Efficient and safe operations with optimal stock levels
The solution for optimal stock levels
Inventories are a central component of many companies. In addition, efficient inventory management can have a significant impact on a company’s financial stability. Using mathematical optimization to calculate inventory levels offers a variety of benefits. By taking into account different variables such as demand forecasts, delivery times, storage costs and order quantities, companies can optimize their inventory levels while improving service levels, reducing storage costs and increasing efficiency. Compared to manual calculations, mathematical optimization enables precise and data-based decision making that helps minimize bottlenecks, reduce overstocking and ultimately increase the company’s profitability and competitiveness.
With OPTANO Inventory Management you can benefit from all these advantages. OPTANO uses mathematical decision support to calculate the optimal inventory levels. This can release unused potential and reduce your costs in the long term. Interested? Get in touch with us!
Lagerbestände sind für viele Firmen entscheidend und beeinflussen ihre finanzielle Stabilität stark. Der Einsatz mathematischer Optimierung bei der Berechnung von Lagerbeständen bringt zahlreiche Vorteile, z.B. optimierte Lagerbestände, verbesserte Servicelevel und gesenkte Lagerkosten. Durch präzise Entscheidungsfindung lassen sich Engpässe minimieren und die Rentabilität steigern. Nutzen Sie unsere Lösung für optimale Inventarbestände! Kontaktieren Sie uns für weitere Informationen!
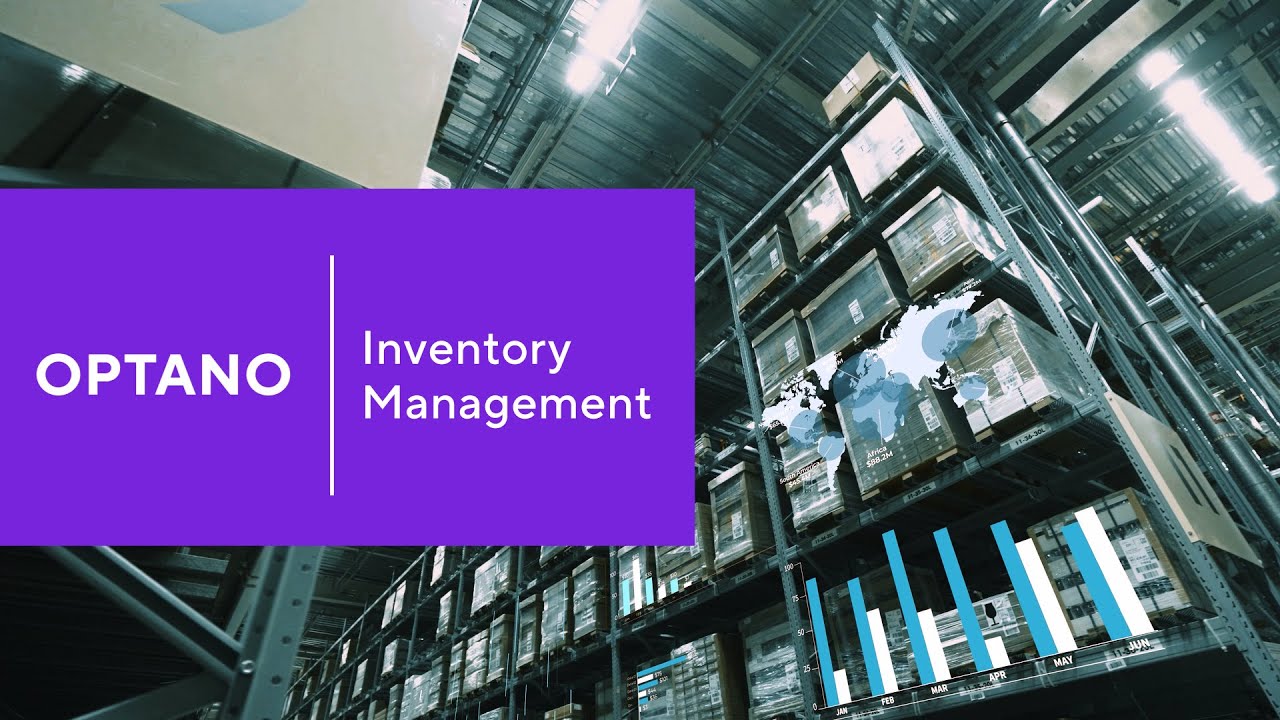
Mit dem Laden des Videos akzeptieren Sie die Datenschutzerklärung von YouTube.
