Operational
harmony
In an increasingly uncertain business world with geopolitical unrest, economic uncertainties and endangered supply chains, CPG (Consumer Packaged Goods) companies are comparatively well positioned and can guarantee high delivery reliability. However, this form of resilience comes at a price: very high operating costs caused by high inventory levels and rigid production cycles. In collaboration with Kearney, OPTANO has succeeded in combining this resilience with delivery reliability and cost efficiency, giving companies a clear competitive advantage. Our colleague Dario Hashemi, who we are interviewing today, played a key role in the development of the OptiCycle solution.
In the introduction, we read that OptiCycle combines the factors of resilience, delivery reliability and cost efficiency. Why is this so special?
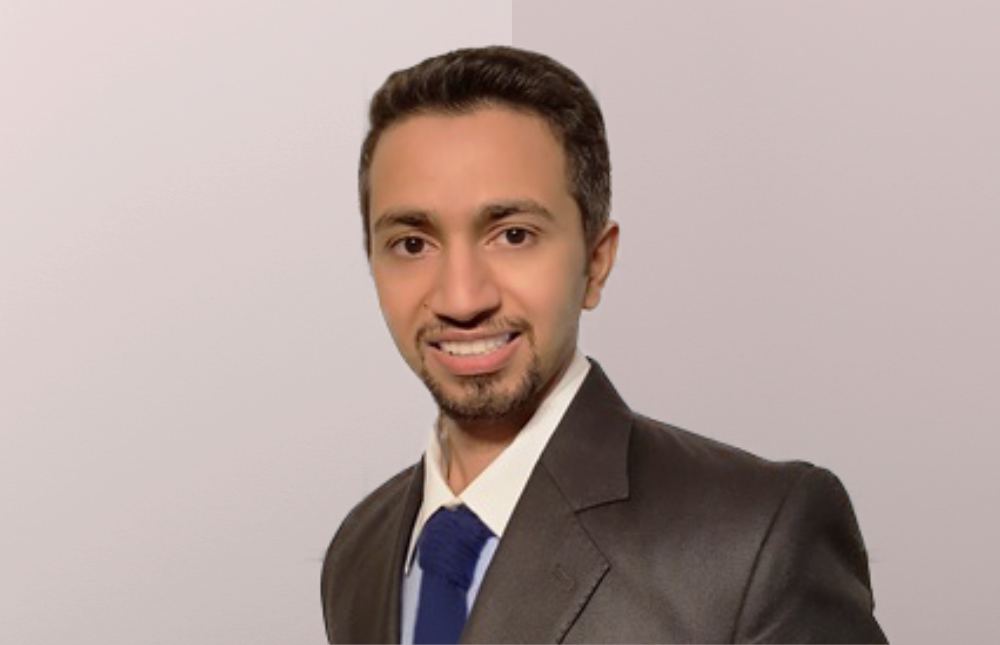
In practice, these properties are diametrically opposed in some cases. Cost efficiency in production is achieved through long production cycles and the associated minimization of set-up processes, whereby resources and machines are optimally utilized. High stock levels are required in order to meet deadlines and maintain an overall resilient supply chain despite fluctuations in demand. In addition to the resulting increase in warehousing costs, there are other disadvantages, such as the risk of rejects due to limited product shelf life (obsolescence costs).
Cost efficiency in warehouse logistics is achieved through low stock levels. In this case, short production cycles enable the targeted adherence to delivery dates and an overall resilient supply chain. This inevitably leads to a higher number of changeover processes, which reduces the utilization of machines and materials and thus leads to significantly higher production costs. OptiCycle resolves this contradiction.
How does OptiCycle succeed in resolving this contradiction?
