Shaping the future of the digital factory together
In our blog Boosting the digital factory we focused on the importance of the digital factory to advance production processes. We also looked at how our cooperation partner, MORYX Industry, deploys its innovative software solution to bridge the gap between manual and digital manufacturing.
In this interview, we talk to Lutz Steinleger, Director at MORYX Industry powered by Phoenix Contact, about the idea behind the MORYX solution, how it works – and the role OPTANO plays in helping to shape the future of the digital factory.
In view of the major changes and trends over the past 5 years, what challenges are manufacturing companies currently facing ?
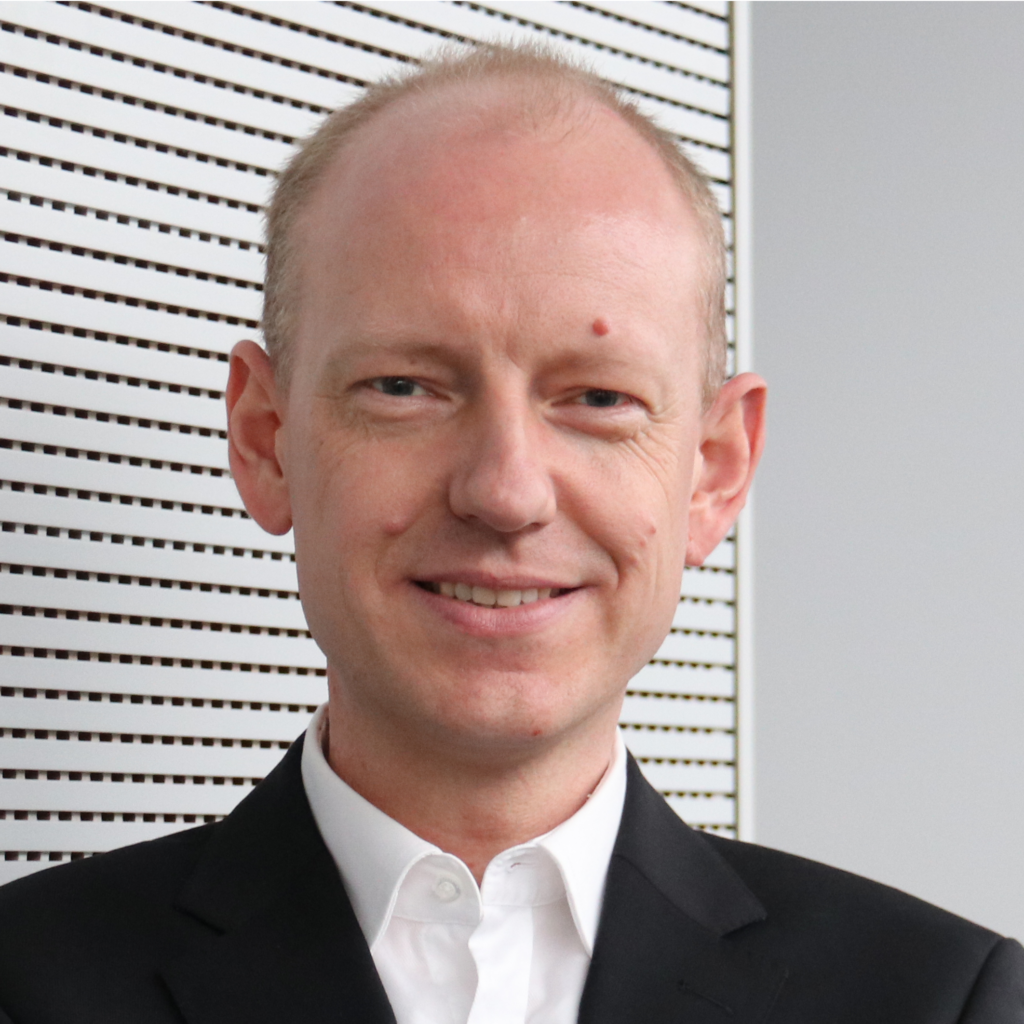
There are many different challenges. Especially in Europe, companies want market proximity. This is why they try to manufacture on the continent in order to have shorter transit routes. At the same time, however, they have to manage their labor, transport and energy costs. This aspect is particularly relevant to large corporations which have facilities worldwide.
Smaller companies have other concerns. Most of them are regionally based anyway. The rise in energy prices is their biggest worry right now. Every single machine in a factory consumes a high amount of energy. All the same, companies still have to ensure that profits rise, but wages are also increasing as well….
But, the one aspect that all companies have in common is their need to supply customers on time and be able to say exactly when they can deliver. Companies need transparency to know exactly how far along a product is in production and what is going on in the production hall. It doesn’t matter how big or small your company is. The only difference is that the more factories and machines a company has, the higher the complexity will be.
The final aspect is the legal requirements. As of 2024, a company must provide evidence of where a part has come from and how much energy has been consumed to manufacture it. So it is not just a question of optimizing your own company; you have to overcome the legislative hurdles as well. To remain competitive in the market, a company has to extract and store specific data. This works best with digital production methods, and this is where MORYX comes in.