Mehr erfahren
The OPTANO solution
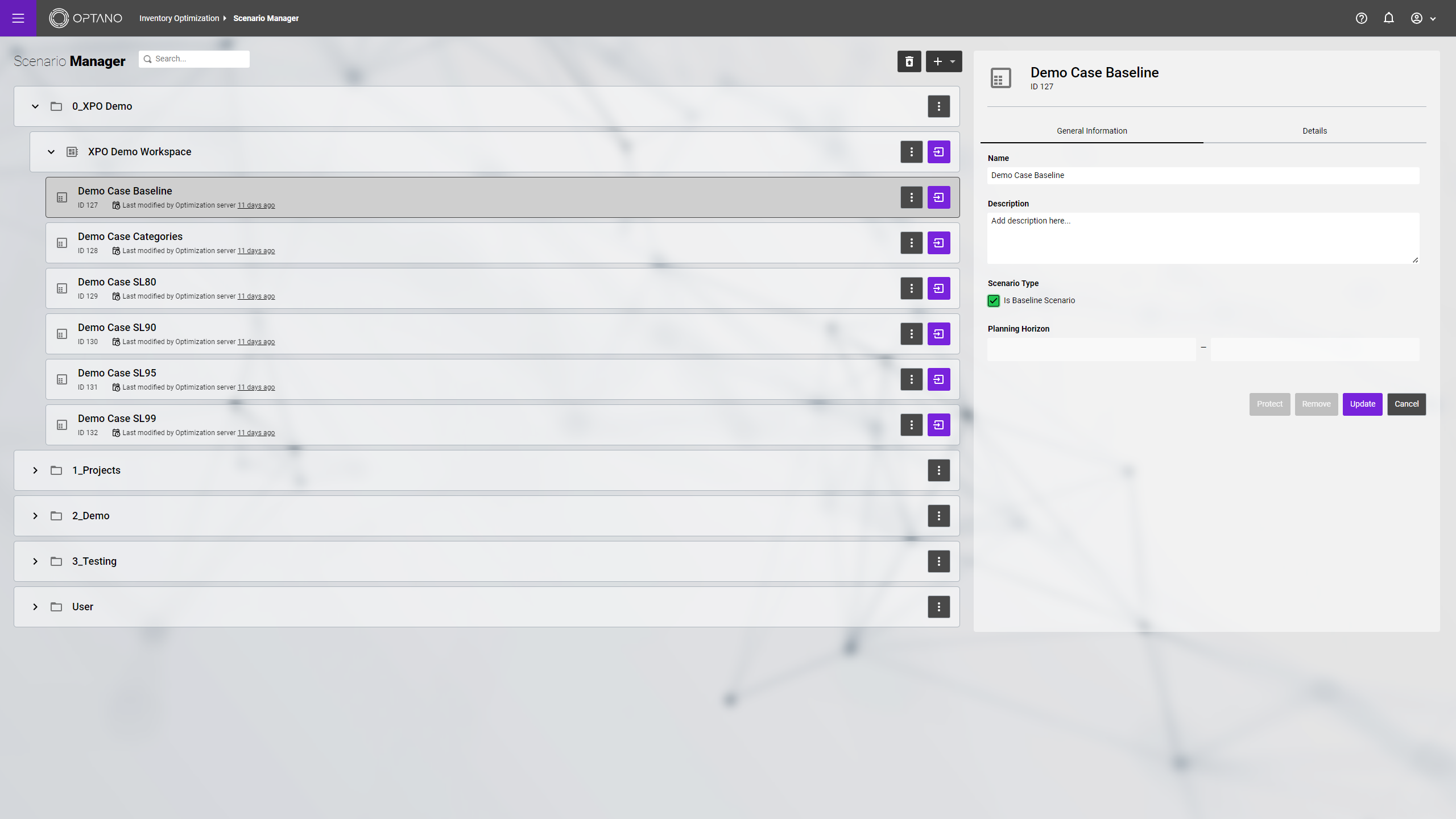
Examples of input data

Unplanned events can affect planned requirements and potentially lead to major profit losses. To minimize these risks, adequate safety stocks are essential. But what exactly are “adequate” safety stocks?OPTANO Inventory Management allows users to select distribution functions for deviations in requirements or delivery times. Based on these functions, the application calculates an adequate safety stock level to reduce losses.
