Materialressourcen effizienter nutzen
Alles, was wir besitzen, hat seinen Ursprung in irgendeiner Form in materiellen Ressourcen. Die Materialliste eines Smartphones zum Beispiel enthält nicht weniger als 35 Elemente, die für seine Herstellung benötigt werden: Glas für den Bildschirm, Lithium für den Akku, Kupfer für die Kabel und Zink für Mikrofone und Lautsprecher, um nur einige zu nennen.
Es verfügen aber nicht nur Smartphones und andere elektronische Geräte über eine umfangreiche Materialliste. Die Ausbeutung dieser Ressourcen fordert jedoch ihren Tribut von der Natur. Angesichts des Themas „Nachhaltigkeit“ sehen sich nun auch Unternehmen gezwungen, Produkte herzustellen, die eine geringere Auswirkung auf die Umwelt und den Klimawandel haben.
In diesem Beitrag möchte wir zeigen, wie mathematische Optimierungsmethoden Unternehmen unterstützen können, Ressourcen effizienter zu nutzen – und somit langfristig auch Kosten zu sparen.
Die Nachfrage nach Materialien übersteigt bei weitem ihr Angebot
Wenn wir von materiellen Ressourcen sprechen, meinen wir Materialien, die in der Natur vorkommen und einen praktischen Wert für den menschlichen Gebrauch haben, d. h. die zur Herstellung von Gütern benötigt werden, die wir brauchen oder wollen. Bei diesen Ressourcen handelt es sich in der Regel um natürliche Ressourcen wie fossile Brennstoffe, Stein, Metall usw. Die weltweite Nachfrage nach diesen Materialien nimmt zu. Allein die deutschen Unternehmen geben jährlich 500 Milliarden Euro für Rohstoffe aus und müssen dabei mit den wachsenden Volkswirtschaften von Ländern wie China, Indien und Brasilien konkurrieren, in denen die Nachfrage sprunghaft ansteigt. Die Folgen sind stetig steigende Preise, starke Preisschwankungen und Versorgungsunsicherheiten. Es versteht sich von selbst, dass Ressourceneffizienz entscheidend ist, aber wie können Unternehmen dies erreichen?
Ressourceneffizienz fördert die Wettbewerbsfähigkeit eines Unternehmens
Ressourceneffizienz trägt einerseits zur Schonung der natürlichen Ressourcen der Erde und andererseits zur Wettbewerbsfähigkeit des eigenen Unternehmens bei, indem die Materialien in der Produktion bewusster eingesetzt werden. Nach Angaben des DEMEA-Instituts können die Rohstoffkosten eines Unternehmens um durchschnittlich ca. 20% gesenkt werden. Das sind Einsparungen, die z.B. in Form von niedrigeren Preisen an den Endverbraucher weitergegeben werden könnten. Um dies zu erreichen müssen die Unternehmen jedoch die richtige Strategie umsetzen, die langfristige Änderungen bei der Planung ihrer Betriebsabläufe und ihrer Lieferketten beinhaltet.
Eine wichtige Möglichkeit, die Effizienz zu steigern und die Kosten zu senken, besteht darin, die direkten Materialkosten während des gesamten Herstellungsprozesses zu verfolgen. Das bedeutet, dass analysiert werden muss, wie die Materialien eingekauft und zusammengesetzt werden und welche Arbeitsschritte erforderlich sind, um sie in das fertige Produkt zu integrieren:
Produktdesign- und Entwicklung
Hier werden die wichtigsten Entscheidungen über die direkten Materialien getroffen. Welche Art von Material soll verwendet werden? Welche Qualität und Menge des Materials? Eine falsche Entscheidung in diesem Bereich kann sich später bei der Herstellung als sehr kostspielig erweisen.
