Making more
efficient use of
material resources
Everything we possess originates from some form of material resource. For example, the bill of materials for a smartphone contains no less than 35 materials that are required for its manufacture: glass for the screen, lithium for the battery, copper for the cables and zinc for microphones and speakers, to name just a few.
Of course, it is not just smartphones which come with an extensive bill of materials and our exploitation of these resources is taking its toll on the environment. With sustainability being the buzzword, businesses are now also feeling the pressure to manufacture products with a view to reducing the effects of climate change, among others.
Here, we want to focus in detail on how mathematical optimization methods can help businesses use their material resources more efficiently – and also save costs in the long run as a result.
The demand for materials far exceeds supply
Resource efficiency can boost a company's competitiveness
On the one hand, material resource efficiency contributes towards protecting the earth’s natural resources and on the other towards the competitiveness of one’s own company by deploying the materials in manufacturing processes more mindfully. According to the DEMEA institute, raw material costs can be reduced by approx. 20% on average. These are savings which could be passed down to the end consumer in the form of lower prices, for example. However, companies must implement the right strategy which involves making long-term changes to the planning of their operating processes as well as to their supply chains.
One vital way to help streamline efficiencies and cut costs is to track direct material costs through the manufacturing process. This means analyzing how the direct materials are purchased, assembled, and the operations required to integrate them into the finished product.
Product design and development
It is here where the main decisions on the direct materials are made. What kind of material is to be used? What quality and quantity of material? A poor decision here can be very costly later down the line.
Developers can optimize the design of the product to keep the amount of material required as low as possible. For example, by reducing the size or volume of the product where possible. Another important aspect to consider is the complexity of the product. The more complex a product is, the more components, i.e. materials are needed. Furthermore, if the product is complex in its design and planning, it is more difficult to manufacture. The result: errors in production which lead to wasted material , products which fail to pass quality checks need rework, which is costly.
Buying materials at the right price and of the right quality
After the materials and their features have been decided upon, they need to be purchased. Here, purchasers should select suppliers carefully and determine the right quantity in consideration of price, quality and logistics in order to obtain the optimal cost-benefit ratio.
Price is, of course, a deciding factor. Raw material prices are subject to severe fluctuations so it makes sense to buy them when prices are low. Having a choice of reliable suppliers can give purchasers a considerable advantage as this makes it easier to negotiate competitive prices. Another factor that needs to be considered is the risk of a loss in value. This can be reduced by keeping throughput times and inventory at a minim to avoid unnecessarily long storage times and material damage. A solution here can be to implement Just-in-Time delivery for specific products, ensuring that you do not have more in your warehouse than necessary. However, the pros and cons of this method need to be weighed up very carefully. For more information, read our blog Optimized Inventory Management.
Reassessing production processes
A high proportion of material waste is generated in production. Too much material waste can mean that the machines are not working as efficiently as they should, thus producing goods that fail to meet quality requirements. This results in additional costs for rework, corrections and disposal costs for scrap. This can be reduced to a considerable extent. By assessing manufacturing practices and machines, companies can pinpoint areas of inefficiency and take steps to improve these. Regular (predictive) maintenance is essential. However, if machines are older, it may be worthwhile investing in new machinery which is state-of-the-art, performs better and more efficiently.
More interesting articles
Streamlining efficiency calls for optimal planning
As described above, the efficient use of material resources calls for close cooperation between R&D, Production, and Purchasing. After all, they are all involved in deciding which materials to buy, how much is needed and when. Yet, cross-departmental planning processes can become highly complex, no matter how well they comunicate with one another. This is because each department has its own constraints, variables and thus conflicting goals. In this case it is easy to lose sight of the common objective. What is needed is planning software which supports businesses in optimizing production workflows, order processes and inventory management, as well as identifying the cross-dependencies in planning processes. In this way, informed decisions on how to make efficient use of resources can be made.
The right planning needs the right software: OPTANO can help
Planning software such as OPTANO applies mathematical optimization methods for needs–based planning. With the help of sophisticated analytical methods such as Predictive and Prescriptive Analytics, plans can be created based on a model which maps the entire production process – taking into consideration all objectives, resources, variables and constraints. Special solvers are used to help come up with the optimal solutions to a company’s specific problem.
