Optimal batch sizes -
Would you like a little more?
We as OPTANO have been in the preparations for OR23 (the annual conference of the Society for Operations Research, in Hamburg) for some time. We will be there as a sponsor with a booth – so feel free to drop by. Of course, there is a lot to prepare for such a conference: flyers, rollups and possibly one or the other OPTANO polo shirt for the booth crew.
In the course of such preparations, we are often faced with a dilemma that is a common one in the manufacturing industry: finding the right batch size. Printing flyers is a good example of this. Producing 1,000 flyers is only 10% more expensive compared to 500 flyers. But do we really need them? Or is there a big risk that we will eventually have to dispose of them? Who hasn’t found boxes full of flyers and brochures during a move with the company, which were cheap in the large quantity, but were not actually needed?
Compared to the problem of batch sizes in the manufacturing industry, this is of course only a small problem. But if the decision is already difficult for such trivial projects with little impact, how do you make it when large amounts and investments are at stake? This is the question we explore in this blog article.
Finding the best batch size
It can't be that difficult...
The problem of the optimal batch size arises primarily from the fact that two competing goals clash: low setup costs and low storage costs. Choosing small lot sizes does result in low storage costs, as only a small quantity needs to be stored at any one time. But at the same time this increases setup costs, as more frequent changeovers between products are required. Conversely, the choice of large batch sizes leads to low setup costs, but this results in higher storage costs.
First starting point - the lot size model according to Andler
A first starting point for solving this dilemma is the lot size model according to Andler. Here, the setup costs and the storage costs are entered as a function and the optimum lot size – i.e. the lowest total costs – lies at their intersection. This already gives a first impression of the cost range and the potential savings that would be possible compared to the current batch size.
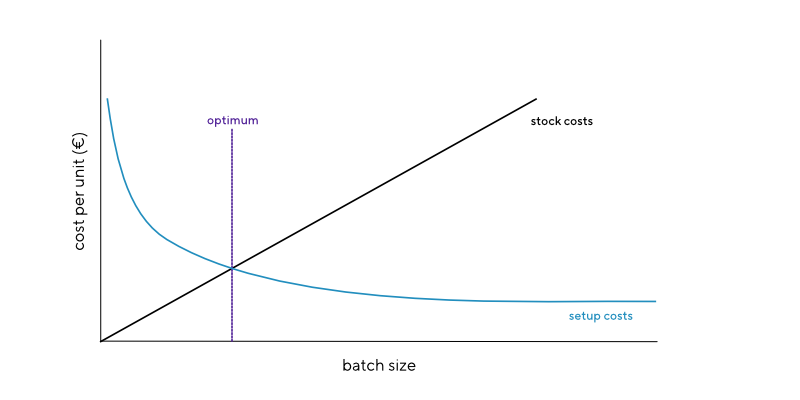
Unfortunately, it is not that simple.
But this approach is unfortunately a very theoretical one, because in practice there are many more influencing factors that have to be taken into account when choosing the batch size. For example, there may be costs for external transportation or storage services that are not integrated into the original cost function. In industries with goods that have a best-before date, the risk that they cannot be sold off in time and have to be disposed of must be taken into account. All relevant data must therefore be recorded. This includes setup times, labor and process costs, and disposal rates and costs, if applicable. There are many more requirements and they vary depending on the industry and the company.
In addition, restrictions must be defined, which often result from operational specifications. For example, minimum or maximum batch sizes may result depending on container sizes. These cannot be undercut or exceeded, even if this would bring advantages. Some of these restrictions are not obvious at first glance.
Our experience has shown that the compilation of these data and restrictions should be done in an interdisciplinary way so that no relevant data are overlooked. This is where the specific experience of the employees comes into play. Many restrictions and guidelines are lived and observed, but have never been formally recorded. Finding them is one of the most important tasks when using mathematical optimization in operations.
The result is an overall construct of facts, requirements and restrictions that can no longer be compared with a simple function. A mathematical model can combine this and by means of optimization the best batch size can be calculated. Changes to data or restrictions can be subsequently integrated and also solved optimally. Thus, with the help of mathematical optimization, not only a one-time solution is created, but also the possibility to incorporate changes flexibly and promptly.