Die Entwickler können das Design des Produkts optimieren, um die benötigte Materialmenge so gering wie möglich zu halten. Zum Beispiel, indem sie die Größe oder das Volumen des Produkts nach Möglichkeit reduzieren. Ein weiterer wichtiger Aspekt, den es zu berücksichtigen gilt, ist die Komplexität des Produkts. Je komplexer ein Produkt ist, desto mehr Komponenten, d. h. Materialien, werden benötigt. Darüber hinaus ist ein Produkt, das in seiner Konstruktion und Planung komplex ist, schwieriger zu fertigen. Die Folge: Fehler in der Produktion, die zu Materialverschwendung führen. Produkte, die die Qualitätskontrollen nicht bestehen, müssen nachgearbeitet werden, was einem Unternehmen teuer zu stehen kommt.
Materialien zum richtigen Preis und in der richtigen Qualität einkaufen
Nachdem die Entwickler die Materialien und ihre Eigenschaften festgelegt haben, müssen die richtigen Materialien eingekauft werden. Hier gilt es, die Lieferanten sorgfältig auszuwählen und die richtige Menge unter Berücksichtigung von Preis, Qualität und Logistik zu bestimmen, um ein optimales Kosten-Nutzen-Verhältnis zu erzielen.
Der Preis ist natürlich ein entscheidender Faktor. Die Rohstoffpreise sind starken Schwankungen unterworfen, so dass es sinnvoll ist, sie zu kaufen, wenn die Preise niedrig sind. Eine Auswahl an zuverlässigen Lieferanten zu haben kann den Einkäufern einen beträchtlichen Vorteil verschaffen, da es so leichter ist, wettbewerbsfähige Preise auszuhandeln. Ein weiterer Faktor, den es zu berücksichtigen gilt, ist das Risiko eines Wertverlustes. Dieses lässt sich verringern, indem Durchlaufzeiten und Bestände so gering wie möglich gehalten werden, um unnötig lange Lagerzeiten und Materialschäden zu vermeiden. Eine Lösung kann hier die Just-in-Time-Lieferung für bestimmte Produkte sein, die sicherstellt, dass nicht mehr Bestände als nötig im Lager sind. Die Vor- und Nachteile dieser Methode müssen jedoch sehr sorgfältig abgewogen werden. Weitere Informationen hierzu finden Sie in unserem Blog Optimiertes Bestandsmanagement
Produktionsprozesse neu bewerten
In der Produktion fällt ein hoher Anteil an Materialabfällen an. Dies kann ein Zeichen dafür sein, dass die Maschinen nicht so effizient arbeiten, wie sie sollten, und somit Waren produzieren, die nicht den Qualitätsanforderungen entsprechen. Dies führt zu zusätzlichen Kosten für Nacharbeit, Korrekturen und Entsorgungskosten für Ausschuss. Dieser kann in erheblichem Maße reduziert werden. Durch die Bewertung ihrer Produktionsverfahren und -maschinen können Unternehmen ineffiziente Bereiche aufdecken und Maßnahmen zur Verbesserung dieser Bereiche ergreifen. Hier ist eine regelmäßige (vorausschauende) Wartung von Maschinen und Prozessen entscheidend. Sind die Maschinen jedoch älter oder technisch nicht mehr auf dem neuesten Stand, kann es auf lange Sicht gewinnbringend sein, in neue zu investieren, die eine bessere Leistung erbringen und auch energieeffizienter arbeiten.
Weitere interessante Beiträge
Effizienzsteigerung benötigt eine optimale Planung
Wie oben beschrieben, erfordert die effiziente Nutzung von Materialressourcen, dass F&E, Produktion und Einkauf zusammenarbeiten, um die Effizienz zu steigern. Schließlich sind sie alle an der Entscheidungsprozess beteiligt, welche Materialien zu welchem Zeitpunkt in welcher Menge benötigt werden. Abteilungsübergreifende Planungsprozesse können jedoch sehr komplex werden, egal wie gut sie miteinander kooperieren. Das liegt daran, dass jede Abteilung ihre eigenen Restriktionen, Variablen und Zielsetzungen hat. Dies führt bei der Planung zu Zielkonflikten und man kann leicht das gemeinsame Ziel aus den Augen verlieren.
