Optimized production planning in the medical technology industry
It is no secret that the world’s population is growing. But that’s not all: our population is also aging, especially in industrialized countries. For example, a third of Germany’s population alone will be over the age of 60 by 2050. At present, life expectancy is 78 years for men, and 83 for women. This is due to improved healthcare systems and the ability to cure infection and diseases more effectively. Even so, the older we become, the more we require treatment and specific medical devices, from lenses and hearing aids to heart pacemakers, catheters, joint replacements, etc.
Consequently, the medical technology industry is one of the fastest-growing sectors, particularly in Europe, North America and Japan. Yet keeping pace with the demand in such a competitive industry is no easy task. When it comes to manufacturing medical devices, the industry has to surmount several hurdles. In this blog, we look at production planning and scheduling issues within the medtech industry and potential solutions to the problems.
The medtech industry: a brief overview
The medical technology industry—often referred to as medtech—comprises companies that develop, manufacture, and distribute technological devices, equipment and diagnostic tests to provide effective healthcare treatment. The large majority of the companies in the industry are SMEs with fewer than 1000 employees. Competition in the market is high, and prices have generally been low as a result. However, the demand for medical devices has been growing due to the aging population and the pertaining medical treatment and, far more recently, because of the pandemic. The costs for quality healthcare are exploding and the medtech industry is under pressure to keep its product costs low. This is particularly challenging since production costs are increasingly higher.
The medtech industry has ailments of its own
Accurate and flexible production planning is necessary to meet the demand for the medtech industry’s products and still keep costs at a minimum. However, production planners in the industry are confronted with a myriad of challenges, some of which include:
Supply chain disruptions
Like many other industries, the medtech industry has felt the full blow of supply chain disruptions over the past few years. These are attributed to the pandemic, the war in the Ukraine and the global shortage of raw materials. The pandemic revealed the lack of transparency and failings within the supply chains of medtech companies. Lean manufacturing methods and the tendency to rely too heavily on just one or two suppliers in one region (i.e. in Asia), led to delays in delivery and rising prices. This is particularly critical during a pandemic when healthcare systems urgently require the products the medtech industry manufactures.
Shorter product life cycles
As already stated above, the medtech industry is a highly competitive playing field. A company’s survival depends on being one of the first to get the best product into the market while already working on the next one. Innovation is being driven forward by advances in technology. For this reason, a product life cycle from the prototype to the finished product can range from merely a few weeks to a few years. Companies are thus under pressure to provide the market with the most innovative devices within as short a time as possible. At the same time, they have to ensure that their products comply with stringent quality regulations. This brings us to the next major challenge, namely…
Regulatory complications
It may be one of the most innovative industries but at the same time, the medtech industry is, also the most highly regulated one. Stringent guidelines have been stipulated by governments and authorities to ensure that each and every product complies with quality requirements. In the EU, for example, the recently enforced Medical Device Regulation (MDR) calls for the strict certification of all new products as well as the recertification of existing ones.
A further headache is that there are no blanket requirements. Countries have their own quality regulations and it is essential to be aware of which guideline applies where. Failure to meet quality requirements can lead to costly product recalls, never mind a loss of reputation in the market.
Many of the manufacturing processes in the medtech industry involve very complex operations such as kitting, sterilizing, or decontaminating which are often outsourced to separate facilities. Unfortunately, discrepancies are often only detected much later in the manufacturing process which leads to rework and delays that companies cannot afford to have.
Uncertain approval dates
Every medical device must be approved before it can be launched into the market. The approval process can be lengthy. This makes it difficult to plan production and inventory, particularly when it comes to phasing out existing products and phasing in replacement ones.
If a company halts production of the existing product too early, then it will lose profit. If it stops production too late, it will incur obsolescence costs. On the other hand, if a company starts production of the replacement too early, it will incur inventory carrying costs. If it starts too late, then it loses revenue.
Transition plans must therefore be in place to ensure that there is enough of the existing product until the latest approval date while still having the replacement product ready for market by the earliest approval date, a fine balancing act.
Different manufacturing processes for different parts and materials
Diverse materials are used to manufacture the different parts required for a single medical product. Such materials can be metals, plastics, glass, electronic chips and many more. These do not run on all machines so it is vital that each manufacturing process is matched with the right workstation and machine. The machines themselves will also vary. Some may be operator-dependent, while others require little operator dependency. There will be varying life cycles, set-up, changeover and load times.
In some cases it is best to schedule production based on set-up and load times in order to stagger operations and minimize downtime. On others, it makes more sense to schedule operations based on the size of the order and inventory. Therefore, a facility should ensure that its production planning and scheduling unites all of these aspects into an efficient timeline which takes all factors into account to optimize workflows, minimize downtime and costs, and ultimately improve productivity.
More interesting articles
Advanced technology for optimal production planning and scheduling
By having advanced production planning and scheduling systems, it becomes easier to identify issues like the ones above and make timely interventions to prevent them from spiraling out of control.
Applying analytical methods such as mathematical optimization is especially recommended when it comes to complex procedures such as production planning and scheduling in the medtech industry. Production plans can be created based on a mathematical model which maps the entire production process – taking into consideration all objectives, resources, variables and constraints. Special solvers are used to help come up with the optimal solutions to the production problem.
