For more ecology
in production
As a common saying goes: Everybody in their lifetime should have planted a tree, built a house and become a parent. Well then, I can give myself a satisfactory pat on the shoulder: I’ve managed all three. Or have I…? Because recently I read an article claiming that a family of four (that applies to my family), emits an average of 44 tons of CO2 each year. 44 tons! The one tree that I have planted is not going to be much help there. We are actually talking more about 88 trees – per year – which are needed to neutralize CO2 emissions. I don’t know about you, but it would be quite a tight fit if we planted that many in our garden.
And yet this little arithmetic exercise tells us that something has to be done. In today’s blog we present some examples of how to structure manufacturing processes so that they are more sustainable and demonstrate how mathematical optimization can help.
About markets and margins…
A few exceptions aside, a large majority of the manufacturing industry – especially in end consumer markets – is under immense competitive pressure. In many cases the markets are heavily saturated and, in connection with the prevailing competition, margins are melting like butter in the sun. It is clear, therefore, that procurement and maufacturing processes have been trimmed to achieve maximum cost efficiency over the years. But what is happening now? For an ever growing number of consumers the price is no longer the sole criteria when buying products. In a survey conducted by Capgemini in 2022, 79% of those surveyed claimed that that they were rethinking their buying habits in view of ecological aspects.
However, increased environmental awareness among consumers has a major snag for manufacturing companies: They are almost diametrically opposed to the prevailing requirements for efficiency. The fact that the legislator has also entered the fray with laws and regulations hasn’t made things any easier for businesses.
This is why we cannot afford to lose any time. Together we will take a look at several options which can be used to make production processes more sustainable.
Moving gradually towards more ecology in manufacturing
When demonstrating methods which can support sustainable production, they can be divided into two parts – into “passive” and “active” methods. The first deals with steps which can be integrated into current production processes and thus have a less invasive impact on the procedure already in place. When we talk of “active” alternatives, we mean strategies which result to some extent in additional investments. Now that we have explained this, we can move on directly to the issue in question.
Our production should be greener (passive methods)
A.) Increasing capacity
This point is evident and you will certainly have already done your utmost to utilize your machinery, employees and other resources as effectively as possible. However, be aware that each standstill not only costs money but also wastes resources from an environmental point of view. Every idle machine, every unused preliminary product was previously manufactured using a lot of energy and resources. Employees came to work that day – perhaps on public transport or by car. Increasing capacity in production not only has a postive effect on your ROI but also on the degree to which your resources are deployed ecologically.
B.) Increasing the utilization rate
This aspect concerns the question: How well are the resources exploited? To be more precise: How much surplus is in the material? One of OPTANO’s earlier projects dealt with the problem of how to minimize the offcut from wooden planks in a wood processing company. Although the company had a lot of experience in cutting the parts required as efficiently as possible, the mathematical method could still ensure a further gain in efficiency. Avoiding scrap also pays off on this same issue. The earlier a company can identify a potentially defective product in its production process, the less operational resources are wasted on its production.
C.) Increasing transport efficiency
It may sound hard to imagine but empty runs make up approx 60% of the transport effected in Germany – in other words, they do not carry any freight. Of course this is even more of an issue if a company has its own fleet of trucks. But even if this isn’t the case, there are still a lot of measures you can take to improve transport efficiency: How often are deliveries made, which materials are dispatched directly to the company and which via regional forwarders, etc? The fewer kilometers a truck has to drive and the fewer routes it travels, the better this is for the ecological balance.
We must actively improve our CO2 balance (active methods)
A.) Ecological resource management
The question of the resources to be deployed is a complex one. In addition to the necessary properties of a resource, it is also a matter of considering its origin, manufacture, transport and ultimately its disposal. Is the raw material produced and processed sustainably? Are there suppliers closer to home who meet these same requirements? Can the raw material be disposed of in an environmentally friendly manner? And on top of all that, it is vital not to lose sight of the costs. All of these are questions that the purchasing department has to deal with. In addition, when substituting a raw material, the production may need to be reorganized and employees trained – if necessary other machines may even be required. Such a step has to be well thought out and requires a great deal of planning and time in advance.
B.) Switching to sustainable energy
When it comes to energy supply it is possible, in theory, to switch to ecologically generated energy fairly quickly. Alongside the additional costs, guaranteeing supply is an important factor – after all, the business must continue to run. However, this raises a further question here: Do we want to buy our energy on the market or do we want to generate it ourselves? Under the circumstances this would even have positive aspects. Not only that such a step would have a positive effect on the company’s image but it could also be worthwhile financially with regard to grants and subsidies.