MORYX closes the gap between IT and OT
Can you tell us more about MORYX? Where did the idea for MORYX come from and what was the path from the initial idea to the current product?
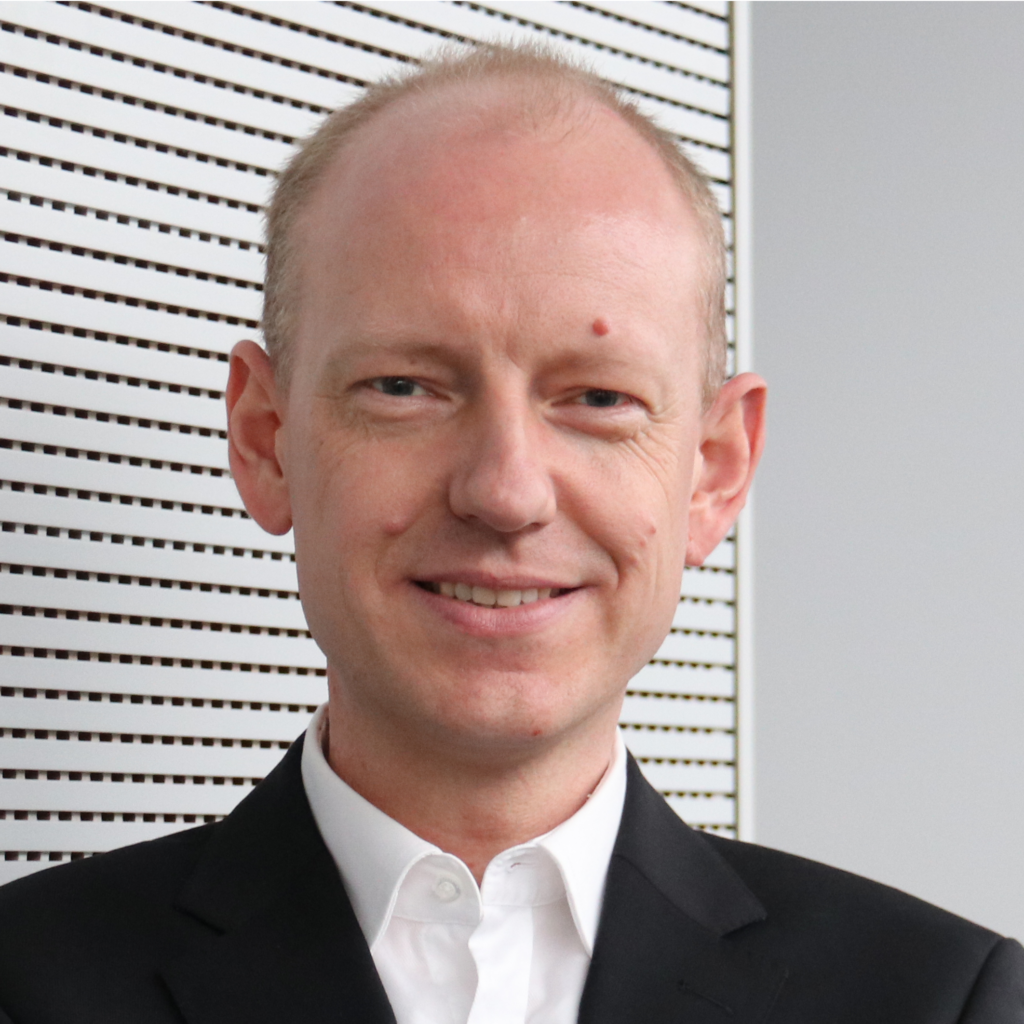
The original idea was from the doctoral thesis of our CDO, Frank Pössel-Dölken, and we began developing MORYX at Phoenix Contact in 2009. Although Phoenix Contact had contributed a lot towards digitalizing factories, we established that there was still a gap between various systems in IT (i.e. SAP or team centers) and OT (robots, manufacturing machines…). MORYX’s role is to close this gap and ensure data and control flows between IT and OT – with as little manual intervention as possible. And since there was nothing available in the market that we could use, we got the go-ahead to develop MORYX. It was used to operate the first machine at Phoenix Contact in 2010.
Over time, the scope and quality of MORYX increased and it has been available as a commercial product in the market for three years now. More and more customers are placing their trust in MORYX to master the challenges I mentioned earlier.
How does MORYX work and what advantages does it have as opposed to conventional production management and scheduling systems?