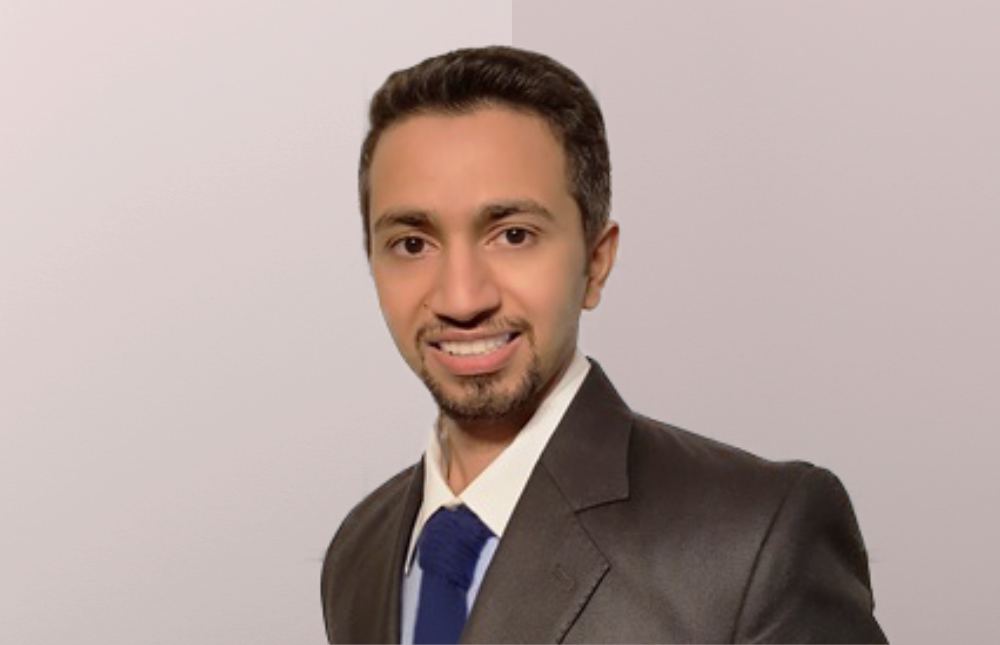
OptiCycle takes a holistic approach to production planning. Many different factors are taken into account, such as the predicted demand distribution (Gaussian distribution function), but also the costs associated with meeting that demand, in our case changeover costs, inventory costs (safety stock and cycle stock costs), and obsolescence costs.
The goal is to minimize all three costs together (changeover, inventory, and obsolescence) without compromising the service level. We achieve this by calculating an optimal production sequence that finds the ideal compromise between these conflicting objectives.
A number of constraints must be taken into account, such as balancing the operating time of each production line for efficient staffing and shift scheduling. The grouping of products with common components and production steps into production batches is also a lever for optimization and must be taken into account.
Taking into account a large number of binary decisions with various influencing factors, constraints and cross dependencies generally requires a high computational effort. However, OptiCycle has a customized and powerful heuristic that finds the optimum in just a few minutes.
OptiCycle minimizes production, storage and obsolescence costs at the same time.
For all those interested in technology: What happens “under the hood” of OptiCyle?
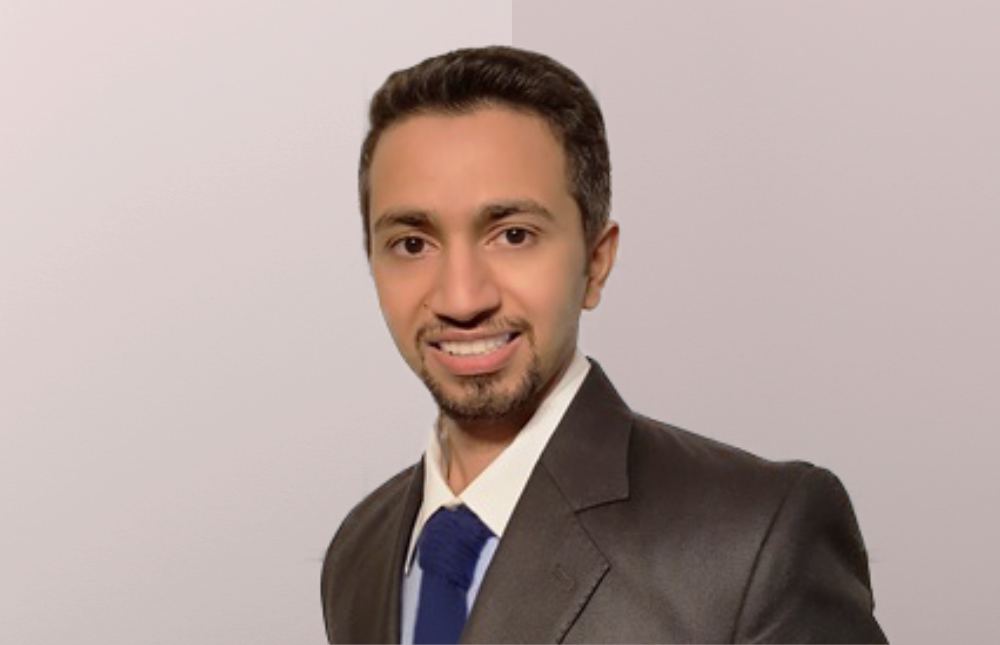
The core of the system is based on PALNS (Parallel Adaptive Large Neighborhood Search). The operators used (destroy and repair heuristics) allow the direct implementation of context-relevant problem specifics, such as the revision of weeks with high operating time, the revision of products with high setup time or the revision of the product group with small batch size, just to name a few.