Factors for safety stocks
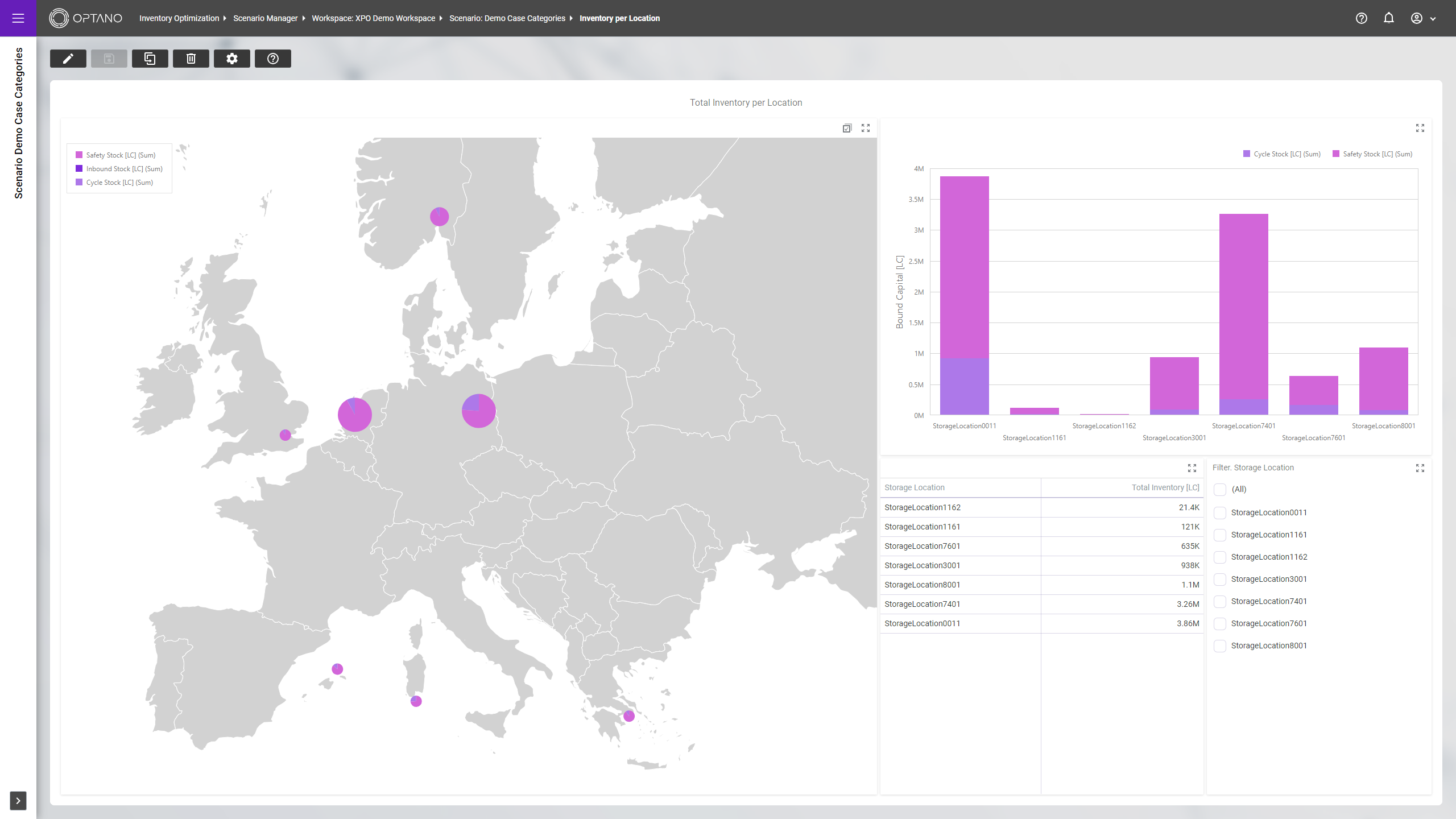
In addition to the probability of uncertainty, the safety stock is also largely determined by the risk period, which must be covered by the safety stock. OPTANO Inventory Management therefore offers users the option of selecting an order policy.
Periodic review: The stock level is checked in regular, non-variable time periods and the difference to the target stock level is reordered. With this order policy, the risk period extends to the length of the review period plus the length of the order period.
Continuous review: Instead of fixed time periods, actual stock levels are reviewed continuously. As soon as the stock level falls below a threshold value, an order for a defined quantity is triggered. In this order policy, the risk period only extends to the delivery time.
