Capacity planning
in chemical manufacturing
You may be familiar with the situation: You want to throw a party and need to decide how much food and drink you will have to buy. If you are like me, you will tend to buy more than is needed – just in case! However, this often means that the fridge is full of leftovers at the end of the evening. Often, a lot of the food goes to waste if it cannot be eaten soon enough.
This is a classic case of failed capacity planning on a small scale. It is annoying, but without any serious long-term consequences. Even so, money and resources have still been wasted. Now, imagine an organization that has to plan capacity for major projects or production. It simply cannot afford to miscalculate. In this article we explain how businesses can benefit from optimized capacity planning, using chemical manufacturing as an example.
What is manufacturing capacity planning?
Generally speaking, businesses apply manufacturing capacity planning in order to calculate how much they can (realistically) manufacture in order to meet the demand that has been forecast. The main objectives are to maximize profit, minimize costs, ensure smooth workflows and processes, and achieve maximum efficiency. Here, various factors must be taken into account such as resources (personnel, equipment and machinery, materials) as well as lead times and production processes.
Capacity planning in chemical manufacturing
In the chemical industry, the objectives behind capacity planning are the same as those mentioned above, but the factors to consider here are of a very specific nature.
Many of the materials and intermediary products processed in the chemical industry are subject to strict (quality) regulations. Products have to be manufactured exactly in line with the prescribed formulas. The specified amounts of each ingredient and the exact composition must be observed because even a slight change to an ingredient or formula can lead to deficiencies and disrupt the entire production process. Depending on the shelf-life of the material and its features, it is important to know how long they can remain in storage, the conditions in which they have to be produced and much more. All of this requires exact planning and coordination along the entire production process. Unfortunately, planning is not easy due to several issues which we will look at below:
Mastering common challenges in chemical manufacturing
Demand variability
The demand for goods and materials can vary due to the economic climate in general, but also because of varying market trends and consumer behavior.
A very current example is that of PPE masks and respirators and the meltblown fabric used in their manufacture. Here, demand peaked when masks were mandatory in public places at the height of the Corona pandemic. Capacity for their production was built or extended in Europe and North America. Now that masks have been lifted, demand for such masks among the public has slumped and the meltblown market is overstocked.
The solution: A demand forecasting system which takes into account market trends as well as economic/political developments, consumer habits, etc. can considerably help a company plan for the resources that are required and meet demand far better.
Raw material availability
Nowadays, raw materials are not as freely available as they were a few decades ago. Environmental factors, supply chain disruptions as well as price fluctuations can all have a considerable impact on the availability of high quality raw materials which are necessary in chemical manufacturing.
The solution: By optimizing inventory and SCM a company can track raw materials availability and prices as well as identify supply chain disruptions. As a result, a company has an overview of the resources required in production and can schedule production and utilize capacity accordingly.
Complex workflows in production
Manufacturing in the chemical industry usually depends on batch production or continuous processes and involves raw materials or intermediates which have to be processed within certain time intervals because of their composition or features.
Production also involves several different workflows such as mixing, heating, cooling, etc. These procedures call for specific machinery and equipment as well as skilled personnel to operate them. Managing a plant’s production and personnel capacity is a highly complex matter. Production lines often run 24/7 and are divided into shifts. There is often the risk that important information is not properly documented or communicated during shift changes. This can lead to more serious problems at a later date.
The solution: Workflow complexity can be eliminated to a great extent if workflows and overall production processes are transparent. This enables planners to identify where bottlenecks occur, where there are inefficiencies. More automated procedures and digitized workflow documentation can greatly improve communication among workers, particularly during shift changeovers. This saves time and disruptions further down the production line.
Product mix and transition
In chemical manufacturing, different products and materials are processed on the same production line. Here it is important that product transitions are scheduled properly to avoid the risk of producing off-spec materials as well as having to invest valuable time and expense on clean-up jobs. As a result, the changeover process becomes longer and more complex.
The solution: Product transitions must be planned accurately with a product wheel which accurately schedules the manufacture of various product types in a high-mix manufacturing environment. E.g. when producing plastics, care should be taken that products of the same color type/field are manufactured one after the other, or detergents with the same chemical fluids. This not only leads to fewer off-specs and less time and costs spent on clean-up procedures in the production line. Changeover times can be reduced and throughput increased. In the end a company has a more predictable and stable production and, with the right scheduling, you have more bandwidth to manage rush orders.
Inventory
A lot of the chemical inventory for production consists of materials and fluids which are stored in tanks and silos. Knowing how much time is required for an operation or workflow as well as the volume of the material needed is a crucial factor. This allows you to manage your inventory and ensure that there is always enough space in the tank when replenishments come in or, at the other extreme, that there is no danger of them running dry. The inflow from one operation and the outflow of another determine when a tank is available. If this is not coordinated exactly then the production line is blocked and its capacity under-utilized. However, as demand varies, production schedules can be unpredictable , particularly when rush orders come in.
The solution: To ensure that tanks and silos are constantly at full capacity, not at risk of overflowing or running empty, upstream and downstream operations must be scheduled synchronously. As a result, production line capacity can be utilized optimally, even in the case of rush orders which need to be given priority.
More interesting articles
Meeting the challenges head-on with a data-driven approach!
