How to overcome challenges in production
Challenges in production
Nowadays modern production has to continuously juggle many issues at once which require constant evaluation and improvement so that it continues to work efficiently. In this article we look at the main challenges that production planners face and explain how they can be overcome:
Demand forecasts
Inventory management
Plant efficiency
How can a company keep costs low yet keep efficiency high without cutting corners in product quality?
Finally, one of the biggest contributors towards plant inefficiency is material waste in production. Wastage – often a consequence of poor planning and inventory management – can lead to high losses and also high overhead.
Lack of skilled employees
Companies nowadays are finding it increasingly difficult to employee workers with the necessary skills and qualifications in manufacturing. This lack of skilled employees means that work is not performed properly and product quality suffers as a result. The finished goods have flaws and must be reproduced, which leads to delays and bottlenecks.
(Still) too much reliance on manual solutions
The unwillingness or inability to effect digital transformation can be attributed to several aspects: it is expensive to implement the new technology, existing workers require training to work with new software or there are simply not enough workers in the company with the necessary skills to apply it.
Yet, if businesses fail to make the transformation towards digitization, they will only lag behind those who have and be unable to compete in their respective markets.
And, returning to the issue of skilled employees – or rather the lack thereof: Businesses which have dated, error-prone, manual processes in place are highly unattractive to technology graduates. They will go to companies with smart manufacturing processes which require their valuable skills to optimize production methods. And, as we explained above, the lack of a skilled workforce only serves to damage a company in the long run.
More interesting articles
Mathematical optimzation for effective production processes
Applying analytical methods such as mathematical optimization is especially recommended when it comes to complex procedures such as production planning. With the help of Predictive and Prescriptive Analytics, production plans can be created based on a model which maps the entire production process – taking into consideration all objectives, resources, variables and constraints. Special solvers are used to help come up with the optimal solutions to the production problem.
Production does run like clockwork - with OPTANO production
Planning software such as OPTANO applies mathematical optimization methods to create the necessary transparency in planning which can help you make informed decisions on the best course of action to take.
With OPTANO production it is possible to identify the right measures in order to achieve your objectives –after sound analysis of all your available business data. In this way, alternatives can be analyzed and compared with one another in what-if scenarios in order to find the proven best solution. For example, by using the same data in multiple scenarios to analyze you can make long and short-term demand forecasts and prepare and respond quickly to unexpected disruptions by being able to reschedule in good time. By analyzing your inventory management you can identify which steps to take in order to prevent surplus or deficit inventory and be confident that a smooth production workflow is in place, that you can fulfil customer orders as planned, reduce levels of wastage and improve your plant efficiency.
Whether it is tactical or operational planning, with OPTANO production plans can be generated quickly and easily in line with your requirements. Do you want to learn more? Then why wait? Contact us today. Our consultants are at hand to answer any questions you may have.
And is the pocket watch still ticking?
Have you already got your factsheet on this topic?
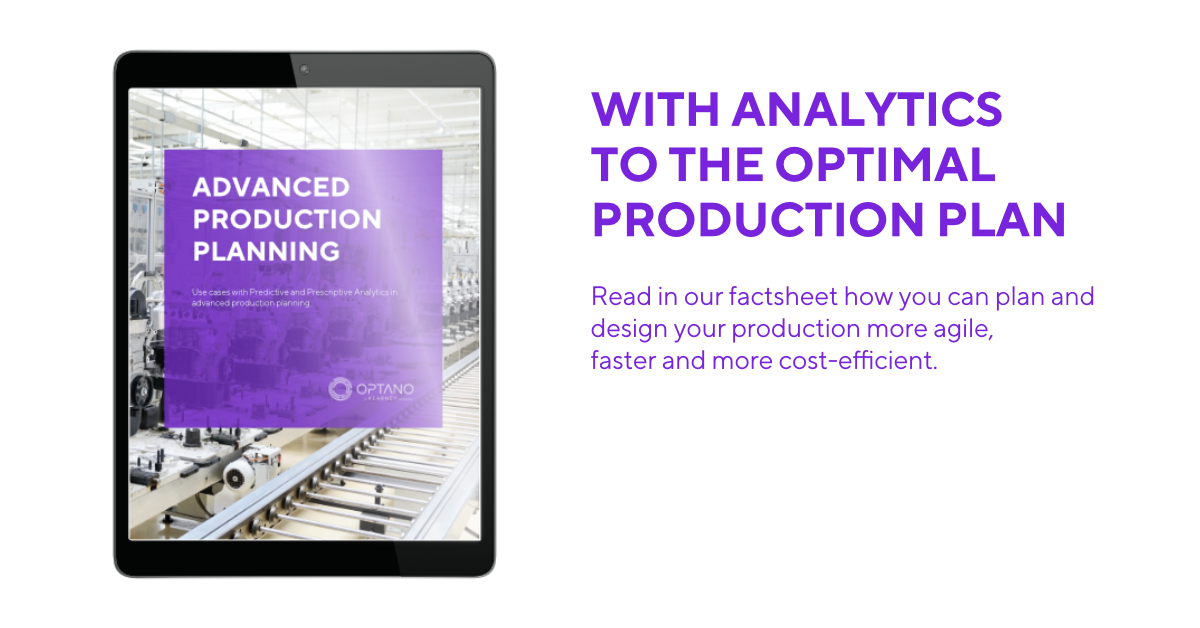
In our factsheet Advanced Production Planning we present some of the use cases of Predictive and Prescriptive Analytics in modern production planning which you can download here.
To obtain our factsheet, all you need to do is enter your contact details in the space below. A pop-up window will then open to download the whitepaper. Please note that by providing us with your email address, you agree that we may contact you on this topic. You may revoke this agreement at any time by contacting [email protected].