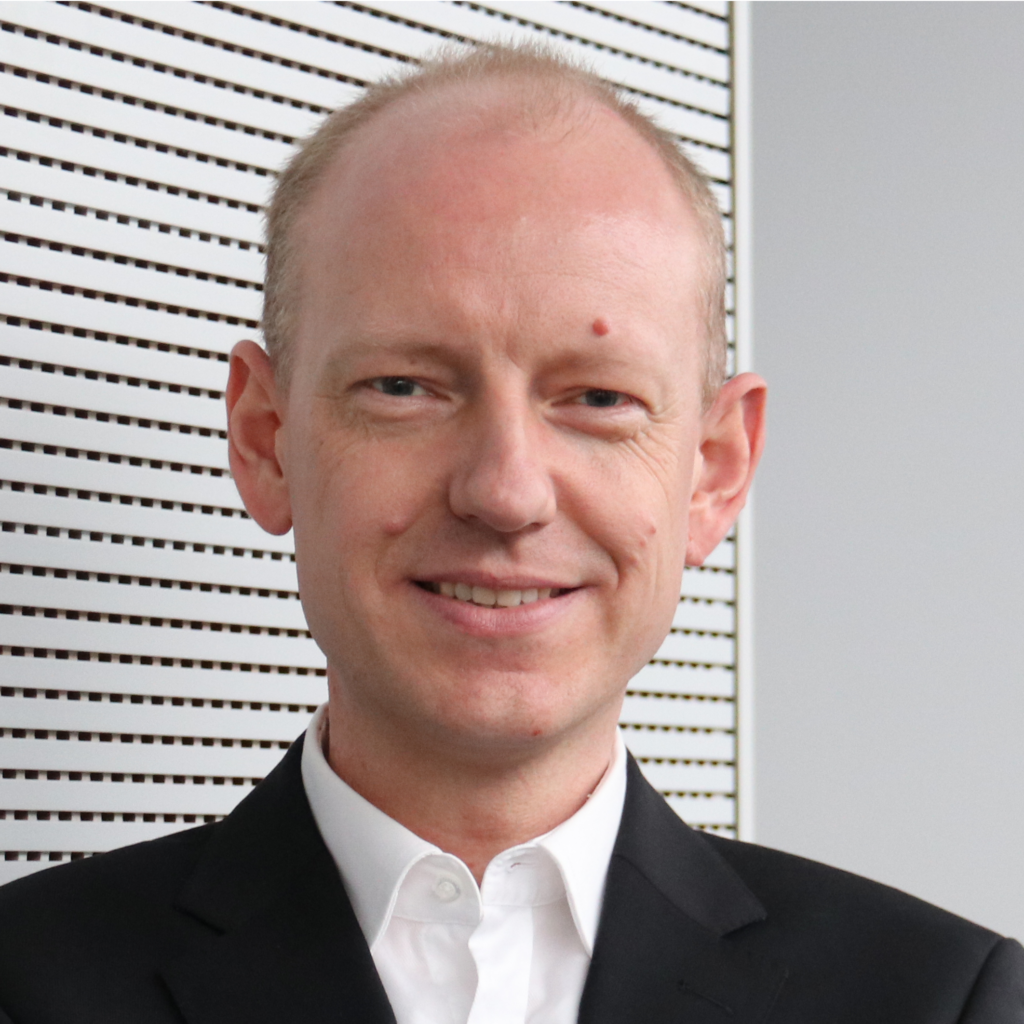
As a leading provider of automation systems, we naturally use PLCs for control and regulation tasks. However, these systems are optimized for real-time and safety applications as well as for connecting sensors and actuators.
We are convinced that every system should have clearly defined tasks in order to maximize maintainability and scalability. Therefore we have placed the control of production and its individual areas in Manufacturing Operations Management MORYX. This is an approach that more and more companies are also adopting. In short, we leave the automation systems as they are and separate the functionality of the control and management data.
Of course, there are systems above automation systems, MES for example. These assign the orders to machines or identify KPIs. However, they cannot actively intervene in a manufacturing process. Let’s assume that product A and product B need different materials in the manufacturing tool or machine. MES cannot actively access machines to control retooling processes or rather, it fails to provide the transparency to see what is happening and how to manage it. MORYX, on the other hand, can do this. It is the first system which can be wholly deployed in the entire factory and actively control the production. But, it has been developed in such a way that production workers can configure it themselves without having a software developer coming into the factory all the time to eliminate a problem. This increases flexibility, lowers costs and the software developer can focus on more important matters.
One final point: we rely on a standardized technological environment. We are the first company to introduce standard technology like Microsoft. net into the factory. We do not see the need to develop new technology when tried and tested products are already in the market. In this way we keep our costs low and can concentrate on what MORYX is there for, namely to operate machines.
