Who supplies whom?
If game names like “SimCity” or “The Settlers” mean anything to you, you probably grew up in the 90s, like I did, and may also be a fan of building strategy games. To this day, I’m fascinated by the complex cycles of goods and the detailed control of production and demand for the sustainable economic success of my game world. In fact, the basic mechanics of the games are not that far removed from reality.
If we look at complex production networks, the planners’ task is precisely to bring goods and demand into line as effectively as possible – it’s just that the drop height is many times higher and the interrelationships are much more complex. In this article, we want to show how the complexity of production networks can be mastered in order to increase efficiency, robustness and sustainability.
High complexity means high optimization potential
The more sites are connected in a production network, the more complex it is to manage them. This is because every decision in the production plant has an impact on the production price and production time, which should be as low as possible in the interest of the customer. So the two simple questions are: who produces what and who supplies whom and how? Sounds simple? Well, it isn’t. Because the devil is in the details:
Do not lose the overview
A production network is not usually created on the drawing board – it grows. While it is relatively easy to integrate newly opened sites into the existing structure, this is much more difficult in the case of acquisitions or takeovers. Not only do they bring an existing infrastructure with them, often the key figures and IT landscape are not compatible either. It is not uncommon for customer relationships to have evolved, so that a customer is not always automatically supplied by the most favorable production site, but by the one that has always supplied him. The lack of transparency of established networks means that such an approach is generally not questioned, and if so, only very rarely.
Plan ahead
Consider heterogeneous production conditions
Not every location can manufacture every product. Certainly not in the same quality and quantity, in the same time or at the same cost. Demand and capacity must therefore be coordinated in such a way that not only is supply guaranteed, but production is also at the lowest possible cost. This is where there is great potential for savings.
Choose different transport options
Savings in production can be lost again by choosing unfavorable transport. It is therefore necessary not only to select the shortest transport distances during planning, but also to minimize the number of transports. If this is not complex enough for you, you can also include different means of transport in the schedule. The choice of airplane, ship, train or truck not only has an influence on delivery times and costs, but also on the CO2 balance to a great extent.
Plan redundancies
In a multi-product company, consideration can be given to manufacturing products at several locations to still be able to deliver in the event of production stoppages. Planning must take into account which redundancies must be kept available for which products and for which products delivery delays can be accepted. Product availability and delivery times have a direct influence on customer satisfaction – an essential factor in planning.
Choose locations wisely
Do not forget CO2
We have already briefly touched on the subject. For a long time, the carbon footprint was considered a soft factor in planning. But in the meantime, it is not only a sensitized public that is providing noticeable pressure in the direction of climate-friendly production. Legislation is also narrowing the scope for manufacturing companies.
For those who think the above challenges are not enough, the list can be extended as soon as we stop talking about national production networks and start talking about international ones. From an international viewpoint, wage differences, currency fluctuations, customs duties and, last but not least, geopolitical factors can be added.
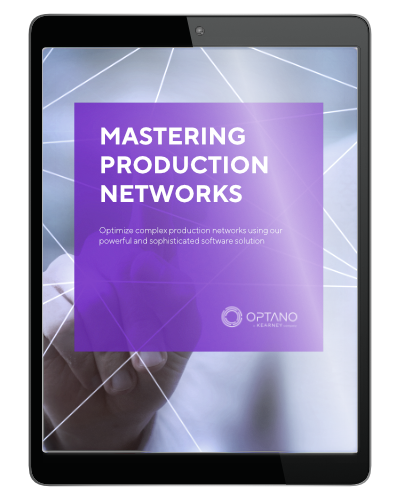
Step by step to better planning
We have seen that many factors contribute to the high degree of complexity in production networks. However, we have also promised that this complexity holds great potential for optimization. In the following, we will take a closer look at this potential and show how it can be leveraged.
Create transparency and data basis
Right from the start: You can’t do it without hard work. Processes must be identified, understood and structured. You have to learn to understand which factors influence each other and how they interact. This is not easy, especially in established structures. Success will come to those who manage to get everyone involved around the table and conduct an honest and systematic analysis of the current situation. This is one side of the coin. On the other side, the necessary data must be identified, harmonized and made usable. In our projects, we repeatedly find that even this process of gaining knowledge is enormously valuable for the companies and that initial quick wins can be achieved quickly – so the hard work is worth it.
Formulate and weight target
You already know what goals you are pursuing with your planning? Maybe it’s worth taking a second, closer look? Because in reality, they are often less clearly formulated than you thought. When defining goals, it is also important to listen to and involve all stakeholders. For example, should unit costs be reduced or should delivery reliability be increased? Or is it a question of even capacity utilization in the network? Or about more redundancy for less susceptibility to faults? Perhaps some of the goals mentioned are contradictory? No problem, if they are prioritized among each other. Which goal is the most important? How should the other goals be weighted against each other? In order to be able to quantify the achievement of objectives, it is advisable to define KPIs (key performance indicators). Also important to know: The more goals are formulated and prioritized, the less plans can be optimized manually. For the beginning, it is therefore important to keep the target definition manageable.
