, it is possible to find the optimal cost trade-off for your network.
Create transparency together
Communication among all the key players in your network is essential. They have to conduct an open and systematic analysis of the current situation and reviewing the network extensively to get a clear overview of the following: who is currently supplying whom and at what cost? Other factors to consider are delivery times and to identify where and how often the requirements for delivery reliability and goods availability are not being met.
During this procedure, a huge amount of data from each production facility and department will be collected and filtered to determine which of it is relevant and can be leveraged. Quite often, though, a network’s own IT infrastructure is not able to process and prepare this wealth of data and external tools have to be deployed, for example an analysis layer which connects all the relevant data sources via an interface.
Only after conducting such an analysis of your network is it possible to identify and understand all of the different processes and structures and gain the necessary transparency to help you pursue your goals (optimal costs, short delivery times, delivery reliability and goods availability). While this step may be arduous and time-consuming, its benefits far outweigh its drawbacks.
Uncover your network's potential!
The transparency that has been created gives you important insights into the potential that has lain hidden in your network and to understanding the trade-offs between procurement, production, inventory, transport and other costs while taking into account other factors such as delivery reliability, a high service level, proximity to customers and other KPIs. Most importantly, it can help to facilitate your planning decisions.
And this brings us to the next issue, namely: manual planning has its limits. The higher the complexity, the lower your chances are of getting an optimal plan if it has been created manually. If one of your main goals is to balance all the different costs within your network, then it is time to seriously consider deploying optimization software, such as OPTANO, if you have not done so already.
Strike the right cost balance with OPTANO
Here at OPTANO, we don’t shy from complexity, we welcome it! This is because we have incorporated a highly sophisticated tool into our software which is able to master any planning challenge – mathematical optimization.
OPTANO has a team of experts with a wealth of experience in all kinds of optimization projects. At the start of any project, the team will work closely with you to identify all of your relevant data and prepare it so that we can help you define your targets. How can procurement costs be minimized without losing out on quality? How can we get the optimal trade-off between transport and production costs, etc.?
Thanks to mathematical optimization methods which run in the background, various objectives can be taken into account during the optimization process and the optimal result can be calculated from any number of possible combinations quickly and easily. The results are grouped and clearly displayed in various graphs, charts and maps to give you an overview of the different cost factors and pinpoint where the problems and inefficiencies in your network are.
OPTANO also allows you to compare the consequences of your decisions in what-if scenarios. For example, you can calculate what the impact would be on the service level if you were to lower your inventory. How would delivery reliability be affected if you reduced transport costs or relocated production? It is also possible to realistically analyze in advance what would happen if you were to make any changes to your supply chain, for example, choosing a new supplier. And we can even go one step further: thanks to advanced analytics methods such as Prescriptive Analytics, OPTANO can provide targeted recommendations on how to implement your decision for optimal results.
Flexible cost optimization at the touch of a button
Unlike household budgeting, there is no need for standard rules like 50-30-20 when it comes to optimizing costs with OPTANO. We are aware that network conditions and parameters are subject to continuous change, and OPTANO offers you the flexibility to adapt to these changes and balance your costs as you so desire – quickly and easily at the touch of a button.
Have you got your copy of our factsheet on this topic?
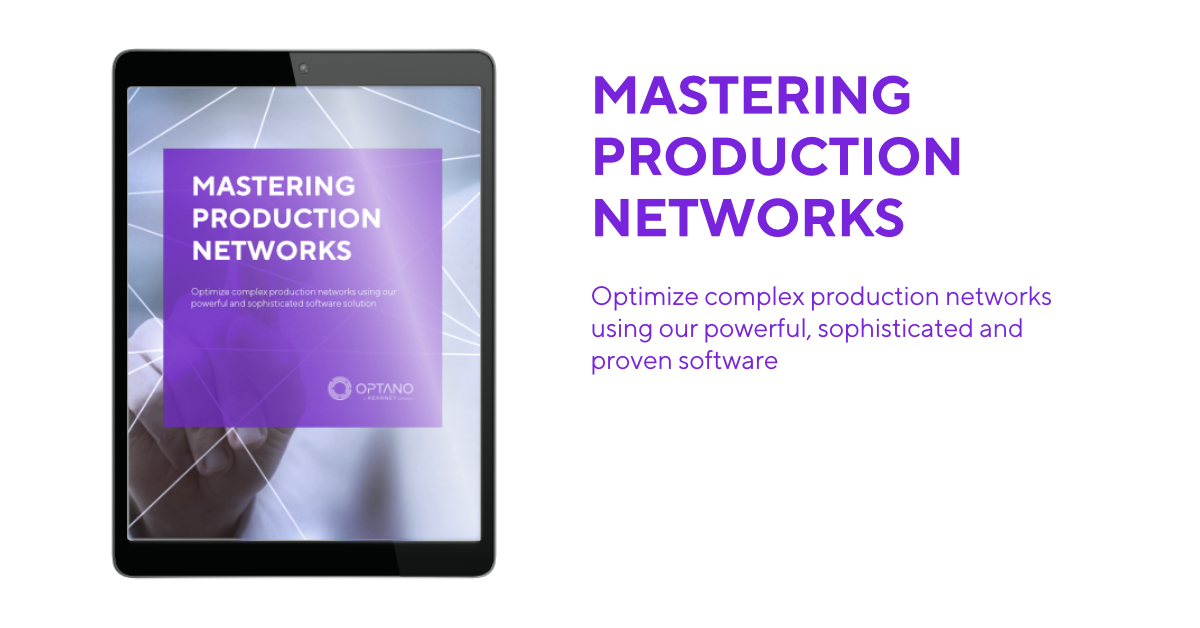
Managing complex production networks is challenging. There is often a lack of the necessary transparency to coordinate requirements and production capacities in such a way that the availability of goods and production costs are in an optimal relationship. In this factsheet, we show the possibilities offered by the OPTANO solution for production networks. In this factsheet we would like to share what we have learned over the course of numerous projects on how to successfully complete an optimization project.
To obtain our factsheet, all you need to do is enter your contact details in the space below. A pop-up window will then open to download the whitepaper. Please note that by providing us with your email address, you agree that we may contact you on this topic. You may revoke this agreement at any time by contacting [email protected].