OPTANO can identify the right measures in order to achieve your objectives –after sound analysis of all your available business data. Various alternatives can be analyzed and compared with one another in what-if scenarios in order to find the proven best solution. For example, by using the same data in multiple scenarios you can make long and short-term demand forecasts so that you know which material you need to order, how much and when. This provides you with more security, even in case of disruptions, as you can reschedule production quickly and easily, thus saving resources and keeping costs down. By analyzing your inventory management you can identify which steps to take in order to prevent surplus inventory and be confident that you have a smooth production workflow where resources are used efficiently and sustainably.
Whether it is tactical or operational planning, OPTANO generates plans quickly and easily in line with your requirements. Do you want to learn more? Then download our factsheet Advanced Production Planning below. Or simply contact our consultants who are at hand to answer any questions you may have.
Time is running out - and our resources as well...
It has taken mankind centuries to discover and learn how to use raw materials such as metal, coal, gas, oil, plastics, etc., yet their depletion is taking far less time. Both industry and consumers need to address the issue urgently. Resource efficiency is a good place to start…
Have you already got your factsheet on this topic?
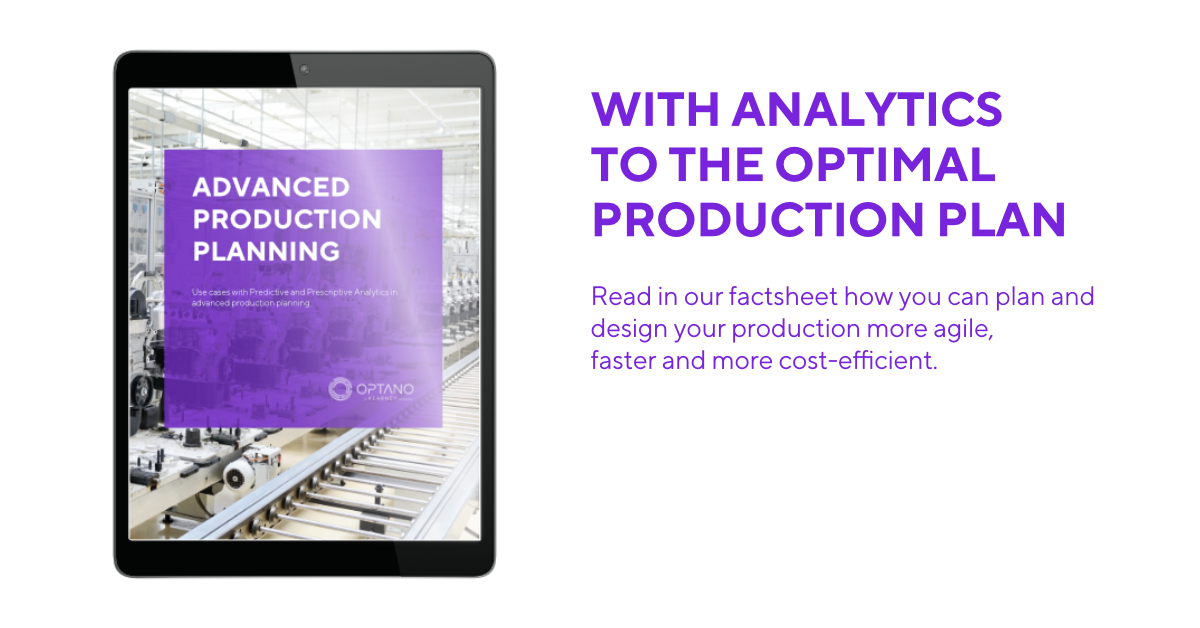
In our factsheet Advanced Production Planning we present some of the use cases of Predictive and Prescriptive Analytics in modern production planning which you can download here.
To obtain our factsheet, all you need to do is enter your contact details in the space below. A pop-up window will then open to download the whitepaper. Please note that by providing us with your email address, you agree that we may contact you on this topic. You may revoke this agreement at any time by contacting [email protected].