Customized
production planning
in small batches
“Any customer can have a car painted any color that he wants, so long as it is black!” Henry Ford, the famous pioneer of modern assembly line production, is purported to have said. Yet what worked back then would inevitably be doomed to failure now due to the demands of today’s customers. The trend these days is customization, i.e. individualization. What serves as an expression of personality for customers is often a challenge for production planning. In this article we look at how to manufacture cost-effectively despite having small batch sizes.
The problem with low production volumes
Until recently the motto was: the larger the batch to be produced, the lower the unit costs will be. This phenomenon is known as the economies of scale. Conversely, this means that the unit costs will increase when manufacturers reduce their batch sizes. This is often attributed to the high installation and start-up costs in production which incur irrespective of the batch size to be produced; it makes no difference whether the product has already been produced before. These mainly consist of the following:
Production planning
The jobs must be ordered and allocated to the right machines. For multi-stage processes it is important to prevent bottlenecks from occurring which may then hold up the entire production.
Resource availability
Raw materials and intermediary products must be available as well as employees for the set-up process and
production. The first group in particular is often the cause of a bottleneck.
Machine installation
The machine has to be set-up and ready for production.
Test runs and readjustments
To guarantee a smooth production workflow, test runs have to be performed and settings have to be readjusted repeatedly.
In an attempt to solve the problem, batch sizes are increased, no matter what the actual demand is. And this does
actually manage to lower the unit costs – but only mathematically. Because in doing so, you create a whole bunch of other problems, such as:
Longer lead times
Orders which only fill the warehouse to a large extent block capacity. Possible follow-up orders may become
delayed as a result which can jeopardize delivery reliability.
High storage costs
Storing semi-finished and finished goods calls for larger storage capacity which needs to be managed and insured.
More fixed capital
Storing semi-finished and fnished goods ties up capital as resources have been invested in them which cannot be capitalized upon immediately.
Risks caused by unsaleable inventory
If products are kept in stock there is always the risk that they cannot be sold in the end. The problem is further
exacerbated if the products are perishable. Write-offs are imminent.
The afore-mentioned disadvantages mean that a non-market-driven increase in production volumes is not an adequate solution to the problem. But what can be done instead?
Proactive planning for more cost efficiency
When it comes to production with small batch sizes then the production planners and their expertise are called for more than ever. Planning has to be designed in such a way that set-up times are minimized and orders are grouped in-telligently to achieve the greatest possible economies of scale in spite of small batch sizes. The more data that is available here, the better. Let us take a closer look at three aspects:
Planning with minimum set-up times
Set-up times are the strongest driver of increased costs with low batch sizes. Therefore, it is important to try to avoid frequent interruptions when setting up machines and ensuring that the set-up times themselves are as short as possible. A very good example in this context are car manufacturers’ coating and lacquering lines. If a batch of cars needs to be coated with a light color after using a dark one, the spray nozzles need to be cleaned particularly thoroughly and so the set-up times are correspondingly higher. For this reason, an optimal coating and lacquering sequence is observed in planning – alongside all other parameters – to reduce the set-up times.
Grouping or splitting the same type of order
A further option is to group different orders intelligently. In this case, orders with the same specification are collected and grouped together to obtain a profitable batch size in total. However, this can lead to longer delivery times which not all customers are willing to accept. Athough this problem can be solved by performing part-deliveries, it has a negative effect on transport costs. Planners have to focus on the right trade-off here. This method is often applied by online printers who group similar orders from different contractors and distribute them in their network.
More interesting articles
Generating demand forecasts
As long as sufficient, reliable historical data is available, demand forecasting can contribute towards lowering unit costs. If you predict a higher demand for a product during a certain time period, the batch sizes will increase accordingly in addition to the directly ordered volume. This would result in higher inventory, but with a sufficiently large probability. This would only be temporary. An example here could be manufacturers of construction materials who also supply their end customer products via DIY markets. Here there are obvious seasonal peaks which can be considered in production planning.
The methods shown above can reduce unit costs on a sustainable basis, even for small batch sizes. However, the effort involved in the planning is extremely high. Furthermore, plans are also prone to change at short notice due to machine failure or when urgent orders come in. In addition, you can only consider a very small number of the parameters and cross-dependencies in planning as this would be too complex otherwise. What, then, would be the advantages of a mathematically optimized production plan using OPTANO based on the three examples above?
Managing complexity in planning thanks to mathematical optimization
Complexity is the enemy of any plan. However, by greatly reducing the complexity involved, plans lose their quality and thus remove themselves even further from a potential optimum. Mathematical optimization is predestined to address complex relationships and find optimal solutions. Here, the underlying processes are first analyzed in order to identify
influencing factors, cause-effect relationships and cross-dependencies. On this basis a mathematical model can be
created which maps the process. With the help of sophisticated algorithms, millions and millions of possibilities can be calculated based on real data in order to find the optimal production plan with regard to a defined objective (here:
lowering unit costs). Even better – the optimization can be geared towards several objectives such as lowering unit
costs and finding the shortest possible delivery times.
