Our blog posts
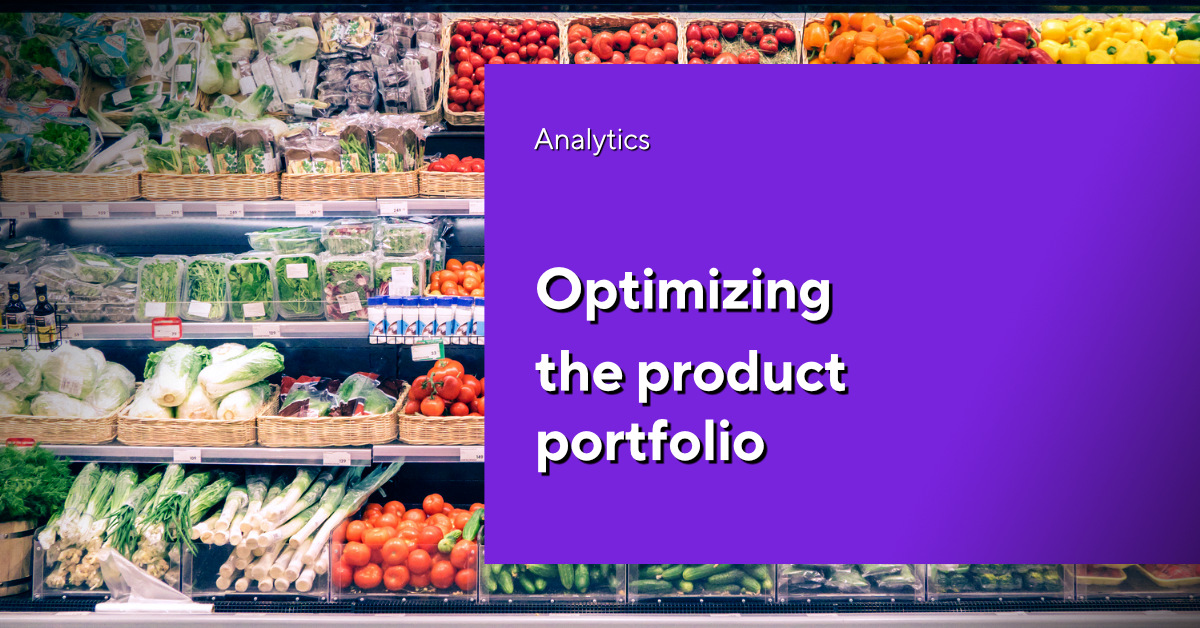
Optimizing the product portfolio
Mathematical methods help to master the countless possibilities and complex interrelationships when putting together a product portfolio. We show you how.
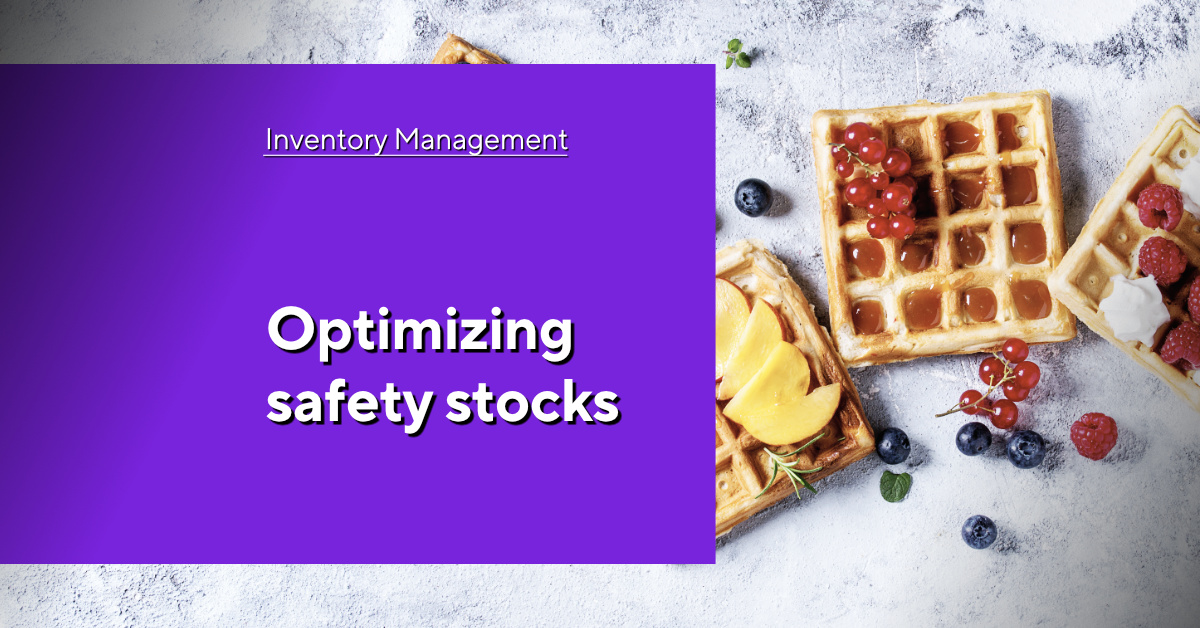
Insights: Optimizing safety stocks