We have made sure that the restrictions or cost components can be expanded at any time – the system can therefore grow with changing requirements. But it not only grows, it learns too: efficient operators are identified during optimization and used more frequently. And last but not least: by combining this with simulated annealing, we have succeeded in achieving the best possible trade-off between exploration (i.e. freedom in the solution space) and exploitation (i.e. improvement of the local solution).
As a result, we see a system that can be applied to even the largest real-world problems with extremely high performance and delivers the best possible result in the shortest possible time.
OptiCycle is the result of collaboration between an interdisciplinary team of Kearney and OPTANO employees. How does such a collaboration work?
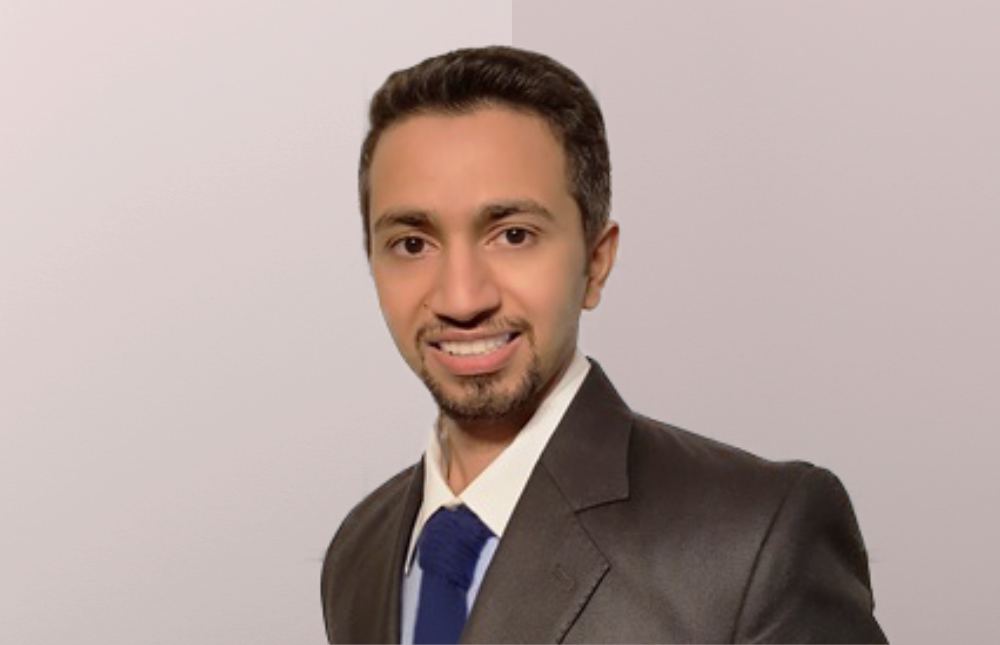
OptiCycle is a good example of how the individual Kearney companies complement each other to form synergies: Kearney’s market and consulting expertise meets Cervello’s data capabilities and combines both with OPTANO’s optimization experience. Together with the colleagues from Kearney, the requirements for the software and the framework conditions were specified, while Cervello provided support with data preparation and the development of the ETL processes. Thanks to the powerful OPTANO platform, we were able to spend most of the time developing the heuristics and release the first version of OptiCycle just two weeks after receiving the final requirements. All in all, it was an extremely successful development that also impressed our customers.
More interesting articles
In your opinion, what were the biggest challenges during development?