Today, manual planning in the form of spreadsheets is no longer an adequate method to master challenges such as those mentioned above. What is needed are digital tools that can solve highly complex problems which have many conflicting goals and cross-dependencies. By taking a data-driven approach, a company can analyze and interpret its data to make far better strategic decisions on how to meet its short and long-term goals.
Like many other industries and business sectors, the chemical industry is data rich but information poor. Companies produce a mass of information and data in all areas of their business, be this in their supply chains, manufacturing, inventory or logistics. Precisely this data can be harnessed effectively to help them structure their operations and processes more efficiently – and this is where Advanced Analytics tools come in…
Optimal capacity – OPTANO can help!
A software platform such as OPTANO applies mathematical optimization to address complex relationships and find optimal solutions to any business problem.
By applying all of the relevant data, a company’s underlying processes can be analyzed to identify any influencing factors, cause-effect relationships and cross-dependencies. On this basis a mathematical model can be created which maps your business and its operations. With the help of sophisticated algorithms, millions and millions of possibilities can be calculated based on real data in order to find the optimal planning strategy with regard to a defined objective. Even better – the optimization can be geared towards several business objectives at the same time.
For example, a production schedule that has been created with OPTANO would find the best job sequence to minimize set-up and lead times simultaneously, ensure that machines run at full capacity and delivery dates can be met. If any changes need to be made at short notice, these can be made with just a few clicks, without the planning quality suffering as a result. Thanks to powerful procedures in the background such as Prescriptive Analytics, planners receive specific recommendations on how to implement their previously defined objectives– be this machine occupancy or combining orders.
OPTANO can also be applied to generate demand forecasts based on Predictive Analytics. With the help of machine learning procedures, relationships are identified and taken into account which would have gone undetected in manual planning. Data from external sources can also be integrated. If a link can be established between the development of specific raw materials prices and the demand for a product, then this factor in real-time can be integrated into the predictive model to forecast demand. The forecast is then integrated into the optimized production plan and can ensure that production volumes can be increased temporarily in order to meet the forecast higher demand within the forecast period. This increases machine utilization and has an effect on the market at the same time.
If you would like to learn more about how mathematical optimization works, then you can download our factsheet “Advanced Production Planning”.
Also, if you have a certain problem which you think OPTANO can help solve, then contact one of our consultants who are only too happy to answer any questions you may have. We look forward to hearing from you!
Have you got your copy of our factsheet on this topic yet?
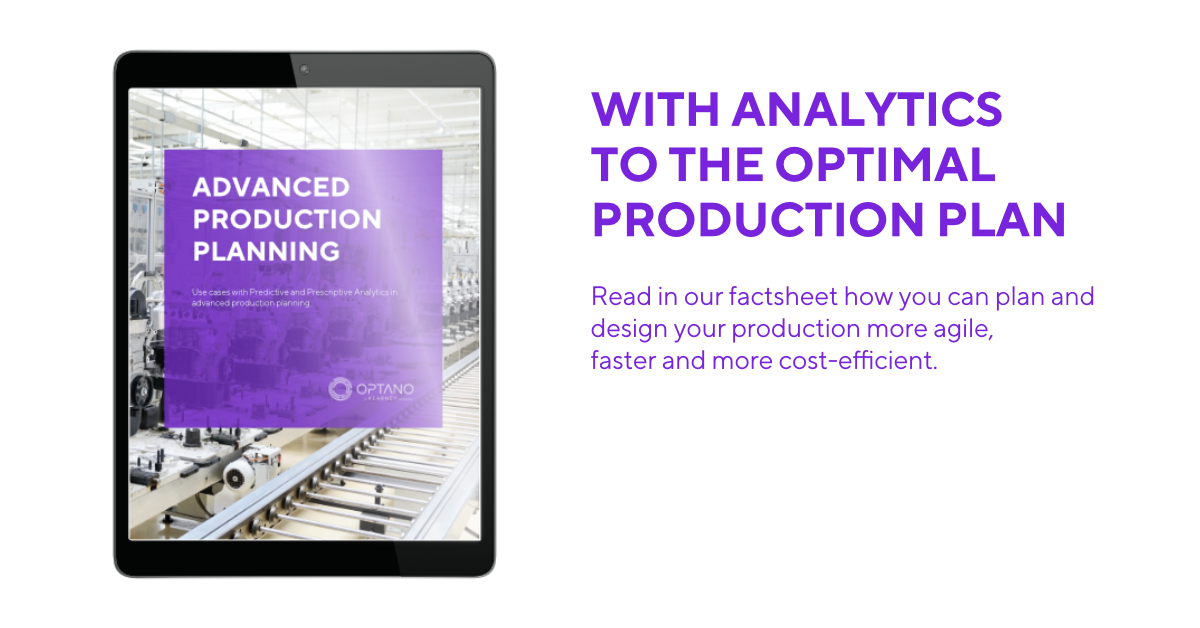
In our factsheet Advanced Production Planning we present some of the use cases of Predictive and Prescriptive Analytics in modern production planning which you can download here.
To obtain our factsheet, all you need to do is enter your contact details in the space below. A pop-up window will then open to download the whitepaper. Please note that by providing us with your email address, you agree that we may contact you on this topic. You may revoke this agreement at any time by contacting [email protected].