Factors for safety stocks
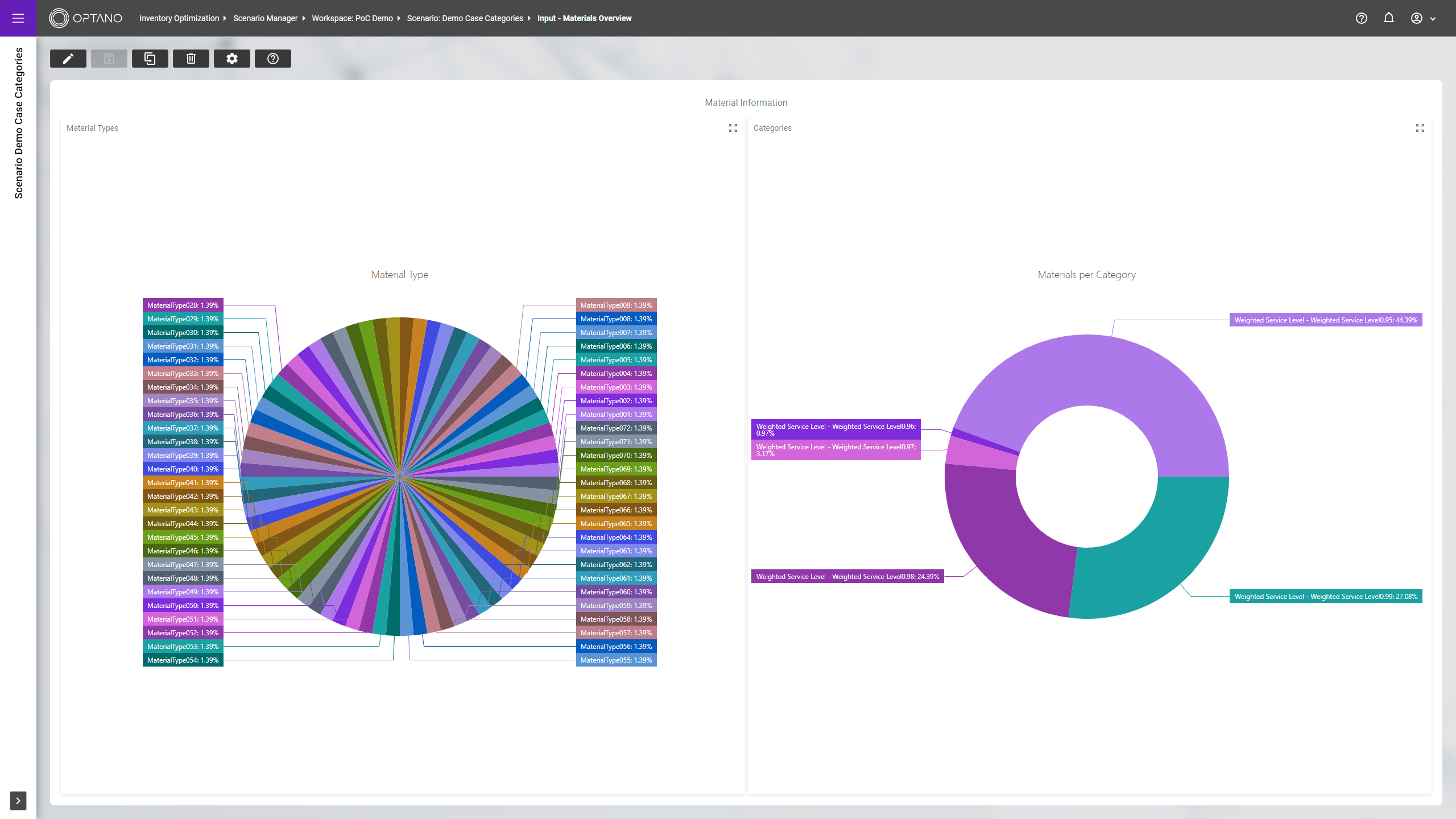
OPTANO Inventory Management offers the option of entering material categorizations. A multi-level categorization is possible, which allows users to create the desired service level for optimization not only globally but also differentiated for different categories.