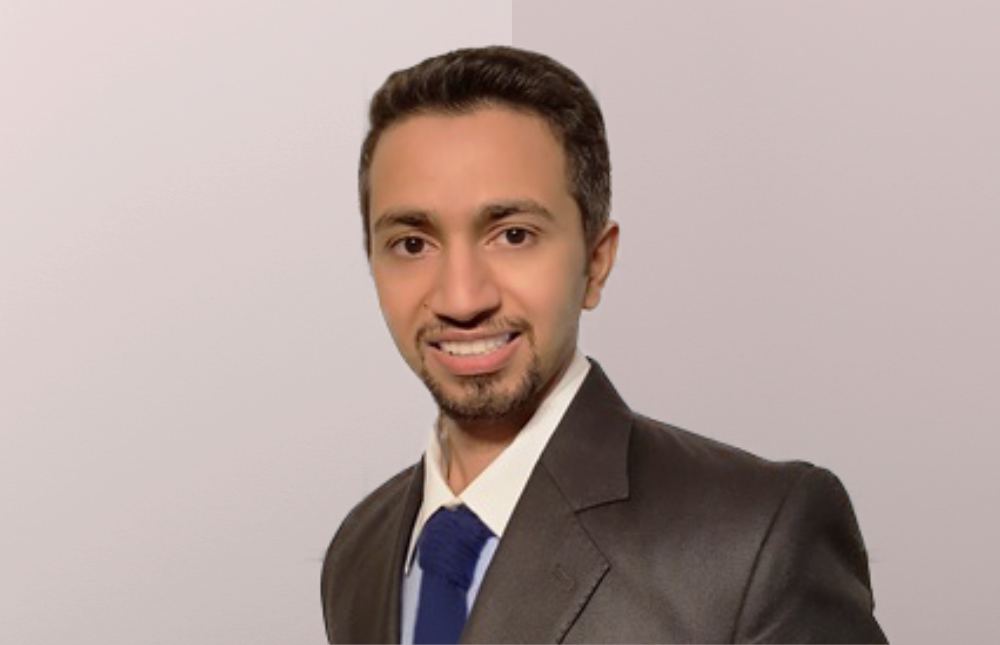
It may sound trivial at first glance, but finding the right level of abstraction is often one of the biggest challenges in such projects. You have to try to get as close to reality as possible without going into too much detail. The calculation here is simple: a level of detail that is too low does not adequately reflect reality and, in the worst case, the optimization result is unusable. On the other hand, too much detail leads to over-complexity, which inflates the model and significantly increases the computing time so that the optimization can not be used in real life.
Finding the right balance therefore requires a great deal of experience, which in turn is one of the great strengths of our interdisciplinary team.
What are you particularly proud of as a team in the development of OptiCycle?
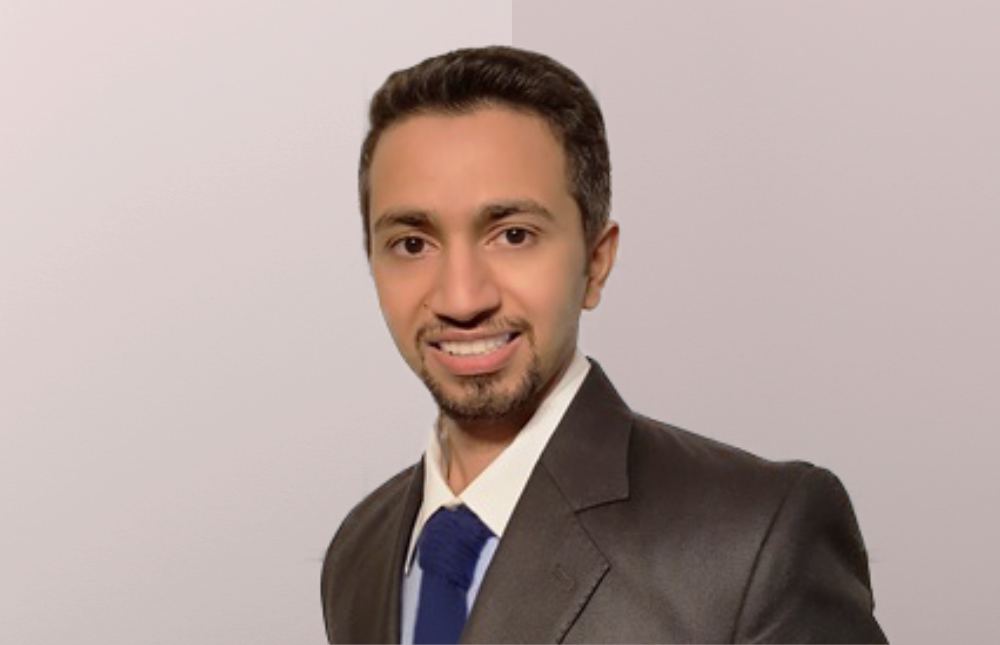
I can only speak for myself, but for me the highlight was clearly the team. A great team spirit, driven by the goal of creating a great tool together. But during such an intensive time, the tool itself naturally grows on you a little. So it was nice for me to see how OptiCycle “thinks” and learns.
