Increased competitiveness through cross-docking
Everyday life at the cross-docking terminal: The driver of a truck scheduled for a specific time reports a delay in his arrival time. In the distribution terminal, action must now be taken quickly, because the slightest disruption will put the entire process behind schedule.
In cross-docking, the six Rs of logistics play a particularly important role. The right products must be in the right place at the right time in the right quality and quantity at the right cost, because cross-docking is strongly geared to the just-in-time principle. Reliable plans are thus an important prerequisite for well-functioning cross-docking logistics.
Cross-docking: transshipment point instead of warehouse
In the “classic logistics chain”, the warehouse is an important component and link from the supplying companies to the consumers. When handling large quantities of goods, warehousing processes, inventory storage activities and goods picking lead to high costs associated with a significant capital commitment.
In cross-docking, the flow principle is realized, in which the storage of goods is completely eliminated or reduced to a short interim storage. Cross-docking is thus a type of goods handling that simply skips the process steps of putaway, inventory storage and picking. Manufacturing companies and resellers benefit especially from distribution cross-docking, in which products from different suppliers are combined into a mixed pallet for onward transportation.
In recent years, the importance of cross-docking in logistics has increased significantly. Companies can reduce their warehousing costs and minimize storage space requirements. Efficiency and effectiveness in logistics can thus be increased. At the same time, shorter throughput times for goods are realized. Speed, productivity and flexibility are of crucial importance in competitiveness for companies.
At a glance:
Advantages of using cross-docking in warehouse logistics
- Reduction of storage space requirements
- Minimization of inventory costs
- Processes for storage, inventory and retrieval are eliminated
- Accelerated flow of goods and reduced throughput times
- Shortening delivery times
Reliability - the be-all and end-all of cross-docking
The prerequisite for successful cross-docking is a smooth process. The aim here is to design and control processes optimally. To this end, all process steps should interlock as seamlessly as possible. This is the only way to achieve the goal of the cross-docking principle: To deliver the correct products to the recipients in the right quantity at the specified time or at the appropriate frequency.
For this to succeed, the perfect coordination of all players is absolutely essential. The prerequisite is a flawless flow of information and transparency between all instances, from the supplying companies to the carriers and the distribution terminal to the recipients. In addition, agreed delivery dates must be strictly adhered to. Reliability is therefore an important criterion for successful cross-docking logistics.
High demands on the technology and the IT system
In cross-docking, the synchronization of goods and information flows must be ensured. And the real-time exchange of data and information between all instances is also imperative for a smooth process. With this complexity, cross-docking places very high demands on the IT solutions used in particular.
In addition to warehouse management software that ensures trouble-free logistics processes with master and movement data, the use of agile planning software is essential. Reliable plans, a prerequisite for the good functioning of cross-docking, can thus be created quite easily.
Create reliable plans using mathematical optimization and OPTANO
With the help of mathematical optimization, it is possible to master the complex requirements of planning in cross-docking logistics. The creation of plans with planning software such as OPTANO is based on a model that maps the entire logistics process – taking into account all objectives, resources, variables and restrictions. With the use of special solvers, optimal plans for cross-docking can then be generated.
More interesting articles
Delivery delay: A new plan must be made
The creation of initial plans is not the only complex task in cross-docking logistics. As described at the beginning, delivery delays can occur at any time. The arrival of a delivering truck is postponed, for example, because the vehicle is stuck in a traffic jam, has broken down or there were already delays during loading.
However, changing the arrival time of even one delivery affects the entire cross-docking process, which is influenced by the following restrictions: Each truck has an arrival time, for each truck there is a desired departure time and as a precedence restriction there is the relation between incoming and departing vehicle. This means that the vehicles can only be loaded when the goods are on site.
It is necessary to reduce the costs that automatically arise in the event of a delay: When changing the schedule, a wide variety of handling times must be taken into account and put into relation with waiting times, because handling causes more costs with higher personnel requirements, among other things. In order to save costs, the time span must also be reduced.
With these dynamic and complex requirements, OPTANO enables rescheduling and resynchronization at the push of a button for the entire cross-docking network.
A brief digression
A master thesis provides insights into OPTANO
In his master’s thesis, our colleague Hannes Post took a closer look at the topic of truck scheduling in the context of cross-docking.
First, the differences between the two most important “Service Modes” in cross-docking were considered. While in the “Exclusive Service Mode” there is a strict division of the docks, which are used either for the handling of incoming or for the handling of outgoing trucks, there is a higher degree of freedom in the “Mixed Service Mode”. Here, all docks can handle both inbound and outbound trucks. The “Mixed Service Mode” has a larger share in practice, but is less explored.