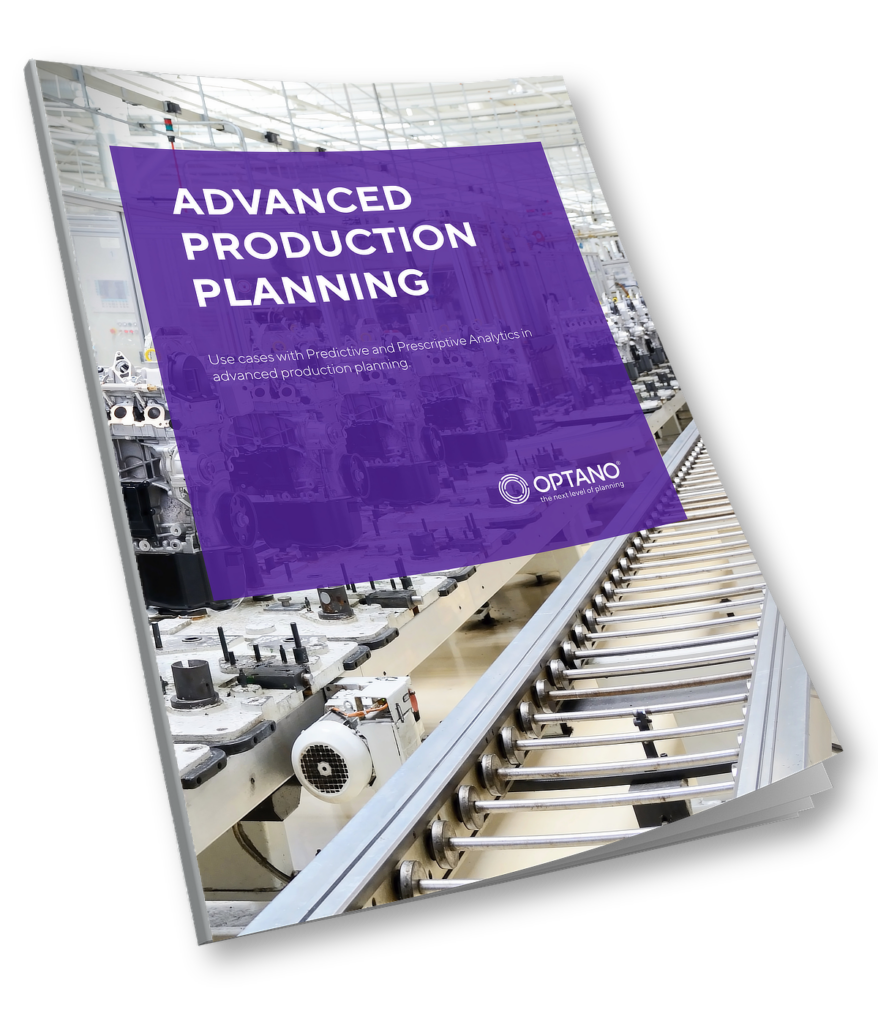
That sounds fascinating. Do you have a favorite feature in MORYX?
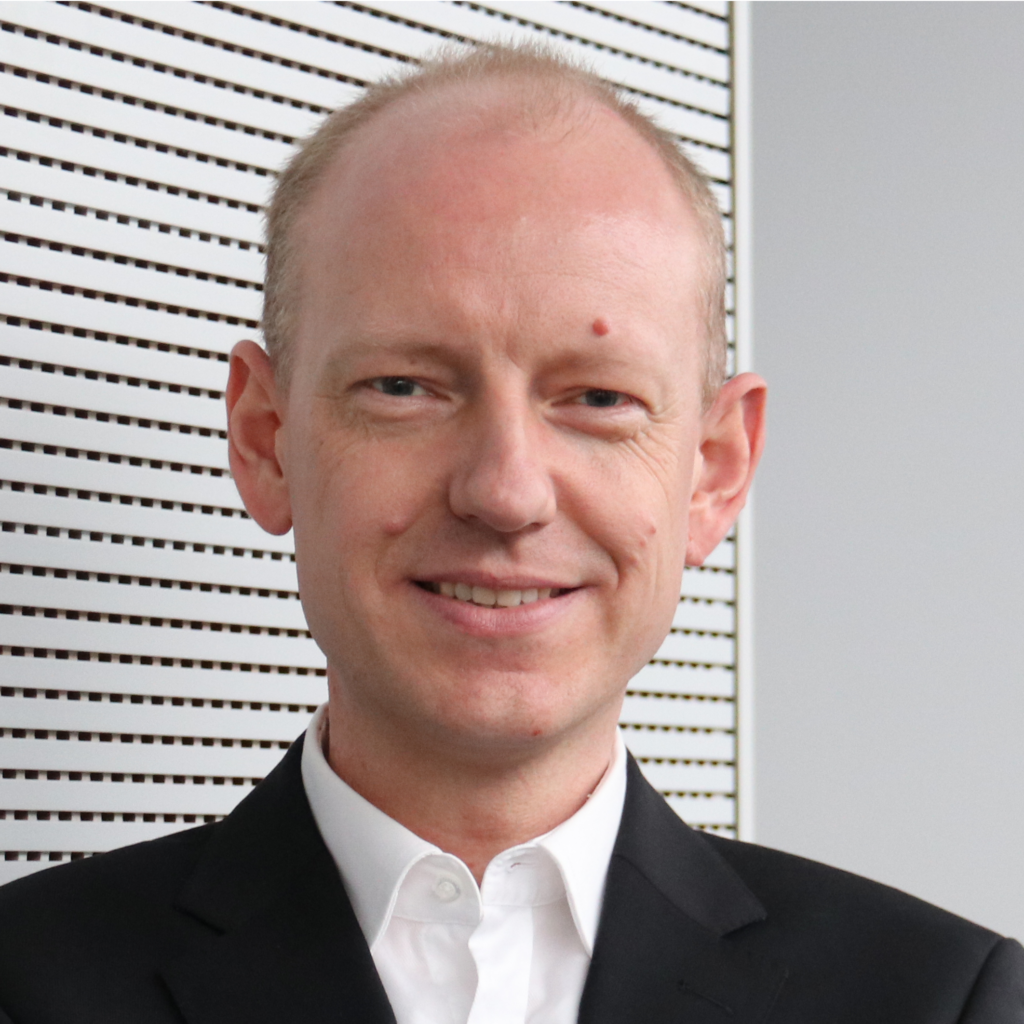
That’s easy -the Factory Monitor!