A production plan that has been created with OPTANO would therefore find the best production job sequence which minimizes set-up and lead times simultaneously, adheres to delivery dates and enables machines to run at full capacity.
If there are any changes that need to be made at short notice, these can be made with just a few clicks without the planning quality suffering as a result. Thanks to powerful procedures in the background such as Prescriptive Analytics,
planners receive clear recommendations on how to implement the previously defined objectives in practice – whether this is machine occupancy or grouping orders.
Planning can be extended by powerful predictive models such as demand forecasts based on Predictive Analytics. With the help of machine learning procedures relationships are identified and taken into account which would have gone undetected in manual planning. External sources can also be included with the historical data. If a connection can be established between the development of specific raw materials prices and the demand for a product, then this factor in real-time could be included in the predictive model. The demand forecast that has been created is integrated into the
optimized production plan and can ensure that production volumes can be increased temporarily in order to meet the forecast higher demand within the forecast period. This increases machine utilization and has an effect on the market at the same time. With mathematical optimization the customers’ desire for individuality and the company’s profitability can be combined easily.
A multi-colored new world
Who knows whether the first Model-T buyers classed the color of the car as an important buying criterium. Most likely they would shake their head in disbelief at the manifold configuration options of the modern-day automobile. And while we have grown used to individually configured cars, this is a comparably new phenomenon in the textile industry, for instance. The trend towards the individualization of products is indisputable and probably irrevocable. But with the right tools at hand, production planners can manage this well – and perhaps even gain a comeptitive market edge. What would Henry Ford say to that?
Have you already got your factsheet on this topic?
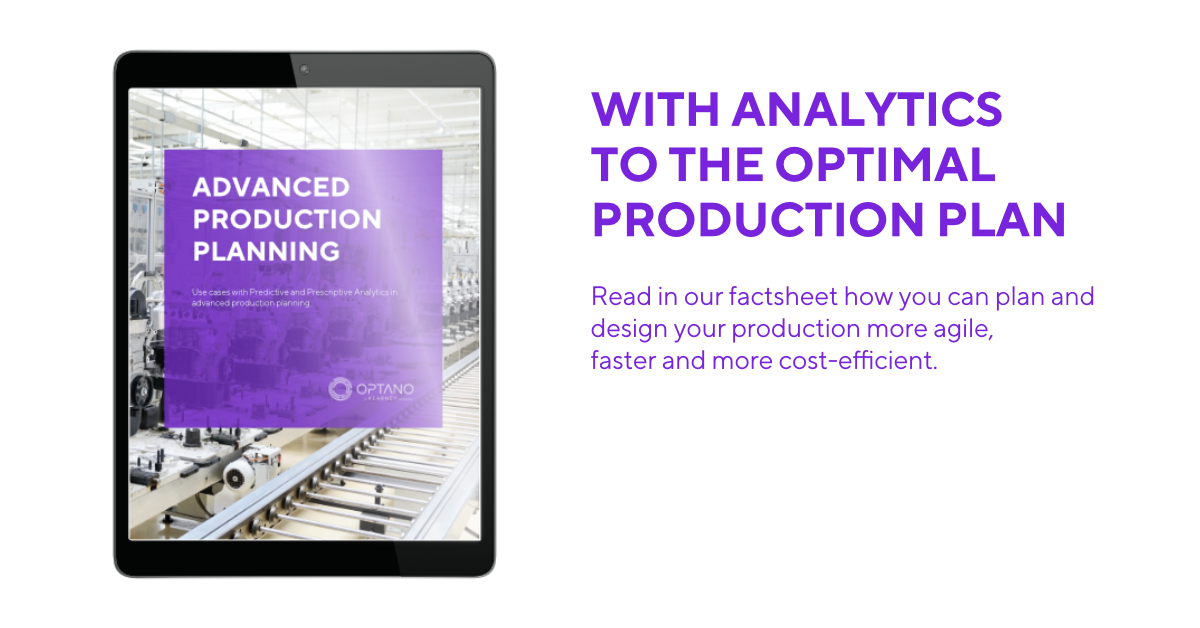
In our factsheet Advanced Production Planning we present some of the use cases of Predictive and Prescriptive Analytics in modern production planning which you can download here.
To obtain our factsheet, all you need to do is enter your contact details in the space below. A pop-up window will then open to download the whitepaper. Please note that by providing us with your email address, you agree that we may contact you on this topic. You may revoke this agreement at any time by contacting [email protected].