High safety stocks give the good feeling of always having enough in stock, but also tie up a lot of capital. We show you how to find the optimum value.
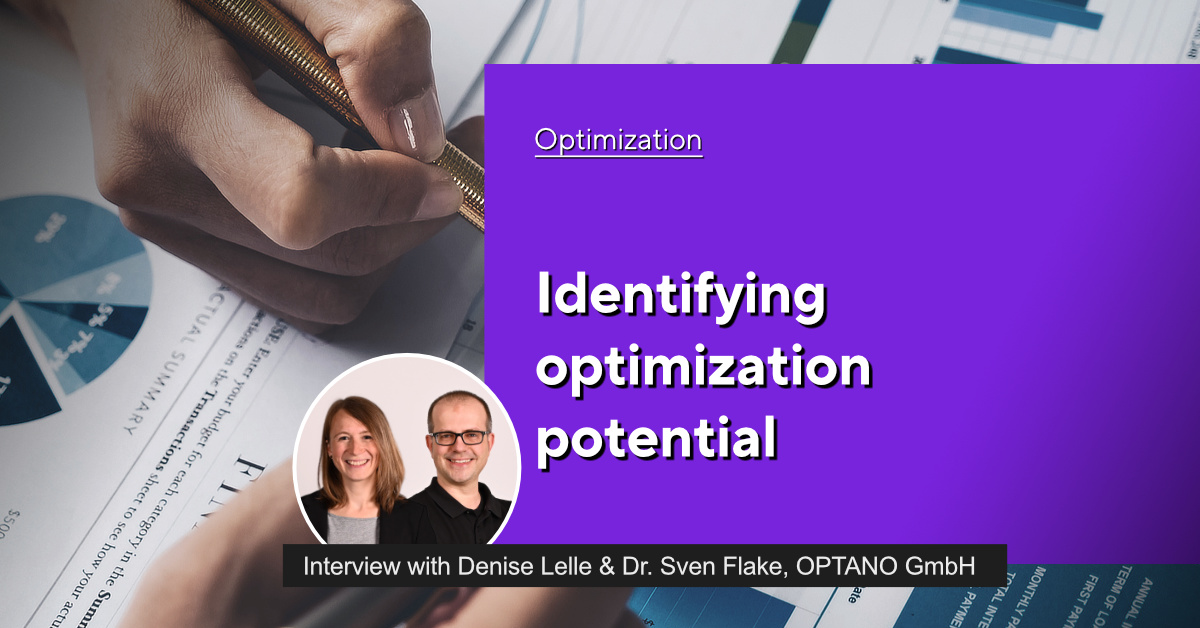
Interview: How much potential is there in optimization projects?
Denise Lelle and Dr. Sven Flake in an interview about the OPTANO workshop “Identifying optimization potential”.