We work here with a so-called digital twin. We map all buildings, machines, components, products, processes and much more as a digital counterpart. The Factory Monitor is responsible for visualization. You can upload a picture of your own factory and position the digital twin with its buildings or machines on it. With a simple double-click on any hall, you can easily see what is happening there in real time.
This is my absolute favorite feature. It provides maximum transparency in real time. And, of course, it is entirely web-based so we can use it no matter where we are.
In Europe we can advance advance digitalization, but only if we enter into collaborations
MORYX is also available as an open-source platform. Why is that?
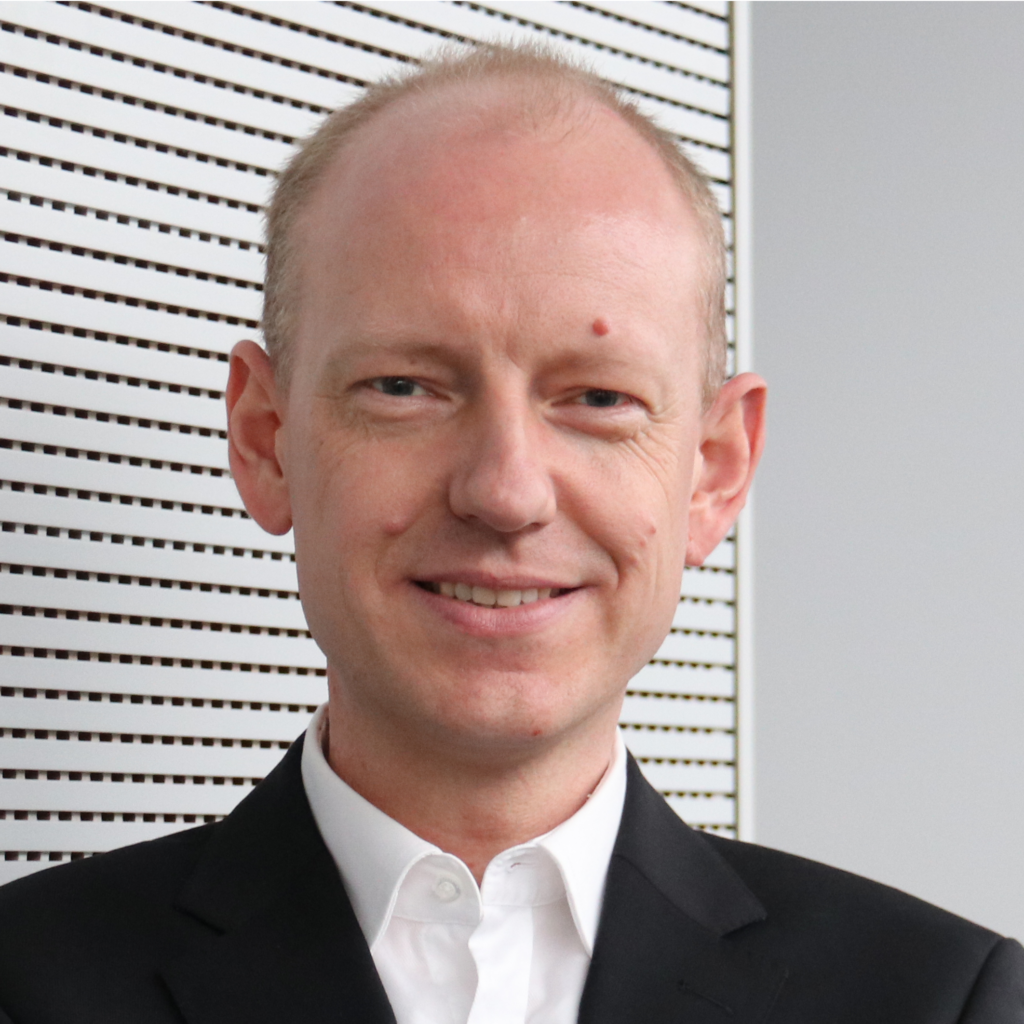
Parts of MORYX have been standardized and open-source for two years. This makes building IOT applications simple and straightforward. For example, it offers everything you need to get the boilerplate code of IoT applications off the shelf as reusable software packages. We also offer interfaces for exchanging digital twins – such as the OPTANO optimization module – as open source.
The motivation behind this is obvious: on the one hand, to promote MORYX, but on the other hand, to incorporate the know-how and ideas of the community into MORYX. We also make it available to students to support them with high-level languages and scripts.
However, the open source approach is not factory-specific. For factory-specific features such as the Factory Monitor, you need to purchase a commercial license.
You work with many various cooperation partners besides OPTANO. What is the philosophy behind this?
