Making optimal
use of energy
in industry
Ever since the beginning of time, man has found inventive ways to stay warm or cool and use water resources to survive and progress. Did you know, for example, that the Romans were the first to use central heating by using a furnace to create hot air that went along channels under the floor to generate heat? In order to cool their homes they would attempt to circulate cold water from the aqueducts through the channels in the house walls. We have come a long way since the Romans’ innovations. Particularly in the last century, we have developed modern heating, refrigeration and water management techniques which are not only essential for our homes: industries rely on these in manufacturing. However, in an era in which we are becoming more environmentally aware and striving to battle climate change, it is vital that industry manages its consumption of energy efficiently.
In this article, we focus on how industries can optimally use process heating and cooling as well as water, not only for their own benefit, but also for that of the environment.
Why are heat, refrigeration and water so important in industry?
In order to understand the significance of heat, refrigeration and water, it is worth taking a look at how they are deployed in industry:
- Heating: Process heat is required in the chemical, iron and steel industries and is also used for the production of cement, glass and ceramics, among others. All of these sectors have jobs in production such as drying, smelting, forging, welding, etc. which all generate vast amounts of heat. More than 60% of Germany’s industrial energy demand alone is used for process heating.
- Refrigeration: Process cooling is applied to remove unwanted heat from an industrial process for it to continue safely and efficiently. It is crucial in the food processing industry to cool food and beverages, or during processes such as the fermentation of beer. The pharmaceutical/medical industry needs it to ensure constant low temperature storage conditions for medical supplies. It is applied in industrial manufacturing to cool machines after they have been running at high temperatures, or to cool certain products, for instance plastics during molding processes. Cooling towers, various industrial chillers and air-conditioning are typically used for cooling processes.
- Water: Industry is a primary water consumer. In fact, it accounts for 40% of the total global water consumption. Textile manufacturing, paper mills, oil and gas and food processing industries among others depend on water for their production. It is required at every step of production which can include jobs such as fabricating, diluting, washing, and of course it is also used in cooling and heating. Not only that, waste water must be managed very carefully to avoid pollution/decontamination.
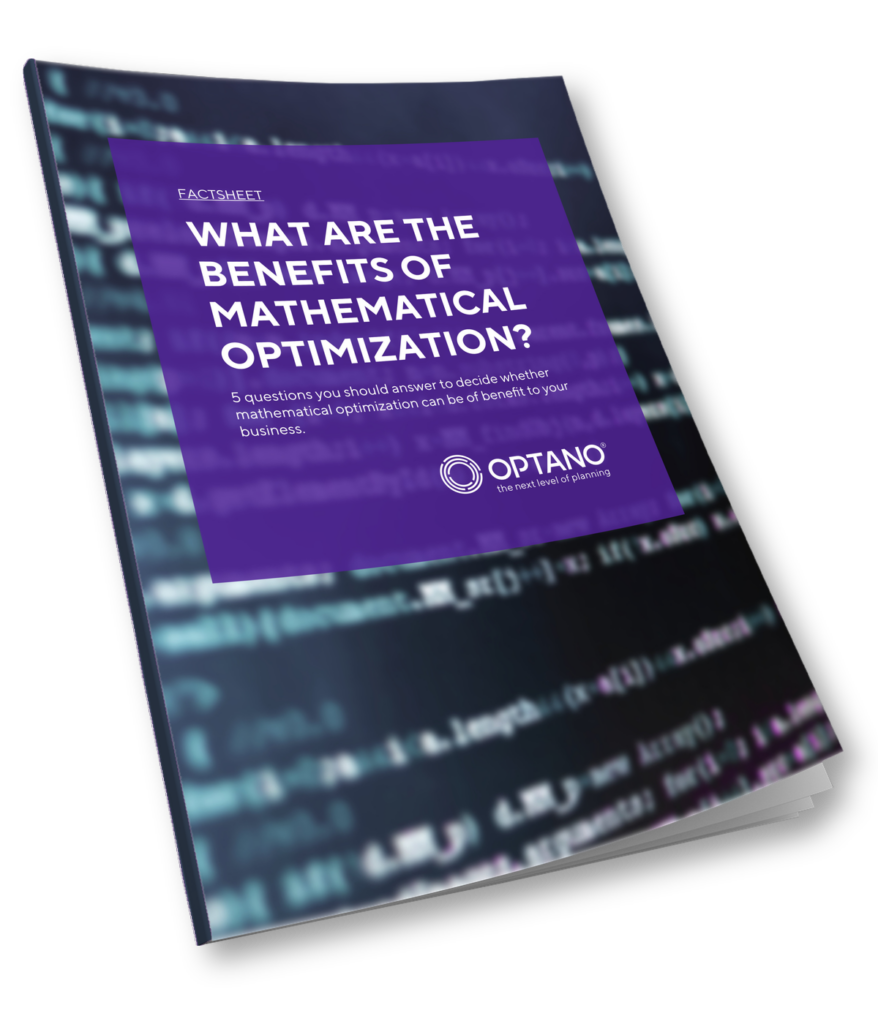
Are you interested in our factsheet?