Examples for categories
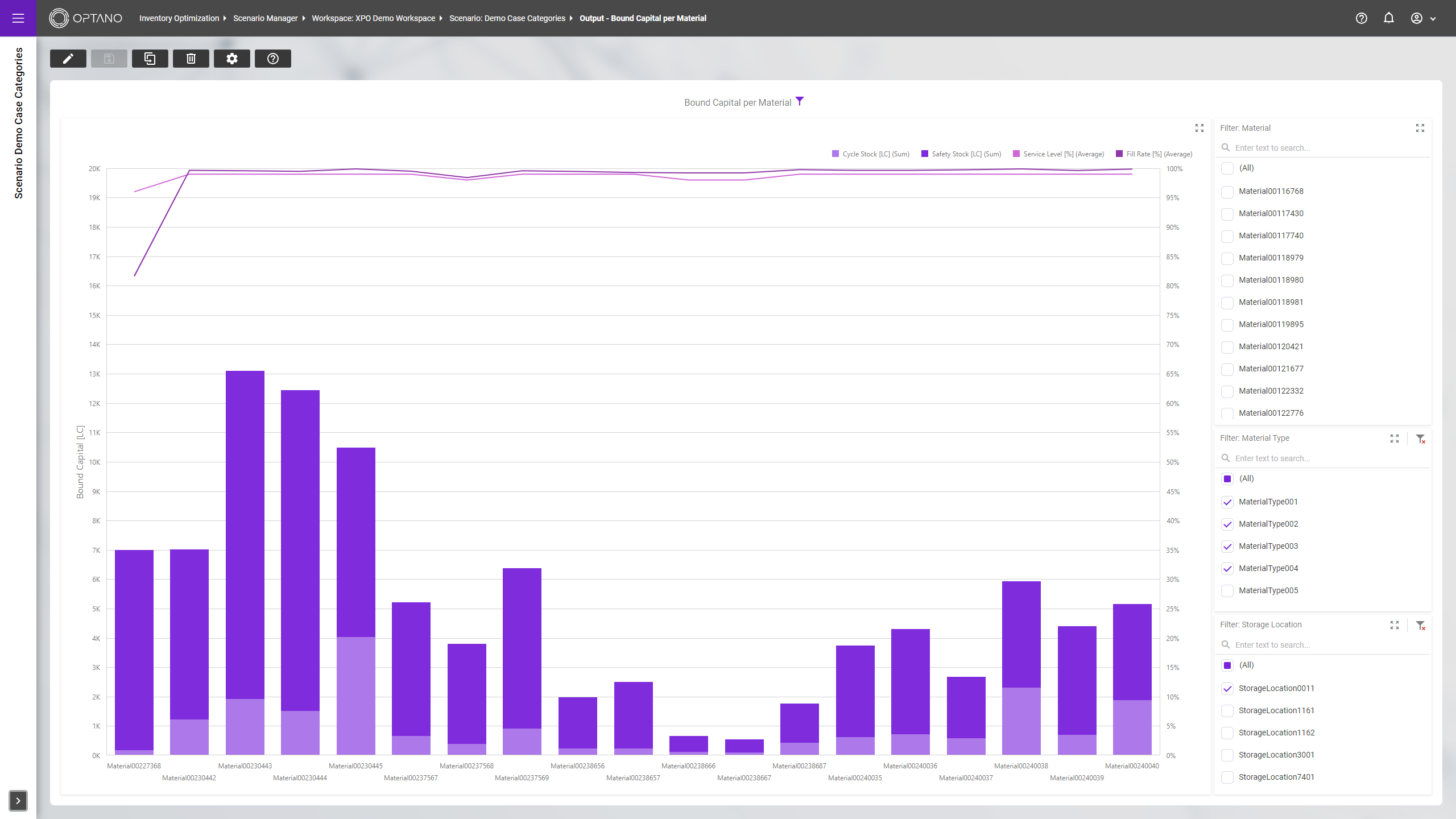
The α service level and fill rate are probably the most important KPIs for calculating optimal stock levels. As the α service level is an event-oriented KPI and the fill rate is a quantity-oriented KPI, it is worth keeping an eye on both when optimizing. OPTANO Inventory Management therefore enables the evaluation and graphical display of both values.