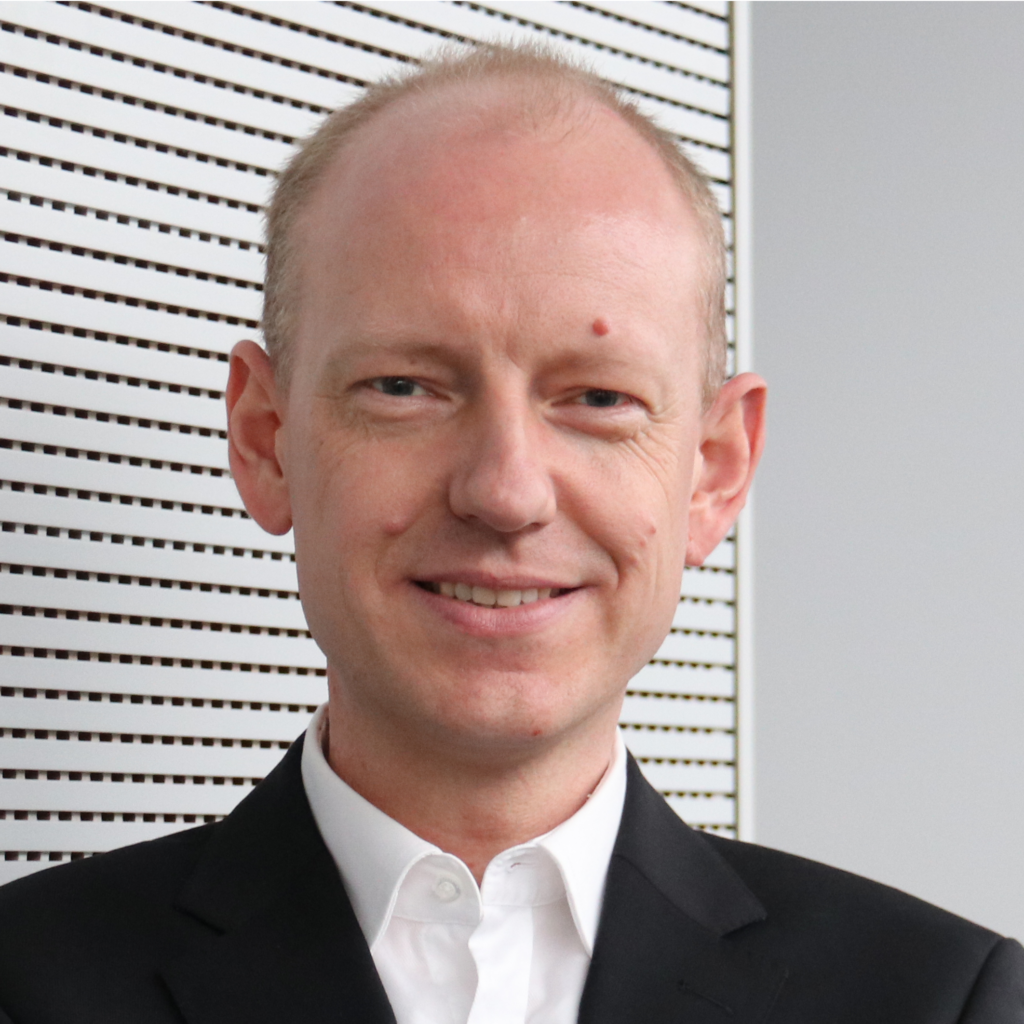
We believe that we can really advance digitalization here in Europe, but only if we enter into collaborations. We believe that not every company should implement everything itself, as there are probably few companies that can do everything. Our cooperation is a good example of this: For example, we don’t have the expertise when it comes to developing mathematical models to optimize production processes. That is your core competence. We focus on our task, which is to further develop the core of MORYX. However, in order to equip MORYX with additional functions, we take partners on board. In this way, we ensure that MORYX is constantly evolving in line with market requirements.
Why did you choose to work with OPTANO and how successful has the cooperation been so far?