More interesting articles
With OPTANO to the optimal batch size
Optimization software like OPTANO allows you to manage mathematical models clearly and achieve optimal results. They solve the problems with complex mathematical solution methods in the background, while the user works with user-friendly software that is clearly and intuitively designed.
In addition, batch sizing optimization can be part of a larger whole, for example embedded in production or supply chain planning. In this way, even more complex interrelationships can be taken into account and greater savings potential can be exploited.
You can also venture a look into the future with OPTANO: possible alternatives can be calculated and compared in various scenarios. For example, this allows you to answer questions about what would change if the warehouse were to be expanded or what effects would result from the acquisition of an additional machine. In this way, you can make your decisions based on real data and even receive a concrete recommendation for action.
OPTANO can also be used for forecasts of decreasing, increasing or seasonal product demand, which are determined using machine learning based on historical data. In this way, deviations between the sales forecast and the actual sales can be significantly reduced. (Detailed information on this topic can be found in this blog article)
Have we made you curious? If you would like more information about OPTANO or have any questions, please do not hesitate to contact us. We are looking forward to your inquiry!
What about our flyers?
Unfortunately, the problem of our flyer count for OR23 was not complex enough for optimization with OPTANO. (If you want to learn more about the complexity of problems, you can read our article on this topic: What makes a problem complex?). Whether we had enough flyers? Find out live on site. We are looking forward to your visit!
Have you got your copy of our factsheet on this topic?
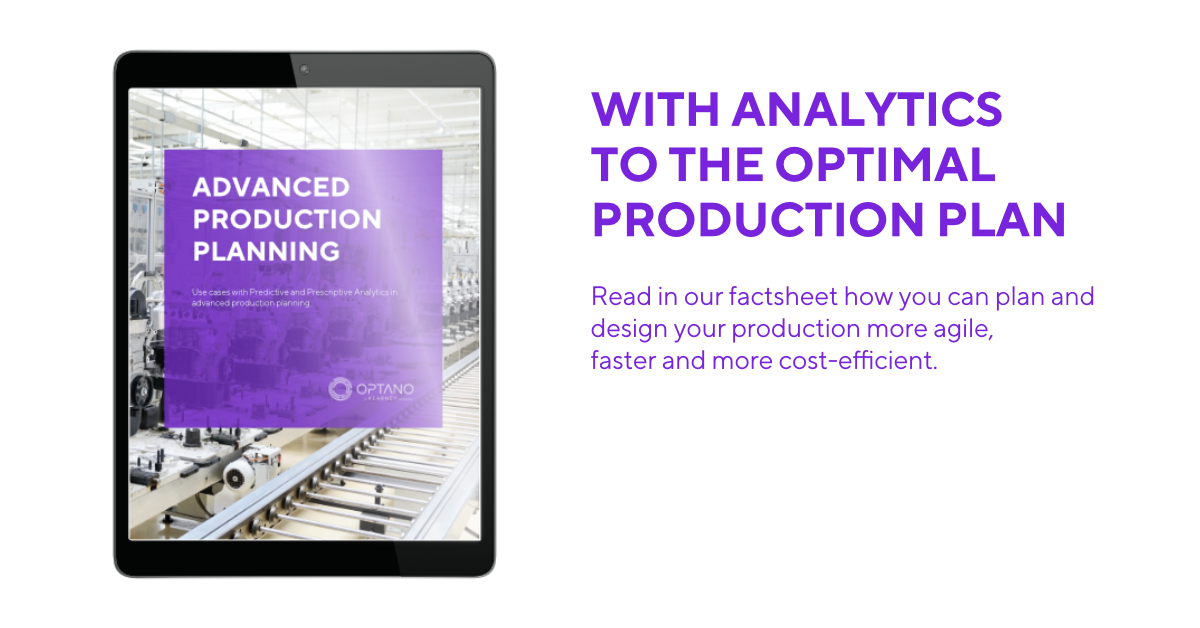
In our factsheet Advanced Production Planning we present some of the use cases of Predictive and Prescriptive Analytics in modern production planning which you can download here.
To obtain our factsheet, all you need to do is enter your contact details in the space below. A pop-up window will then open to download the whitepaper. Please note that by providing us with your email address, you agree that we may contact you on this topic. You may revoke this agreement at any time by contacting [email protected].