What are the benefits of mathematical optimization?
The above jobs and processes are crucial elements in the production infrastructure, yet the major problem is that excessive use of heat, refrigeration and water has a negative environmental impact. High levels of process heating and cooling emit vast amounts of CO2 into the atmosphere. Since water stress is projected to increase and spread to more regions by 2050, industry is also being called upon to limit its water footprint. With the introduction of legislation requiring industries to implement more sustainable, climate-neutral manufacturing methods and achieve prescribed sustainability goals, companies are facing immense challenges. To make matters worse, the current energy crisis, which has led to even higher costs for the consumption of fossil fuels and electricity, has meant that many businesses are struggling to maintain efficiency as well as meet environmental and economic targets all at the same time.
Reduce energy consumption, but how?
We are all aware that if every individual and business, i.e. industry, were to reduce the levels of energy we consume, this would significantly slow down global warming and provide environmental and economic benefits. By gradually phasing out conventional energy sources, switching to renewable energy and implementing more efficient, climate-neutral production processes, industries can considerably reduce their carbon footprint and increase efficiency overall. When it comes to heating, cooling and water use, businesses are already implementing solutions:
- Heating: Industrial heat makes up two-thirds of industrial energy demand and almost one-fifth of global energy consumption. Industries mainly rely on fossil fuels for heating. Over 70% of industrial heat is generated by coal, oil and gas. To meet more ambitious climate goals, switching to new heating alternatives such as solar thermal power and geothermic and bioenergy are necessary. While these offer huge future potential, they still cannot be deployed in all industrial facilities, and can only generate heat up to a certain temperature. Furthermore, they are volatile methods, heat can only be generated at certain times of the day, for example. Electrifying heat generation, e.g. with a heat pump, is also possible, but only for processes at low to medium temperatures.
Yet reducing industrial heat demand is still possible by taking operational measures. Primary heat demand can be reduced by optimizing processes to prevent heat loss (e.g. with improved insulation and heat recovery). “Unavoidable” waste heat can be reused for preheating processes, to heat premises and water, and can be made available to external parties (i.e. by feeding it into local heating networks). - Refrigeration: Industrial cooling is responsible for 10-15% of all greenhouse gas emissions. For many years, industry relied on synthetic refrigerants like CFCs, HCFCs and HFCs, which were classed as big climate killers and subsequently prohibited. Today, the market offers a huge range of more efficient, state-of-the-art industrial chillers (e.g. fluid chillers) with natural refrigerants such as air and water, which can greatly minimize environmental impacts. However, the ROI has to be calculated in advance. Further measures include proper maintenance and operational improvements (having timed defrost cycles, automatic doors, ensuring seals are maintained, etc.) which can also contribute greatly towards lower energy consumption in cooling processes.
- Water: Efficient water use can provide both environmental as well as economic gains. It naturally leads to less water pollution, hence improved quality of water, and protects freshwater resources. Lower water consumption also means saving costs on electricity, gas, chemicals and wastewater disposal.
Reducing water consumption can be achieved in many simple ways in industry. For example, routine maintenance can help to identify any leaks in pipes which can waste gallons of water. Components and equipment can be replaced by alternatives which make more efficient use of water, e.g. hoses and sprays with shut-off nozzles to control the water flow. Finally, should water discharge be reused wherever possible. This could be the rinse water from cleaning, condensation from boilers, refrigerator defrost, etc.
More interesting articles
Climate-neutral production requires foresighted planning
However, the key levers on the way to a climate-neutral production infrastructure are in the planning phase. This is where decisions about system topology are made, or where technology selection and usage control strategies are taken into account. When we consider each of the above areas individually, the solutions to reduce heating, cooling and water consumption appear fairly straightforward. However, when we view all three factors as one issue, things become far more complex. The constraints and objectives of all three conflict with one another, decisions taken in one area have direct and indirect effects on the other, be these positive or negative. In addition, other business and production targets must be taken into account: cost efficiency, minimum throughput and setup times, machine utilization, etc. This makes planning extremely complicated, particularly if companies still deploy manual planning methods such as spreadsheets.