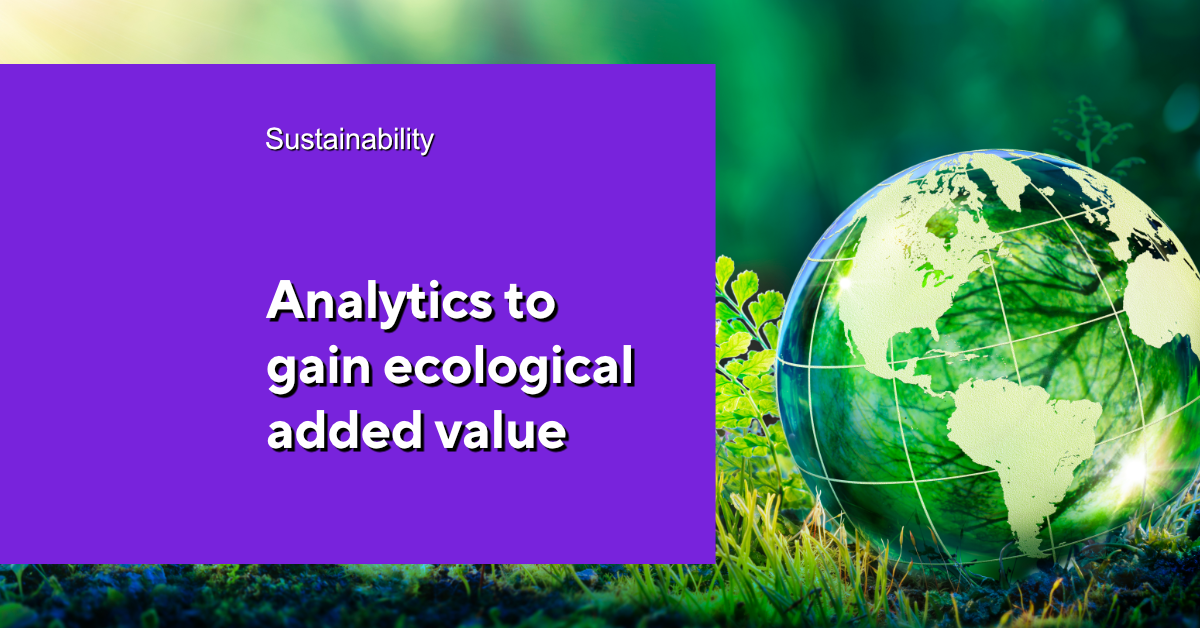
Insights: Mathematical optimization for sustainable value
How can value chains be structured optimally and be ecologically sustainable? Analytics can help and even offer a competitive edge.
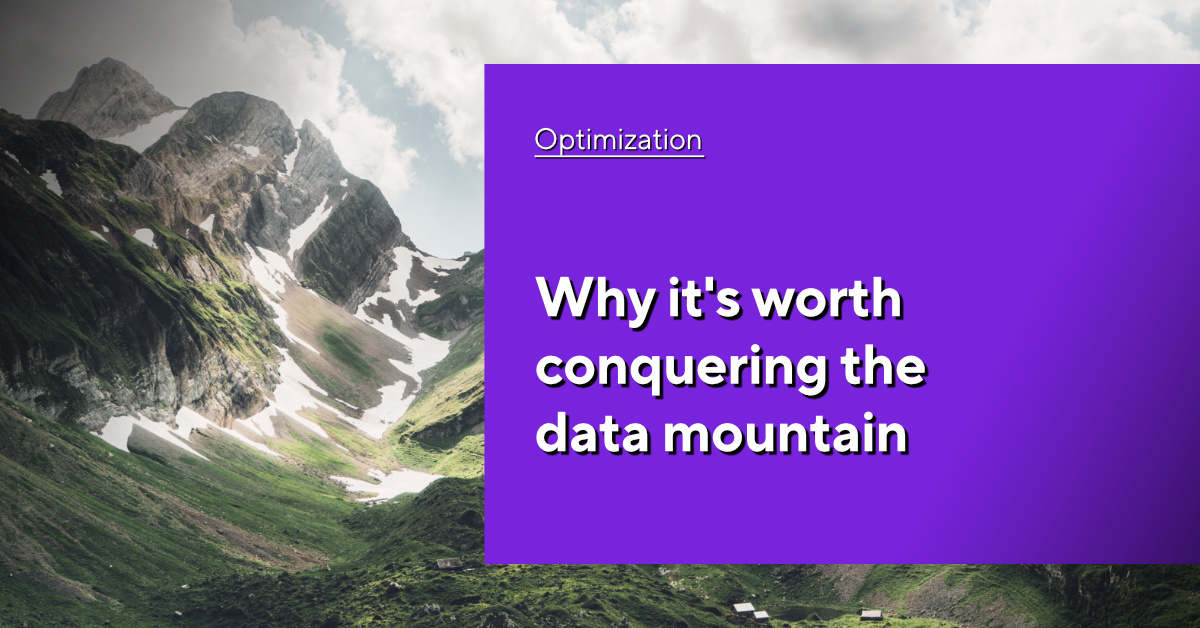
Insights: The added value of data: Why it’s worth conquering the data mountain
For many companies, the topic of data preparation seems like a huge mountain