How mathematical
optimization helps to
prevent production failures
There’s a rumble, a humming sound, then a bang – and suddenly the machine comes to a standstill and the deceptive calm makes us fear the worst … the machine has broken down and will lie idle, for the time being at least. We recently had a similar scenario in our basement: our washing machine appeared to be working as usual – we could switch it on, select the program and start it. But then the drum just stopped turning mid-program. No matter which tip from the internet we tried, nothing worked: the machine would no longer do what it was supposed to do. Considering it was more than 15 years old we quickly realized that it wouldn’t be worth having it repaired and that we would need to buy a new one. The current delivery times for many brands made us break out in a cold sweat – a household with no children and no washing machine for 4 months? No way… we had to come up with plan B!
When a machine breaks down…
Although our defective washing machine made us panic for a moment, the actual consequences for our family were still very manageable. If a machine breaks down in a manufacturing company, then it quickly results in huge financial losses. This is because as long as the machine is lying idle, the world around it still keeps turning. Incoming goods are delivered, products must be shipped. The longer the machine – and possibly even the entire assembly line -are at a standstill, the greater the consequences: the warehouse is overstocked, delivery dates cannot be met. While attempts are made to get the machine up and running again as soon as possible, production has to continue as well as it can – and as fast as possible!
… the production planner is called for.
And so the production planner responsible faces a major task: Which orders can still be executed even though one machine isn’t working? Which delivery dates need to be postponed, which ones can be brought forward? In other words, a completely new production plan needs to be created which can work without the defective machine and yet still meet all the constraints and deadlines as precisely as possible. Solving this type of problem manually or with spreadsheets is a highly laborious task. It calls for very detailed knowledge about the production itself, orders and their correlations. Finding a good solution here within a short space of time is simply not possible in view of such complex dependencies.
What happens now?
Mathematical optimization can solve this problem very easily. Drawing up production schedules using mathematical optimization is based on a model which represents your entire production and includes all of your machines, orders and constraints. Once this model exists, it can easily be adjusted. In this particular case: the defective machine is simply removed from the model and will no longer be considered in the planning process. Any further information such as orders, set-up times and the like remain the same.
It is now quite easy for the optimization to calculate a new production plan based on this slightly modified model .
Rescheduled in an instant with OPTANO production
Thanks to today’s perfect production flows, every second in which production comes to a standstill – even just a part of it – costs money. Therefore it is particularly important that the new schedule is available fast and that production can continue.
OPTANO production ensures that such an issue can be dealt with very easily and swiftly. There is an extra view for downtime in which planned downtime such as maintenance, but also unforeseen downtime can be entered for each machine.
For the machine that has just broken down, you can simply enter the probable length of time in which it cannot be used. The optimization cannot schedule this machine for the time period that has been entered. If you let the optimization calculate again, you will get a new production schedule which has been organized around the defective machine. With this schedule, you can now distribute all the current orders among the machines available as best as possible. And because this can be created very rapidly, you hardly lose any production time.
Stay one step ahead with OPTANO production
OPTANO production can, of course, do a lot more than simply respond fast to machine failure. Whether it is tactical or operational planning – with OPTANO production you can generate optimal plans based on your requirements fast and easily. It means you can guarantee delivery reliability, maximize your machine capacity and ensure shorter throughput times with optimized set-up times. The result: your production planning will always be optimal and, at the same time, so manageable and flexible allowing you to get the best out of any situation – now and in the future.
If you would ike to learn more about how your production planning can benefit from mathematical optimization and what else it can do, simply download our factsheet “Modern Production Planning using Predictive and Prescriptive Analytics”. And of course you can also contact us directly. Dr. Sven Flake is happy to talk to you in person and answer any questions you may have on optimal production planning.
And what is plan B doing?
Fortunately, the problem with our broken washing machine was just as easy to solve: Even though we had considered bridging the month-long delivery time by taking our washing to a self-service laundry or to friends and family, we soon decided that this would not be an option in the fall. Our number one condition was that we needed a new washing machine which had to be delivered immediately. So, after wavering back and forth and studying the product data, we chose a machine from those that could be delivered immediately. Two days later it arrived and we hope it will run as long and reliably as its predecessor. Because even if the solution can be easy – a defective machine always causes havoc at first.
Do you already know our factsheet on the topic?
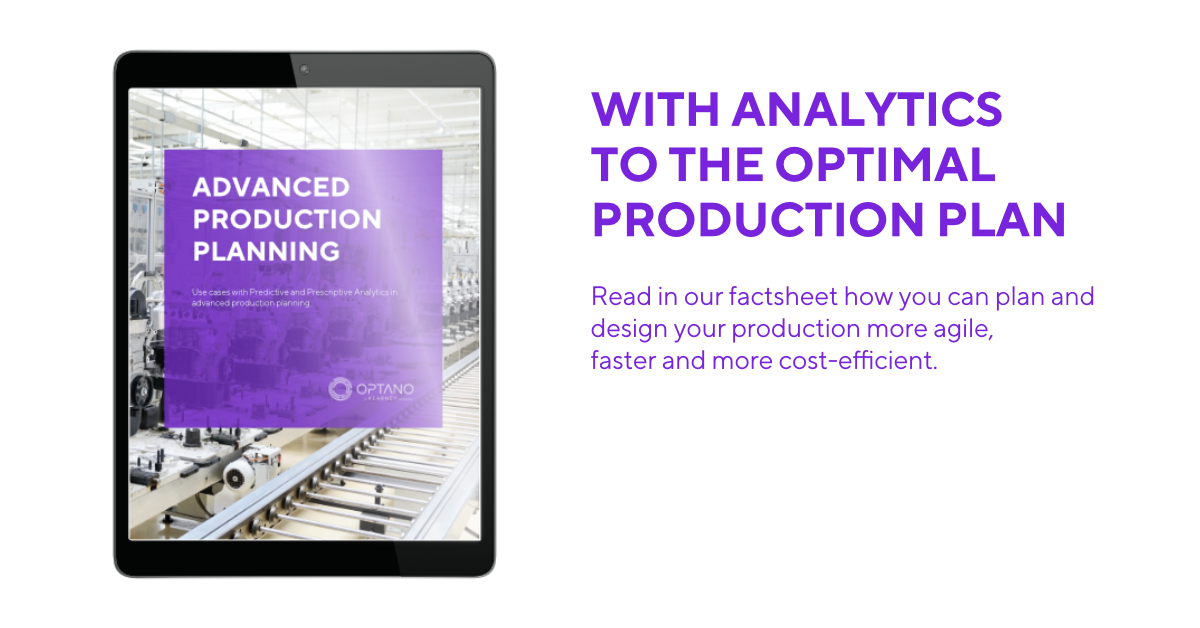
In our factsheet Advanced Production Planning we present some of the use cases of Predictive and Prescriptive Analytics in modern production planning which you can download here.
To obtain our factsheet, all you need to do is enter your contact details in the space below. A pop-up window will then open to download the whitepaper. Please note that by providing us with your email address, you agree that we may contact you on this topic. You may revoke this agreement at any time by contacting [email protected].