Advanced analytics can play a significant supportive role here. It focuses on model-based approaches using dynamic simulation and mathematical optimization which can support the evaluation of techno-economic and ecological criteria in the planning of new and existing production infrastructure systems.
To achieve this, tracking data on heating, cooling and water consumption is essential. This should include relevant technical and economic data such as temperatures, makeup rates, flow rates, pressure drop, evaporative losses, operating and manufacturing practices, when process heating and cooling takes place, how much heat is reused, for what purpose is water used and many more besides. The data is then captured, managed and analyzed in a software planning application.
OPTANO and mathematical optimization to support climate-neutral production
OPTANO applies mathematical optimization to map all the constraints and goals in your business, helping you to identify trends and processes and build models related to energy usage. This enables you to make sense of your data and calibrate processes far better, allowing you to compare and evaluate the results based on your defined energy and economic goals and make proactive decisions. Would it make sense to switch to alternative heating methods like solar thermal energy? Should we replace cooling towers with fluid chillers? What planning changes would arise as a result? What costs would this incur? This helps you make optimal use of your energy resources, increase efficiency in production and reduce operational costs.
Planning software like OPTANO can find the best solution to even the most complex problem, not just in terms of energy but also for your network, supply chain or production planning. It supports you with targeted recommendations on the best action to take – based on the proven analysis of all the data that is taken into account.
OPTANO provides you with the overview you need – feel free to talk to us! Our consultants are happy to answer any of your questions. Alternately, send us a mail and we will get back to you.
Time to make optimal use of our technical advances
It is certainly true that we have made major technical advances over the centuries. However, we have also created many ecological problems along the way. Now, it is down to us to leverage the technology we have invented to solve the problems we have created. Mathematical optimization is a good starting point.
Have you got your copy of our factsheet on this topic yet?
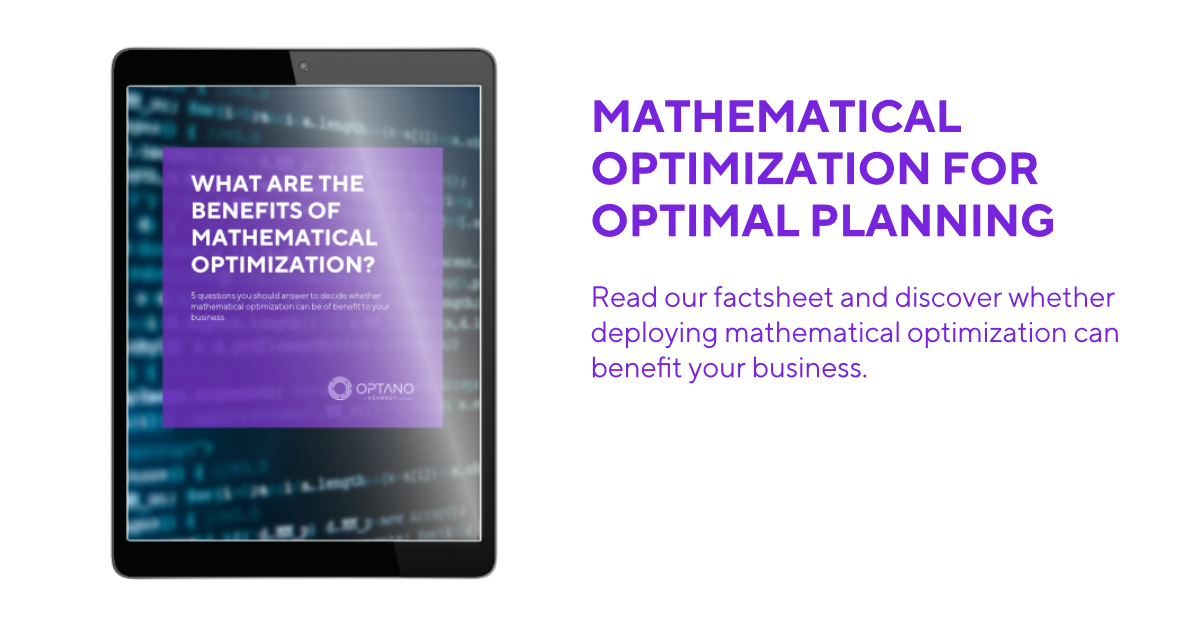
In our factsheet “What are the benefits of mathematical optimization?” we ask 5 questions to help you assess whether mathematical optimization brings benefits to your organization.
To obtain our factsheet, all you need to do is enter your contact details in the space below. A pop-up window will then open to download the whitepaper. Please note that by providing us with your email address, you agree that we may contact you on this topic. You may revoke this agreement at any time by contacting [email protected].