OPTANO Production for more accuracy and flexibility in production planning
By implementing and managing your production planning and scheduling with OPTANO Production, which applies mathematical optimization and Advanced Analytics procedures, planners can create accurate, flexible schedules to adapt to changing demand and other variables. The key benefits of OPTANO Production are:
Demand forecasts
With OPTANO Production you can identify demand patterns and trends and use them to forecast demand by applying and evaluating relevant supply chain data using Predictive Analytics. Data from external sources can also be integrated to detect links. For example, how will the availability of raw materials affect prices? Based on these forecasts, you can manage your inventory and make contingency planning to prevent stockouts or overages
Job scheduling
OPTANO Production finds the best job sequence so that different manufacturing processes are properly coordinated to minimize set-up, changeover and lead times simultaneously and ensure that machines run at full capacity. Delivery dates as well as earliest and latest approval dates are also considered to ensure that delivery reliability is met and phasing-in and phasing-out products can be planned with confidence.
Agile response
Respond flexibly to unexpected disruptions such as sudden downtime, delivery failures, extended approval processes, etc with OPTANO Production. If any changes need to be made at short notice, these can be made with just a few clicks, without the planning quality suffering as a result. You can create new production plans in an instant. An alternative plan is calculated based on the new parameters within a very short time which still lets you achieve the optimum– no matter how often you have to reschedule.
Optimal decision-making
OPTANO Production applies mathematical optimization as a powerful Prescriptive Analytics procedure so that planners receive specific recommendations on how to implement their previously defined objectives in production planning. Different situations can be analyzed in what-if scenarios in order to make informed decisions on the best way to manage supply chains, optimize and coordinate manufacturing processes and generate the best transition plan for phasing out products and phasing in replacements successfully. In this way, medtech companies can maximize production, minimize costs and still ensure they maintain a competitive foothold in their market.
Whether it is tactical or operational planning, with OPTANO production plans can be generated quickly and easily in line with your requirements. Do you want to learn more? Then why wait? Contact us today! Our consultants are at hand to answer any questions you may have. And if you would like to learn more about how mathematical optimization can benefit your production planning, you can download our factsheet: “Advanced Production Planning”.
An innovative industry needs innovative solutions
Thanks to its devices and diagnostics, the medical technology industry saves lives and contributes enormously to sustainable healthcare. As a driver of innovation and economic growth, it needs advanced technology, like mathematical optimization, to provide innovative solutions to the challenges it faces, ensuring that its products reach those who need it most, safely and promptly.
Have you already got your factsheet on this topic yet?
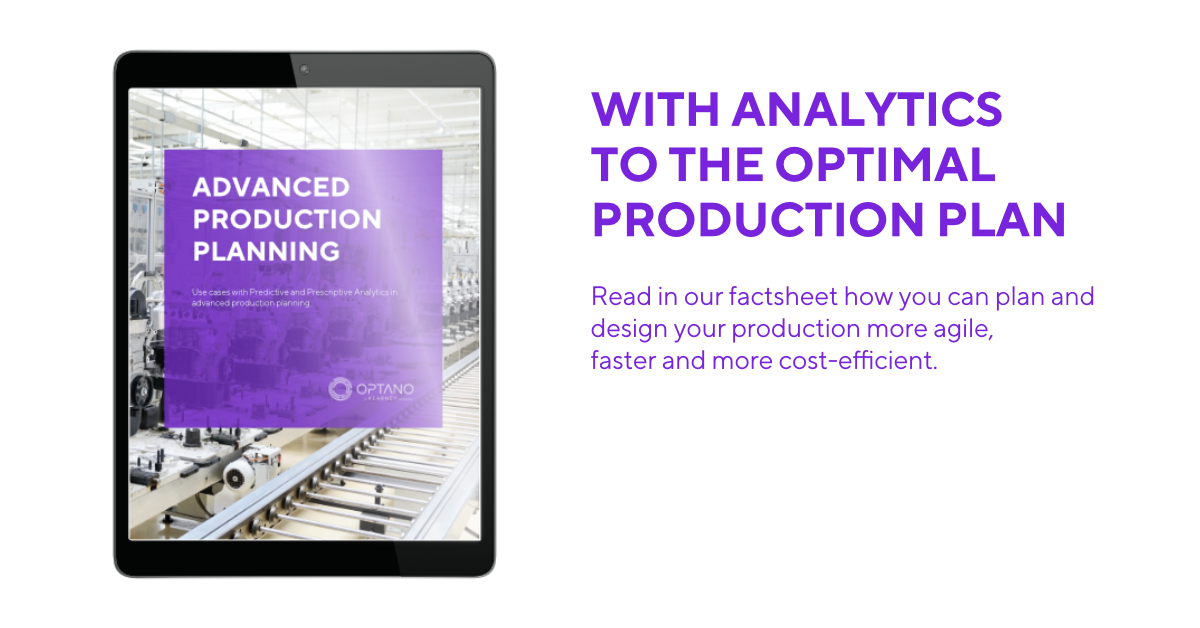
In our factsheet Advanced Production Planning we present some of the use cases of Predictive and Prescriptive Analytics in modern production planning which you can download here.
To obtain our factsheet, all you need to do is enter your contact details in the space below. A pop-up window will then open to download the whitepaper. Please note that by providing us with your email address, you agree that we may contact you on this topic. You may revoke this agreement at any time by contacting [email protected].