Gefragt ist eine Planungssoftware, die Unternehmen dabei unterstützt, Produktionsabläufe, Bestellvorgänge und Bestandsmanagement zu optimieren und die Querabhängigkeiten in Planungsprozessen zu erkennen. Auf diese Weise können fundierte Entscheidungen zum effizienten Einsatz von Ressourcen getroffen werden.
Die richtige Planung benötigt die richtige Software: OPTANO kann helfen
Die Zeit wird knapp - unsere Ressourcen auch
Kennen Sie schon unser Factsheet zum Thema?
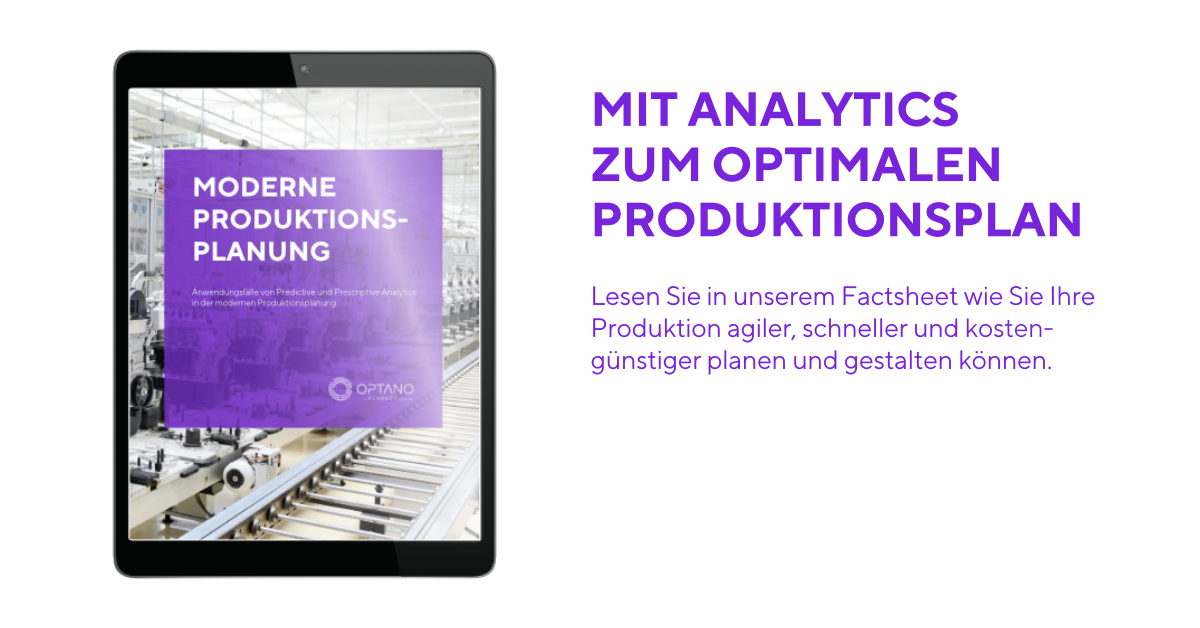
Wir haben Anwendungsfälle von Predictive und Prescriptive Analytics in der modernen Produktionsplanung in einem Factsheet zusammengestellt. Dieses können Sie hier herunterladen.
Um dieses Factsheet zu erhalten, müssen Sie nur Ihre Kontaktdaten in das untenstehende Formular eintragen. Es öffnet sich dann ein Pop-up-Fenster zum Downloaden des Whitepapers. Bitte beachten Sie, dass Sie mit der Angabe Ihrer E-Mail-Adresse zustimmen, dass wir Sie zu diesem Thema kontaktieren dürfen. Sie können diese Zustimmung jederzeit widerrufen, indem Sie sich an [email protected] wenden.