C.) Active ecological balance
We only need to look at LinkedIn to see that more and more companies are investing the equivalent of their yearly CO2 emissions in reforestation projects. Many are planting proper company forests and actively involving their employees in planting and maintaining them. Alternatively there are many associations and institutions to which trees can be donated for reforestation projects. This has an element of charm to it and it is not only your marketing team that will thank you for it.
With these “passive” and “active” methods, companies can make a valuable contribution to more ecological production. There are certainly many more options but here we would like to take a look at how mathematical optimization can help to implement the possibilities we have described.
More interesting articles
Mathematics, it’s your turn
You may have already guessed it but mathematical optimization can be very useful in many of the cases we have described above. Not only can you structure your processes more efficently but you can also create forecasts or simulate various scenarios, on the basis of which you can make strategic decisions. We would like to demonstrate the most important use cases below:
A.) Multi-goal optimization
Mathematical optimization allows you to optimize structures and processes on the basis of a pre-defined goal. For example you could specify the goals “minimum costs” or “maximum delivery reliability”. Based on real company data, the algorithm will calculate the optimal production sequence for you and actively advise on its implementation. The beauty of this: it can be optimized not only for one goal, but for several and in principle, these can even be conflicting ones.
In our example it would therefore be possible to meet economic as well as ecological goals in an optimization. One possibility would be, for instance, to attach a price to the CO2 emissions of different work stages. The more “environmentally harmful” one possible procedure would be, the “more expensive” it would be, too. This means that an algorithm which is oriented towards cost efficiency would then prefer the more “environmentally friendly” option. Of course, the environmental aspect would be only one of many that contributes to the optimization result but you can certainly assume that an optimum which has been calculated in this way would be more environmentally sustainable than one in which CO2 costs were not considered. This is particularly practical for companies which already apply mathematical optimization since the algorithm need not be changed.
Another possibility is to conduct two optimization runs. If we put the ecological aspect first, a first optimization run would come up with the most environmentally friendly version. This optimal CO2 value from an ecological viewpoint would then represent the target for a further, economic optimization. The cost-optimal version would then be identified from among the environmentally friendly versions. Of course this would also work in reverse (the most environmentally friendly of the cost-optimal versions).
B.) Forecasting with Predictive Analytics
Predictive Analytics calculates how likely it is that certain events will happen based on historic data but also on external influencing factors. This can be extremely useful; for instance to predict demand fluctuations. However, it can also be highly beneficial when deployed in production processes.
One example is the early identification of rejects. Based on an analysis of rejects and the associated production data, indicators can be identified which can, with a certain likelihood, lead to the reject of a production part in a later production process. This means that a metal part which has not cooled down sufficiently in production step A, can already be removed since there is a high probability that this circumstance would lead to an error in production step D. This would be more favorable in terms of a high utilization rate than if the part had gone through steps B and C before it had to be rejected.
Machine failures can also be predicted according to a similar principle. Based on Predictive Analytics, maintenance intervals can be selected so that the number of machine failures are minimized without resulting in any unnecessary standstills. This method can also help to increase the utilization rate in the production process.
C.) Optimal procedures thanks to Prescriptive Analytics
Prescriptive Analytics answers the question: “How can I make something possible?” Not only does it calculate optimal states but it also provides sound recommendations on how to attain this state such as splitting orders across different machines or changing the job sequence to achieve mimimum set-up times.
This last example in particular demonstrates how Prescriptive Analytics can be dpeloyed in production planning. While splitting orders reduces the production time (goal: increasing delivery reliability), the minimization of the set-up times increases the throughput time and ultimately the efficiency. The great thing about this is that plans remain in optimal alignment with the goal, even if plans have to be repeatedly changed at short notice (e.g. because of an urgent priority order). New plans can literally by made at the touch of a button and still contribute to the previously defined goal.
The same applies to the optimal use of resources. The example of minimizing offcut in the wood processing company clearly demonstrates that the mathematical process has the edge over a lot of experience. A further good example is the lacquering line at a car manufacturer. Here, the sequence of the colors plays a crucial role. If, for example, a batch of light colored paint comes after a dark one, the spray nozzles will have to be cleaned far more thoroughly. This is not only time-consuming but also consumes significantly more water for cleaning. As well as that there is a risk of rejects.