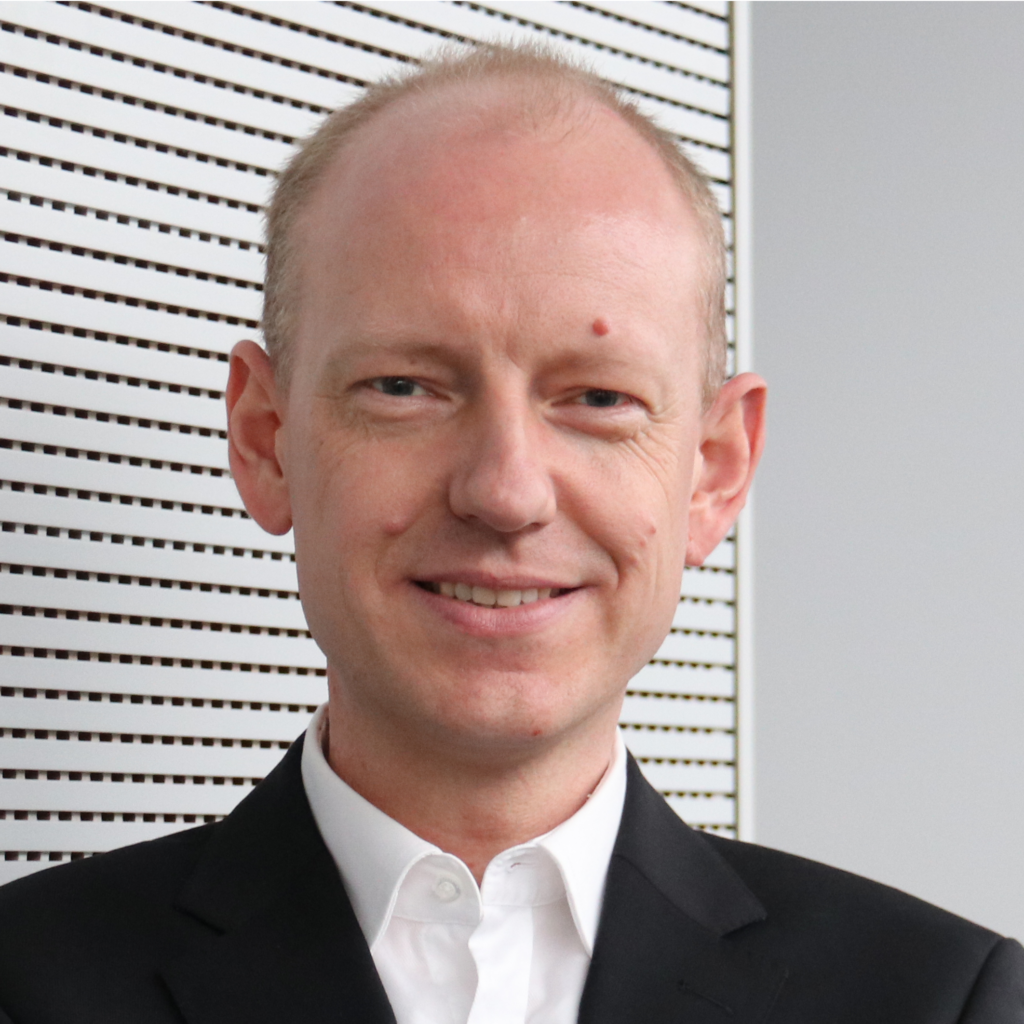
At the moment, MORYX takes production orders 1:1 from the upstream systems – “unoptimized”, so to speak. Together with OPTANO, we would like to see whether a mathematically optimized sequence of production orders has a positive effect on process effectiveness. And, as is often the case, our contact came about through personal relationships. Someone knows someone who knows someone who works at OPTANO…
So, we had a first meeting to see if we were a good fit. Above all, whether we had a common understanding of how to drive innovation forward. Because we don’t want to create something that already exists, but something truly innovative that brings measurable benefits to production. And it became clear relatively quickly: the mindset of OPTANO and MORYX fit together perfectly.
We then held a 2-3 hour workshop with Sven Flake and some of his team at our premises in Blomberg to roughly sketch out the project. The result of the joint development was an MVP that we are currently testing extensively. With the help of the OPTANO module in MORYX, customers can make their production more efficient. For example, they need to carry out fewer set-up processes between orders, thus minimizing the non-value-adding time in a production process. Orders can now also be parallelized. This either shortens the runtime or increases throughput. Ultimately, we have one overarching goal: to maximize the OEE (Overall Equipment Effectiveness) of the factory (or individual systems).