Factors
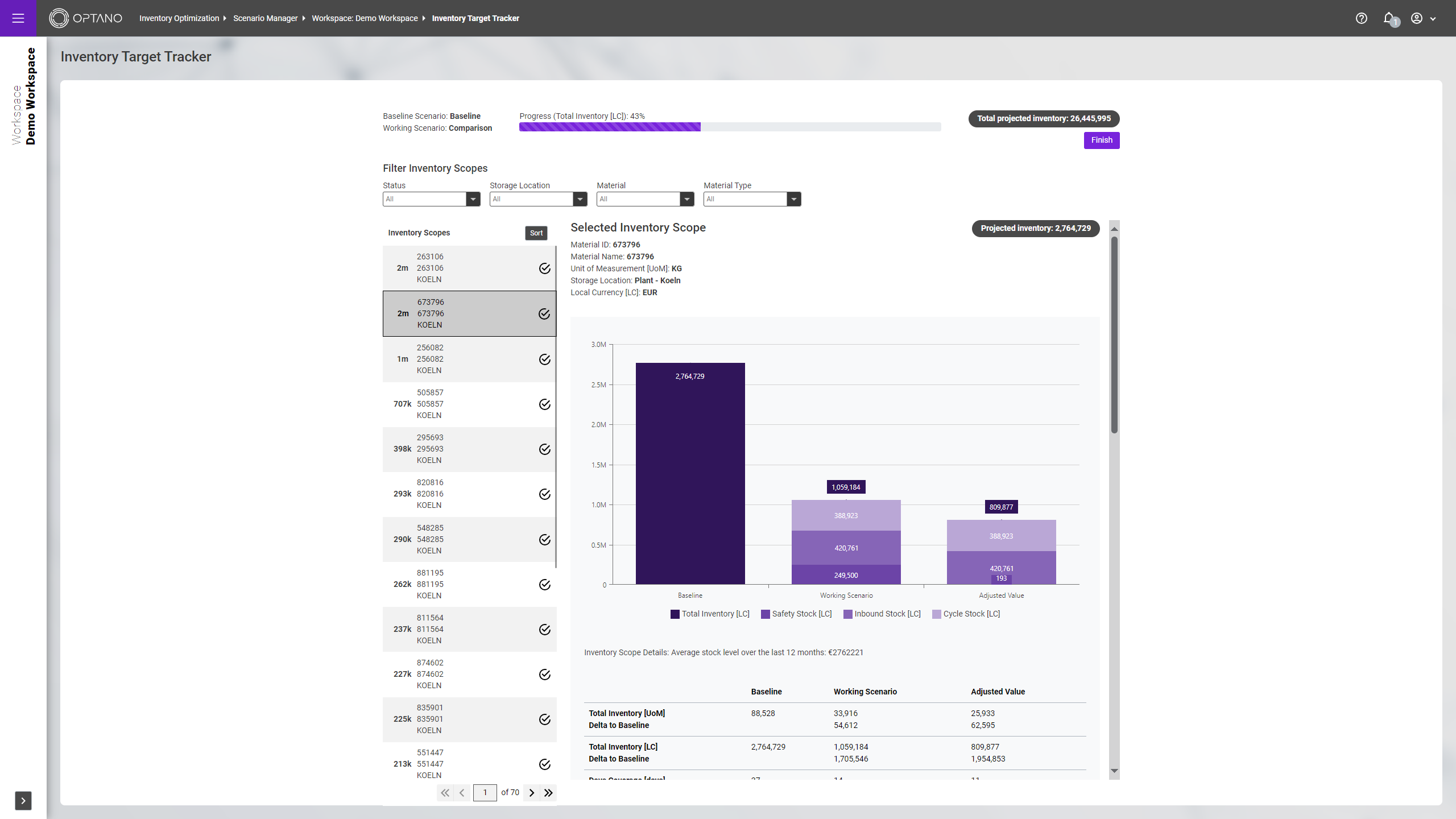
With the help of the Inventory Target Tracker, inventories can be optimized, adjustments made and concrete steps planned for improved inventory management.
Comparison of actual to target: Baseline and optimization scenarios can be selected to compare stock levels. The savings potential is clearly presented graphically and numerically.
Simple adjustment: Data validation is made easier and the main stock drivers can be individually adjusted. The effect is immediately visible in the comparison chart.
Action plan: It is possible to create specific plans for each product in order to achieve the desired inventory and exploit the identified savings potential. Contact persons can be defined, support planned and escalation measures documented.
Factors
Low
storage costs
Automated
reordering
Differentiated
setting options
Optimal
safety stocks
Higher liquidity
Minimization
of delivery bottlenecks
Higher
service level
Effective
risk modeling
Release Notes
How can we help you?
You are also welcome to use our contact form. We will then get back to you as soon as possible!
We look forward to talking to you!