The models used in the OPTANO software are suitable for both the “Exclusive Service Mode” and the “Mixed Service Mode”.
Restrictions, objective function and algorithms
Another chapter of the master thesis deals with the restrictions of cross-docking already mentioned in the text. Besides the precedence restrictions, the arrival and departure times of the trucks are the most important limiting factors.
The objective function involves minimizing costs while taking into account the different dispatch times, desired departure times, and the trade-off of dispatch times having a higher cost factor versus just waiting times.
The initial plan is created using a genetic algorithm, a metaheuristic. In order to exclude further potential for improvement, this plan is also given to a solver as an initial solution.
The reactive rescheduling
In addition to the creation of initial plans, fast reactive replanning is essential in the event of disruptions in cross-docking logistics. Here, in the event of a delay, the initial plan is first shifted to the right by determining, among other things, the point in time from which all operations or jobs already started are fixed in the initial plan. The new plan with the right shift is then used as a starting solution for the metaheuristics to quickly convert it into a new admissible plan.
Parallelization
To enable an even faster response during replanning, the genetic algorithm used is parallelized, thus significantly reducing the runtime. For test scenarios of realistic size, it is thus possible to react to disturbances in less than a minute and to find a new plan that minimizes the costs incurred.
You would like to learn more?
To find out if mathematical optimization can bring benefits to your logistics, simply download our factsheet “Why Supply Chain Analytics”.
If you would like to learn more about how OPTANO can improve your planning, or if you have any further questions, please contact us today. We’ll be happy to answer all your questions. Or, drop us an email and we’ll get in touch with you.
Do you already know our factsheet on this topic?
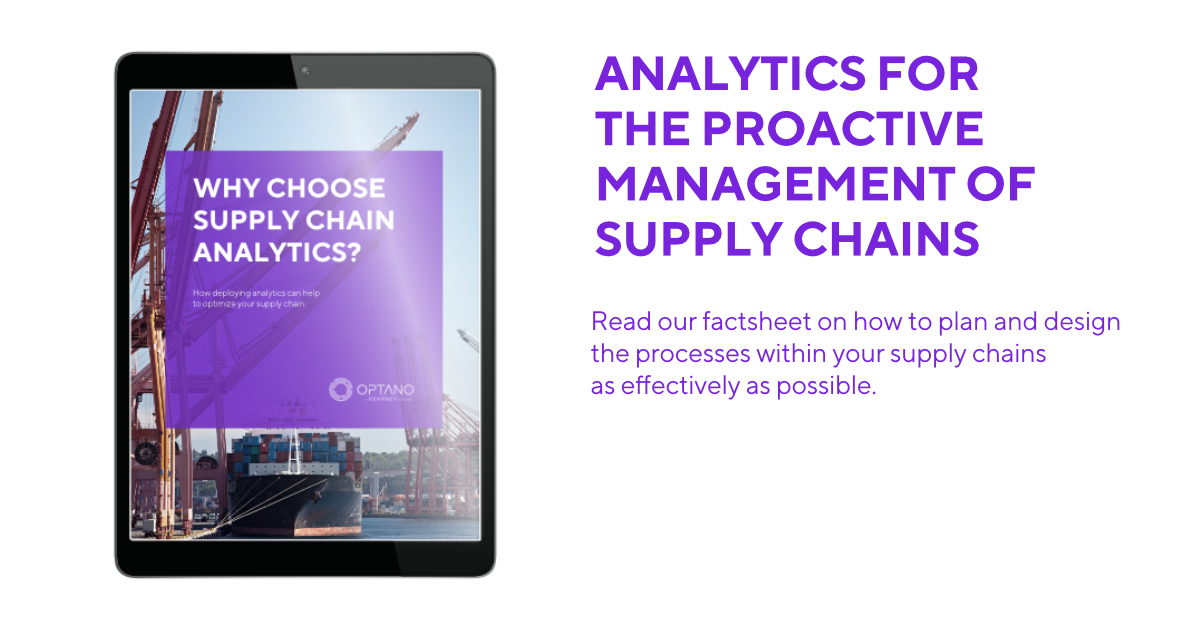
In our factsheet “Why choose supply chain analytics?” we describe the different types of supply chain analytics. You will discover how supply chain analytics works and how it can help to optimize your company’s supply chain.
To obtain our factsheet, all you need to do is enter your contact details in the space below. A pop-up window will then open to download the whitepaper. Please note that by providing us with your email address, you agree that we may contact you on this topic. You may revoke this agreement at any time by contacting [email protected].