Create demand forecasts
Analyze data
The topic of data was already briefly addressed at the beginning of this section. In order for data to become information, it is important to bring it together and analyze it at a central point. If the existing IT infrastructure does not offer this possibility, it is advisable to introduce an analysis layer – this can be an external tool that can be connected to all relevant data sources via an interface. The previously defined KPIs help to evaluate the degree of target achievement. Graphically linking the network as a mesh of production sites (with all relevant master data and KPIs) and customers (with actual and forecast requirements) as well as transport routes (with different transport modes and costs) can help to increase the overview and make better decisions.
Optimize network
Leveraging hidden savings potential with OPTANO
In the previous section, we showed how to improve the planning of complex production networks in general. And we know: Many companies already plan their processes and structures sufficiently well – or at least believe they do. In our experience, the rule of thumb is that the savings potential through intelligent decision support increases with the complexity of the network. So when planning becomes really complex, the stage is set for mathematical optimization, as offered by OPTANO. Especially when it comes to identifying and leveraging hidden potential in planning, software like OPTANO is virtually unbeatable.
The right team at the right time
Data becomes information
So who supplies whom and in what way?
As already described in the previous section, the optimization algorithm matches the demand forecast for a specific period with the production capacities. Care is taken to ensure that each customer is supplied by the location that can produce at the lowest cost. Important premises: There must be sufficient production capacity and transportation costs must not eat up the efficiency gain. On the contrary, the number of trips and kilometers driven should be minimized. In contrast to manual planning, any number of additional constraints can be taken into account. For example, if an upper limit has been defined for the delivery time, the system can suggest that the customer be supplied from two locations. If the carbon footprint is to be reduced, the number of transports can be minimized by bundling deliveries. Perhaps intermediate warehouses are the solution if the upper limit of delivery time is to be maintained? The possible combinations are – as already mentioned – almost unlimited. The system is so flexible that constraints can be added or removed at will. No matter how the parameters change, our customers can be confident that OPTANO will provide them with a proposal for the best possible plan with regard to their goals.
With the help of intelligent, mathematically supported planning, complexity becomes a real competitive advantage. By systematically identifying optimization potential in planning, efficiency increases can be implemented reliably and the system as a whole becomes more stable and even sustainable. An effect that cannot be achieved with classic, manual planning. Speaking of manual planning: Maybe it’s time for another round of “SimCity”?
Have you already got your factsheet on this topic?
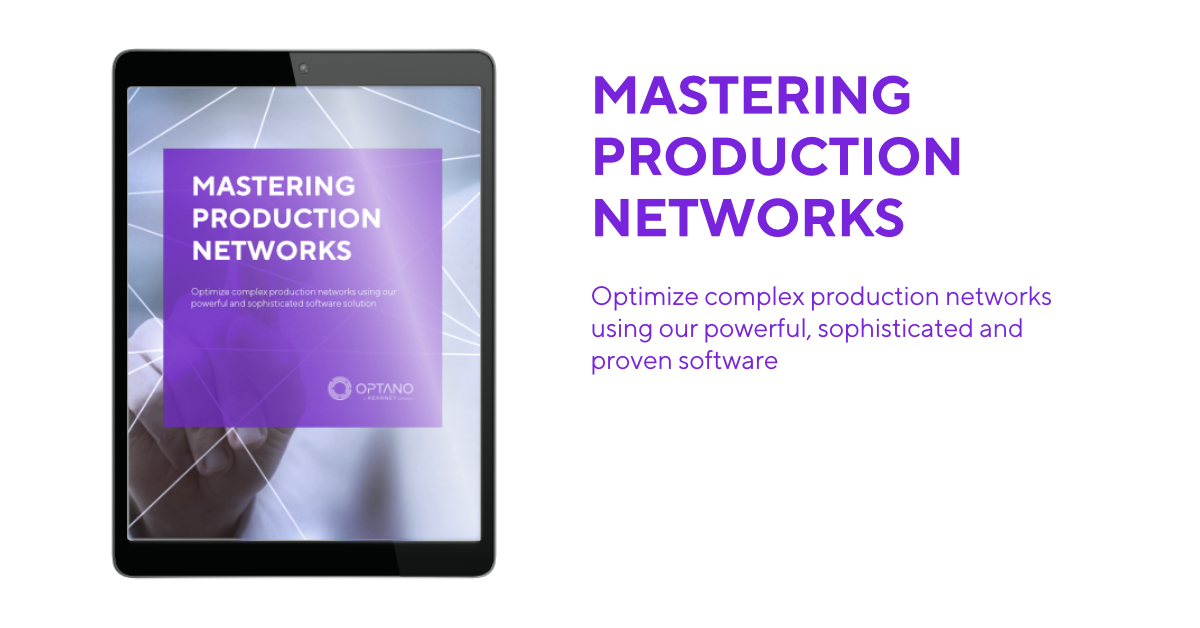
Managing complex production networks is challenging. There is often a lack of the necessary transparency to coordinate requirements and production capacities in such a way that the availability of goods and production costs are in an optimal relationship. In this factsheet, we show the possibilities offered by the OPTANO solution for production networks. In this factsheet we would like to share what we have learned over the course of numerous projects on how to successfully complete an optimization project.
To obtain our factsheet, all you need to do is enter your contact details in the space below. A pop-up window will then open to download the whitepaper. Please note that by providing us with your email address, you agree that we may contact you on this topic. You may revoke this agreement at any time by contacting [email protected].