that seems impossible to climb. However, it is definitely worth tackling the climb.
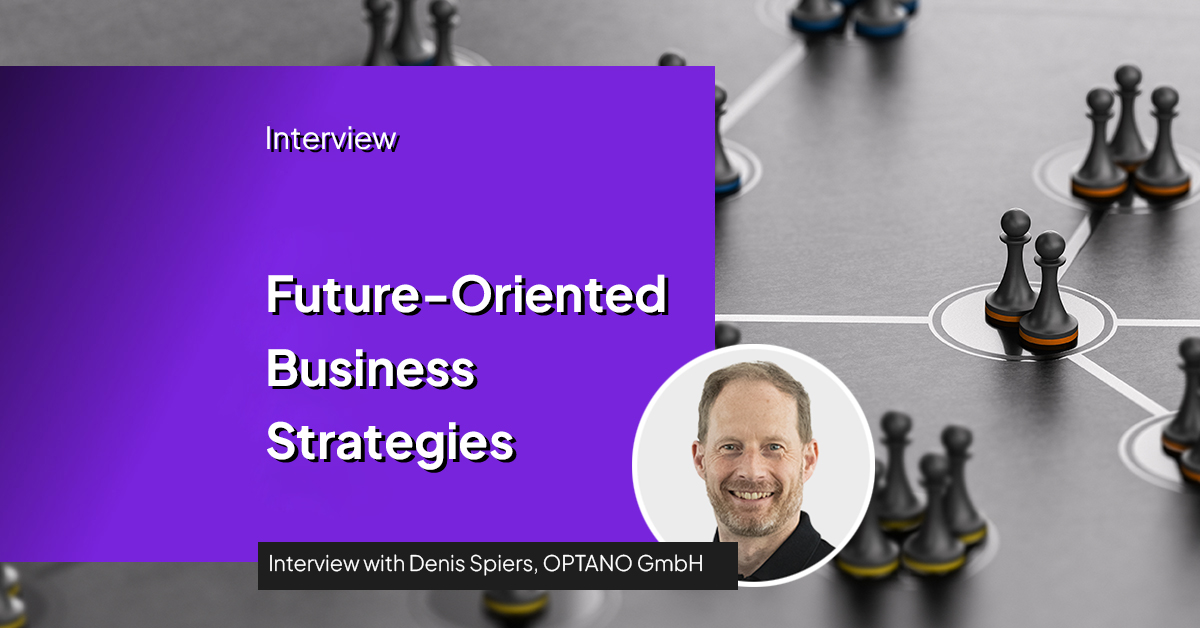
Interview: Future-Oriented Business Strategies
OPTANO is entering an exciting new chapter: Denis Spiers has joined as Head of Business Development. With his extensive experience in strategic business development and innovative optimization solutions, he brings fresh perspectives to the company.