Another classic case in mathematical optimization processes is route planning. Depending on which resources are required in production and when, the system calculates different delivery profiles: a direct route, milk-run or regional forwarder. Here the capacities of the goods-in and goods-out departments as well as the warehouse capacities and cost reqirements are also considered. A further aspect here is the reduction of empty runs, insofar as your company disposes of its own fleet of trucks.
D.) A look into the future with what-if scenarios
When it comes to making strategic decisions, the most powerful instrument is quite evidently what-if scenarios. If the mathematical model and all data sources have been connected successfully, various scenarios can be simulated and their impact on various areas can be assessed, taking all of the cross-dependencies into consideration.
By looking at the previous examples, we could assess the impact of switching to a different material or supplier. Also the question of what would happen if we purchased sustainable energy and whether it would be worth generating this ourselves can also be simulated precisely. But this is also an invaluable tool with regard to logistics. For example, what would happen if we built an additional warehouse? What if one section of local or urban transport was replaced by more sustainable forms? All of these questions can be asessed with what-if scenarios – broken down to all your KPIs.
The forest in the garden
As you can see there are many ways to organize your production processes more sustainably. Mathematical optimization can contribute greatly towards making production structures and processes better and more environmentally friendly. This applies to both the described “passive” and “active” methods. Whether it is based on legislation, the change in the buying behavior of consumers or the intrisical motivation of businesses: The production process of the future will have to change. So let us make a start! Maybe by planting a tree in the garden?
Do you already know our factsheet on this topic?
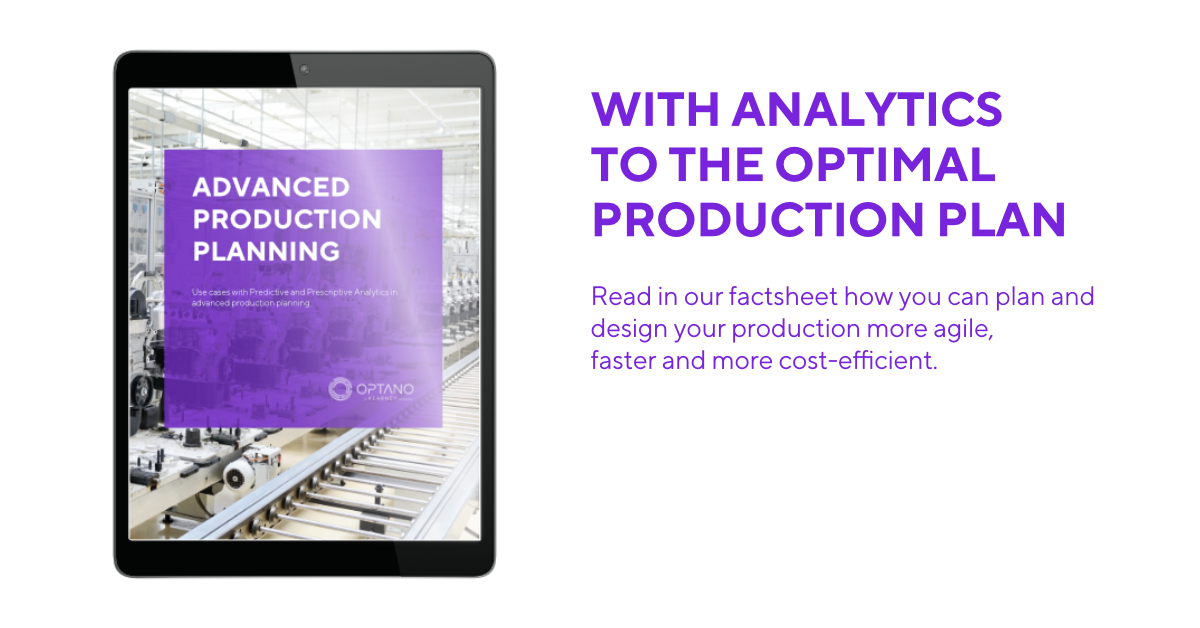
In our factsheet Advanced Production Planning we present some of the use cases of Predictive and Prescriptive Analytics in modern production planning which you can download here.
To obtain our factsheet, all you need to do is enter your contact details in the space below. A pop-up window will then open to download the whitepaper. Please note that by providing us with your email address, you agree that we may contact you on this topic. You may revoke this agreement at any time by contacting [email protected].