Transportation lead times in production network planning
“Better to have it and not need it than to need it and not have it” my father used to say. However, in the context of a manufacturing network, excess inventory can be costly. In this article, we explore how incorporating transportation lead times into tactical planning can help reduce the need for valuable storage space and optimize overall production efficiency.
Manufacturing network challenges
Consider a manufacturing network with plants or warehouses in different countries. Materials or intermediates often need to be sourced over long geographic distances. While this can provide cost savings by reducing the price of goods and intermediates compared to local sources, these advantages must outweigh the higher transportation expenses to be beneficial.
Warehousing in transit
Not all goods and resources required for production need to be stored in traditional warehouses; they can be stored in “mobile warehouses” during transportation, reducing storage costs. A good long-range capacity plan therefore takes into account the increased lead time for long transportation lead and delivery times without affecting production and service levels. An important building block on the road to lean manufacturing.
Of course, there is a downside to long transportation and delivery times. Unexpected delays can result in costly production downtime. Not only does this result in direct costs, but it also leads to a reduction in service levels, ultimately risking customer satisfaction.
Safety stock can be used to counteract this, but it results in higher inventory costs. The trick is to allocate resources based on a good demand forecast so that machines, raw materials, and personnel are available in sufficient quantities and at the right time to meet demand. The challenge is to maintain enough safety stock to keep production running without overstocking.
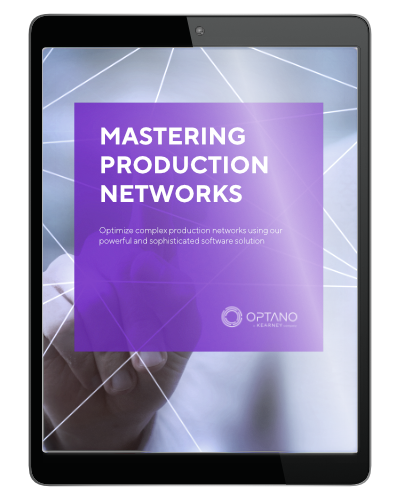
The limits of manual planning
The art of long-term capacity planning with transportation lead times is to balance the following factors:
Material and transportation costs
Material must be sourced in the right quality and at the right price, without transportation costs eating away at cost efficiencies. This can mean not only sourcing from long distances, but also sourcing using slow modes of transportation (e.g. sea freight).
Production reliability and service level
Production downtime is not only costly, it also damages customer relationships. Therefore, it is important to ensure smooth and efficient production and maintain service levels by planning for transportation times and downtime probabilities.
Inventory costs and safety stock
Storage costs can be reduced by using transportation as a “mobile warehouse”. This reduces the amount of space needed to store materials. Safety stock, which must be held in reserve to ensure continued production in the event of a transportation delay or failure, must be added.
Finding the right trade-off between all of these factors for an entire network is nearly unimaginable with manual planning. It becomes completely impossible when unexpected events require rapid re-planning.
Digital solutions to complex challenges
To meet this challenge, the most important step is to digitize your supply chain. The term “digital twin” is often used in this context. This is misleading in that a complete enterprise is never digitized, only the part that is needed to achieve the result. The trick is to find a level of abstraction that provides an optimal answer to the question without becoming overly complex and unnecessarily consuming computing time.
Once the digital replica is complete, the impact of decisions on the entire network can be simulated. For example, it can answer the question of what a delay in the delivery of a key component would mean in terms of costs and service levels. It can also calculate the impact of countermeasures. For example, what would happen if these components were flown in in a smaller batch instead of waiting for the delayed container ship to arrive?
In such a system, powerful algorithms allocate available production and transportation assets to maintain a defined level of capacity utilization and service at minimal cost – regardless of how the underlying conditions change. Using prescriptive analytics, OPTANO provides specific recommendations on how to achieve the defined goal. This is often referred to as digital decision support.
Mastering transportation lead times for maximum efficiency
Incorporating transportation lead times into production network planning is essential to optimizing efficiency and reducing costs. By leveraging digital solutions and advanced optimization software, companies can balance material and transportation costs, maintain production reliability, and minimize inventory costs. This approach not only promotes lean manufacturing practices, but also ensures that resources are allocated effectively to meet demand. Ultimately, finding the right balance between these factors is key to achieving a lean and resilient production network with high service levels.
So I have to correct my father a bit: It is not “Better to have it and not need it than to need it and not have it. – It is more like “Better to have exactly what you need when you need it.
Have you already got your factsheet on this topic?
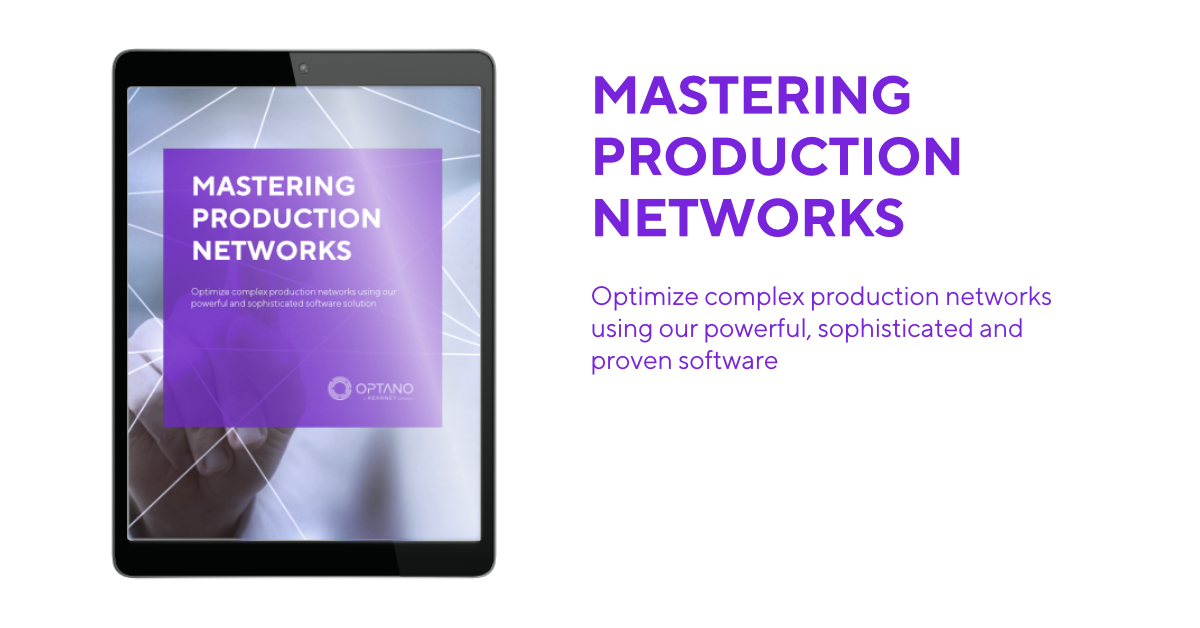
Managing complex production networks is challenging. There is often a lack of the necessary transparency to coordinate requirements and production capacities in such a way that the availability of goods and production costs are in an optimal relationship. In this factsheet, we show the possibilities offered by the OPTANO solution for production networks. In this factsheet we would like to share what we have learned over the course of numerous projects on how to successfully complete an optimization project.
To obtain our factsheet, all you need to do is enter your contact details in the space below. A pop-up window will then open to download the whitepaper. Please note that by providing us with your email address, you agree that we may contact you on this topic. You may revoke this agreement at any time by contacting [email protected].