All in all I can say is that our collaboration with OPTANO has been very dynamic and creative and certainly offers added value to our customers. In our view, it is the first step towards a close partnership in the future.
What can you tell us about the mutual presentation that will be held at the SPS in Nuremberg?
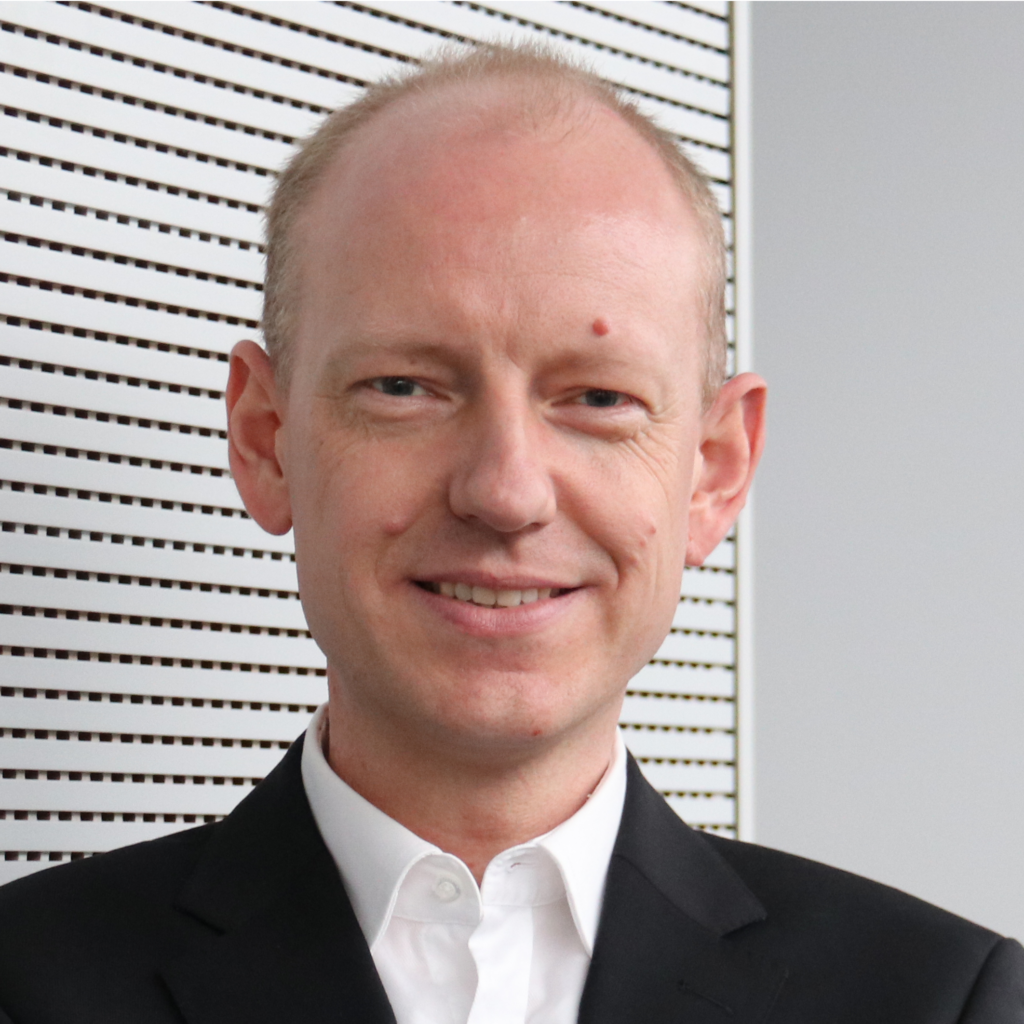
MORYX will be represented at the Phoenix Contact stand at SPS, Smarter Product Solutions, which is one of the largest international trade fairs for electrical automation technology. Here we will be presenting the MVP we developed together with OPTANO. We are sure that the possibility of optimizing production orders in real time and seamlessly transferring them to machines and manual production options will meet with great interest. We look forward to a lively exchange with the trade fair visitors.
Lutz, thank you for finding the time to talk with us here at OPTANO.
Also, if you are interested in OPTANO’s solutions for production planning, you can download our factsheet on this issue below.
Have you got your Factsheet on this topic yet?
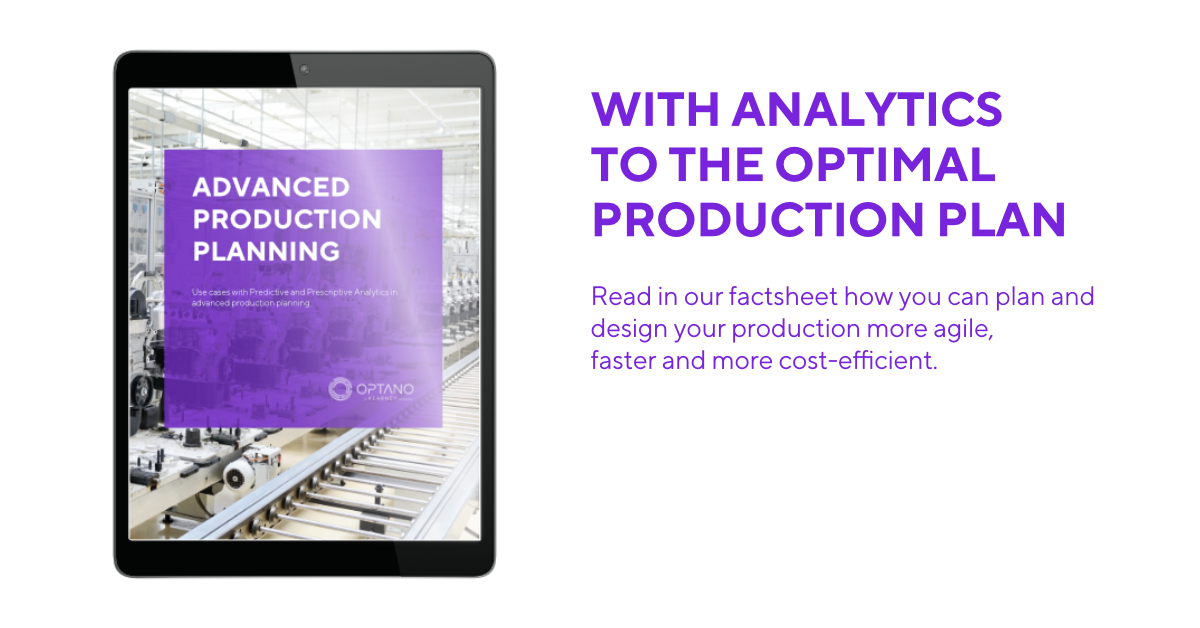
In our factsheet Advanced Production Planning we present some of the use cases of Predictive and Prescriptive Analytics in modern production planning which you can download here.
To obtain our factsheet, all you need to do is enter your contact details in the space below. A pop-up window will then open to download the whitepaper. Please note that by providing us with your email address, you agree that we may contact you on this topic. You may revoke this agreement at any time by contacting [email protected].