One example: as the production lines often run around the clock in three shifts, there is no real start of the week and no weekend. The tool has then created plans in which production is sometimes carried out across weeks, where previously it was only planned in weekly cycles. This resulted in significant savings in changeover costs. We did not explicitly include this information in the optimizer; it found it out for itself.
Thank you very much, Dario, for taking the time to talk to us.
Do you already know our factsheet on the topic?
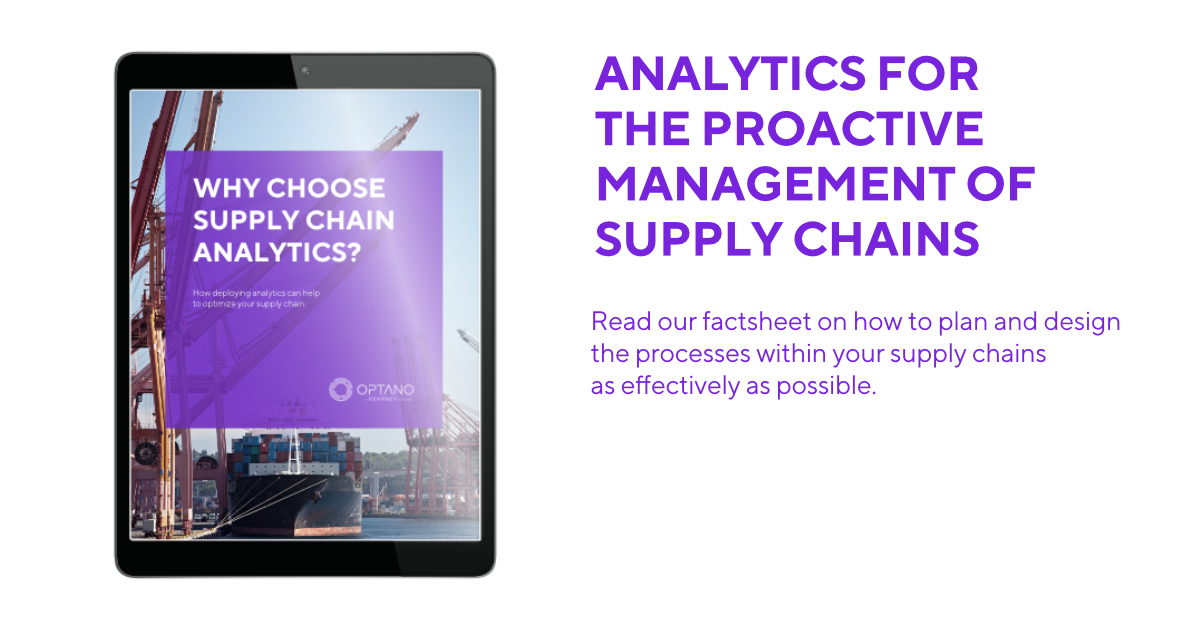
In our factsheet “Why choose supply chain analytics?” we describe the different types of supply chain analytics. You will discover how supply chain analytics works and how it can help to optimize your company’s supply chain.
To obtain our factsheet, all you need to do is enter your contact details in the space below. A pop-up window will then open to download the whitepaper. Please note that by providing us with your email address, you agree that we may contact you on this topic. You may revoke this agreement at any time by contacting [email protected].
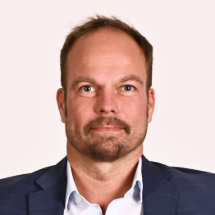